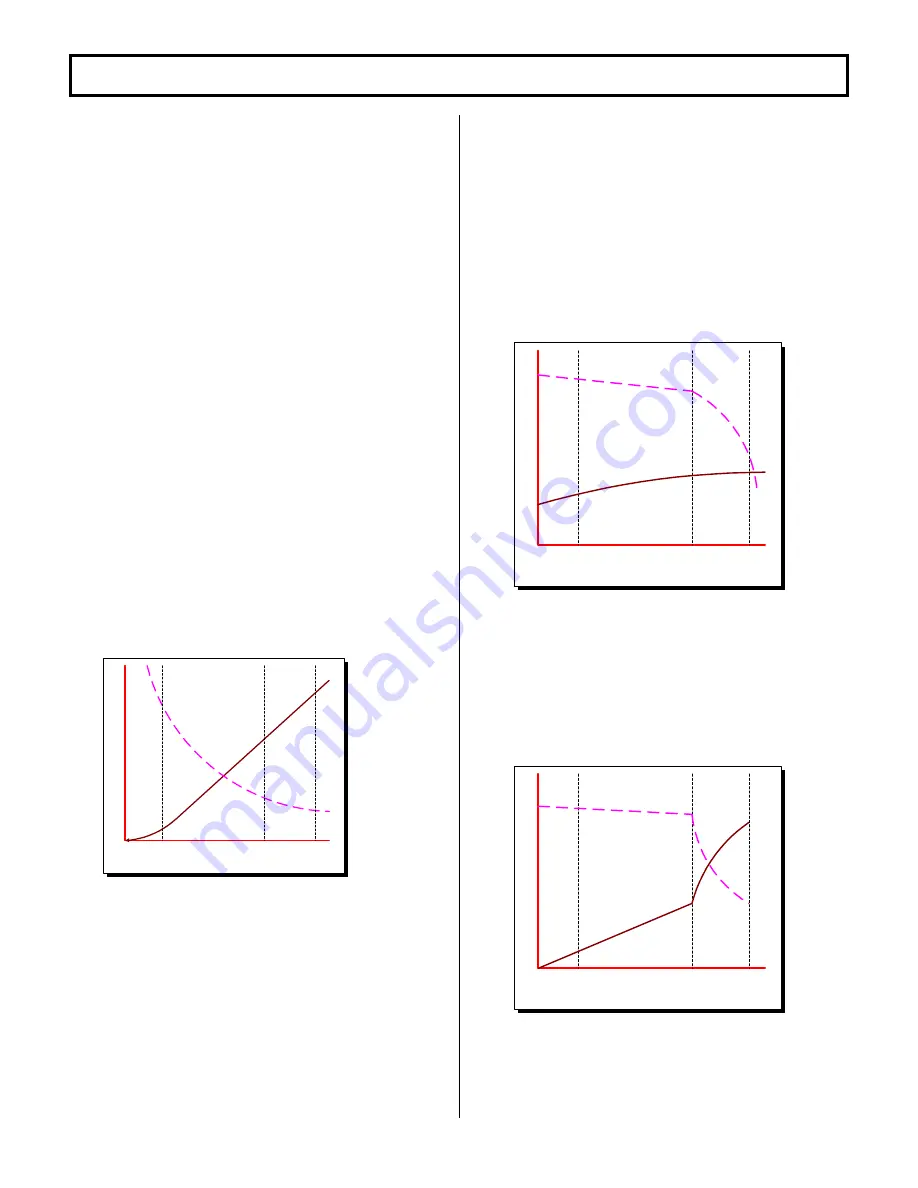
BASIC OPERATION AND FEATURES
SX TRANSISTOR CONTROL
Page 3
July 2002
Section 1. INTRODUCTION
Section 1.1 Motor Characteristics
The level of sophistication in the controllability of traction
motors has changed greatly over the past several years.
Vehicle manufacturers and users are continuing to expect
more value and flexibility in electric vehicle motor and
control systems as they are applied today. In order to
respond to these market demands, traction system
designers have been forced to develop new approaches to
reduce cost and improve functions and features of the
overall system. Development is being done in a multi-
generational format that allows the market to take
advantage of today’s technology, while looking forward to
new advances on the horizon. GE has introduced a second
generation system using separately excited DC shunt
wound motors. The separately excited DC motor system
offers many of the features that are generally found on the
advanced AC systems. Historically, most electric vehicles
have relied on series motor designs because of their ability
to produce very high levels of torque at low speeds. But, as
the demand for high efficiency systems increases, i.e.,
systems that are more closely applied to customers’
specific torque requirements, shunt motors are now often
being considered over series motors. In most applications,
by independently controlling the field and armature
currents in the separately excited motor, the best attributes
of both the series and the shunt wound motors can be
combined.
NO
LO
AD
CU
RRE
NT
FU
LL
LO
AD
CU
RRE
NT
ST
AR
TIN
G
CU
RRE
NT
ARMATURE CURRENT
Figure 1
SPEED
TORQUE
As shown in the typical performance curves of Figure 1, the
high torque at low speed characteristic of the series motor
is evident.
In a shunt motor, the field is connected directly across the
voltage source and is therefore independent of variations in
load and armature current. If field strength is held
constant, the torque developed will vary directly with the
armature current. If the mechanical load on the motor
increases, the motor slows down, reducing the back EMF
(which depends on the speed, as well as the constant field
strength). The reduced back EMF allows the armature
current to increase, providing the greater torque needed to
drive the increased mechanical load. If the mechanical
load is decreased, the process reverses. The motor speed
and the back EMF increase, while the armature current and
the torque developed decrease. Thus, whenever the load
changes, the speed changes also, until the motor is again
in electrical balance.
In a shunt motor, the variation of speed from no load to
normal full load on level ground is less than 10%. For this
reason, shunt motors are considered to be constant speed
motors (Figure 2).
NO
LO
AD
CU
RR
ENT
FU
LL
LO
AD
CU
RRE
NT
ST
ART
ING
CU
RRE
NT
ARMATURE CURRENT
Figure 2
SPEED
TORQUE
In the separately excited motor, the motor is operated as a
fixed field shunt motor in the normal running range.
However, when additional torque is required, for example,
to climb non-level terrain, such as ramps and the like, the
field current is increased to provide the higher level of
torque. In most cases, the armature to field ampere turn
ratio can be very similar to that of a comparable size series
motor (Figure 3.)
NO
LO
AD
CU
RR
ENT
FU
LL
LO
AD
CU
RRE
NT
ST
ART
ING
CU
RRE
NT
ARMATURE CURRENT
Figure 3
SPEED
TORQUE
Aside from the constant horsepower characteristics
described above, there are many other features that
provide increased performance and lower cost. The
following description provides a brief introduction to some
of these features.