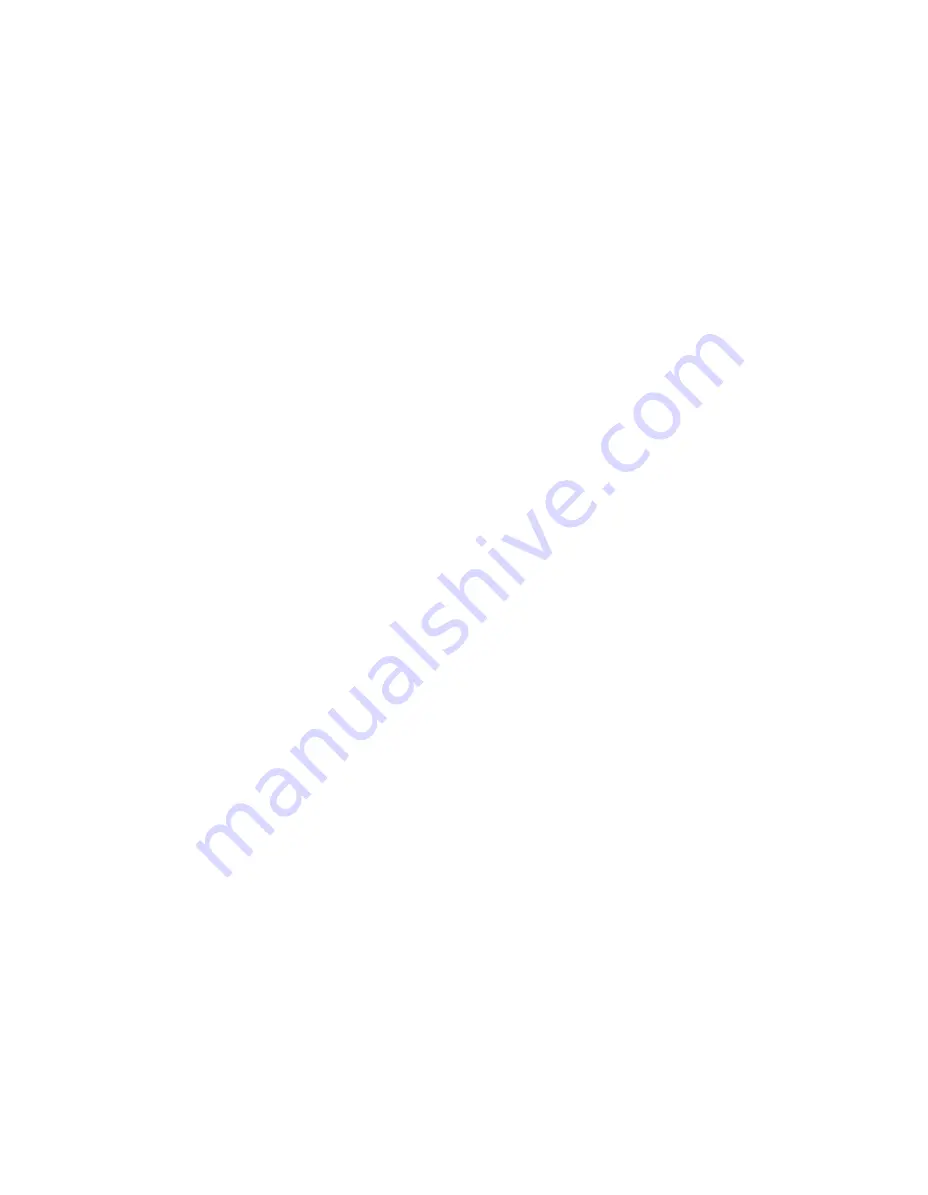
GEK-65525
CONSTRUCT! ON
The type CCP13E relay is mounted in an M2-size case.
The case has studs at both
ends in the rear for external connections. The outline and panel drilling for this
case is shown in Figure 3.
The electrical connections between the relay units and the case studs are made
through stationary molded inner and outer blocks, between which nests a removable
connection plug that completes the circuits. The outer blocks attached to the case
have the studs for the external connections and the inner blocks have the terminals
for the internal connections.
Every circuit in the drawout case has the auxiliary brush, as shown in Figure 4, to
provide adequate overlap when the connecting plug is withdrawn or inserted.
Some
circuits are equipped with shorting bars
(
see internal connections in Figure 5), and
on those circuits it is especially important that the auxiliary brush make contact,
as indicated in Figure 4, with adequate pressure to prevent the opening of important
interlocking circuits.
The relay mechanism is mounted in a steel framework called the cradle, and is a
complete unit with all leads terminated at the inner block.
This cradle is held
firmly in the case by a latch at both top and bottom and by a guide pin at the back
of the case. The connection plug, besides making the electrical connections between
the respective blocks of the cradle and case, also locks the latch in place.
The
cover, which is drawn to the case by thumbscrews, holds the connecting plugs in
place.
The relay case is suitable for either semiflush or
to two inches thick, and appropriate hardware
thickness must be indicated on the relay order to
be included.
surface mounting on all panels up
is available.
However, panel
insure that proper hardware will
These relays are induction-cylinder devices for alternating-current (AC) circuits.
The principle by which torque is developed is the same as that employed in an
induction-disk relay with a watthour meter element, though in arrangement of parts
they are more like split-phase induction motors.
The stator of each unit has eight laminated magnetic poles projecting inward and
arranged symmetrially around a central magnetic core.
The poles are fitted with
current and potential coils; four potential coils that are internally connected,
forming a single circuit, as well as four current coils similarly connected. In the
annular air gap between the poles and central core is the cylindrical part of the
cup-like aluminum rotor, which turns freely in the air gap.
The central core is
fixed to the stator frame; the rotor alone turns. The three units are mounted one
on top of the other. The three rotors are mounted on a single shaft.
This construction provides higher torque and lower rotor inertia than the induction
disk construction, thus making these relays faster and more sensitive.
The directional contacts
(
see Figure 6) are especially constructed to suppress
bouncing. The stationary contact
(G)
is mounted on a flat spiral spring
(
F
)
, backed
up by a thin diaphragm (C).
These are both mounted in a slightly inclined tube (A).
5
www
. ElectricalPartManuals
. com