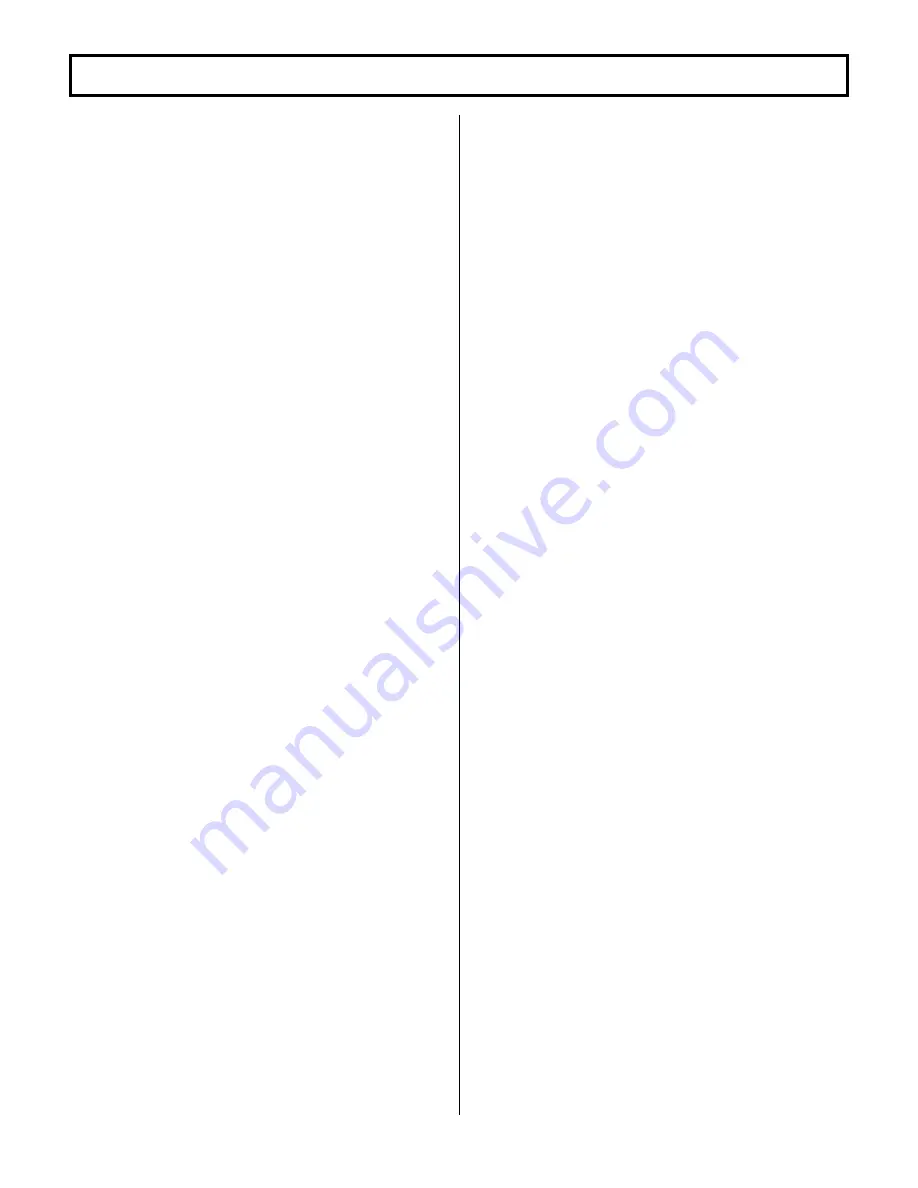
BASIC OPERATION AND FEATURES
SX TRANSISTOR CONTROL
Page 5
July 2002
Section 2. FEATURES OF SX FAMILY OF TRANSISTOR
MOTOR CONTROLLERS
Section 2.1 Performance
Section 2.1.1 Oscillator Card Features
Section 2.1.1.a Standard Operation
The oscillator section of the card has two adjustable
features, creep speed and minimum field current. The
creep speed can be adjusted by Function 2 of the handset.
The field control section allows the adjustment of the field
weakening level in order to set the top speed of the motor.
This top speed function (Minimum Field Current) is enabled
when the armature current is less than the value set by
Function 24. Top Speed can be adjusted by Function 7 of
the handset .
The % ON-time has a range of approximately 0 to 100
percent. The SX controllers operate at a constant
frequency and the % ON-time is controlled by the pulse
width of the voltage/current applied to the motor circuits.
Section 2.1.1.b Control Acceleration
This feature allows for adjustment of the rate of time it
takes for the control to accelerate to 100% applied battery
voltage to the motor on hard acceleration. Armature C/A is
adjusted by Function 3 from 0.1 to 22 seconds.
Section 2.1.2 Current Limit
This circuit monitors motor current by utilizing sensors in
series with the armature and field windings. The
information detected by the sensor is fed back to the card
so that current may be limited to a preset value. If heavy
load currents are detected, this circuit overrides the
oscillator and limits the average current to a value set by
Function 4 and Function 8 of the Handset. The C/L setting is
based on the maximum thermal rating of the control.
Because of the flyback current through 3REC, the motor
current is usually greater than battery current, except at
100% ON time.
Section 2.1.3 Plug Braking
Slow down is accomplished when reversing direction by
providing a small amount of retarding torque for
deceleration. If the vehicle is moving, and the directional
lever is moved from one direction to the other, the plug
signal is initiated. Once the plug signal has been initiated,
the field is reversed, and the armature current is regulated
to the plug current limit as set by Function 5. Armature
current is regulated by increasing the field current as the
vehicle slows down. Once the field current reaches a
preset value, set by Function 10, and armature plug current
can no longer be maintained, the braking function is
canceled, and the control reverts back to motoring.
All energy produced by the motor during plugging is
dumped as heat in the motor in this braking mode.
Section 2.1.4 Regenerative Braking to Base Speed
Regenerative braking to base speed is a function of the
vehicle motor design which slows the vehicle to a speed
corresponding to the base speed of the motor whenever the
start switch is opened or the control detects an overspeed
condition. The field FETs pulse on/off to regulate the
armature current. During regen, armature current is
allowed to flow from the armature through the current
sensor, the battery, the armature transistor and back to the
armature. All regen current is returned to the battery.
Regen current will continue to flow until the speed of the
motor drops below its base speed, at which point the
vehicle will coast.
Section 2.1.5 Auxiliary Speed Control
Section 2.1.5.a Field Weakening
This function allows the adjustment of the field weakening
level in order to set the top speed of the motor. The function
is enabled when the armature current is less than the value
set by Function 24 and the accelerator input voltage is
greater than 2.9 volts. It is important to note that this
function is used to optimize motor and control
performance, and this setting will be determined by GE and
OEM engineers at the time of vehicle development. This
setting must not be changed by field personnel without the
permission of the OEM.
Section 2.1.5.b Speed Limits
This feature provides a means to control speed by limiting
motor volts utilizing "adjustable speed limits", initiated by
individual limit switches. The NC switches are connected
between input points on the control card and battery
positive. The lower motor volt limit always takes priority
when more than one switch input is open. This motor volt
limit regulates top speed of the transistor controller, but
actual vehicle speed will vary at any set point depending on
the loading of the vehicle.
Section 2.1.5.c Top Speed Regulation
This feature requires a system tachometer. The standard
GE system tach is built into the motor and provides four
pulses per armature revolution. Once the control has been
calibrated to the vehicle parameters (gear ratio
and wheel rolling radius), using Function 1, speed can be
measured with a resolution of +/- 1 mph. When traveling
down an incline, if the vehicle speed increases to the
overspeed setting, the control automatically transitions to