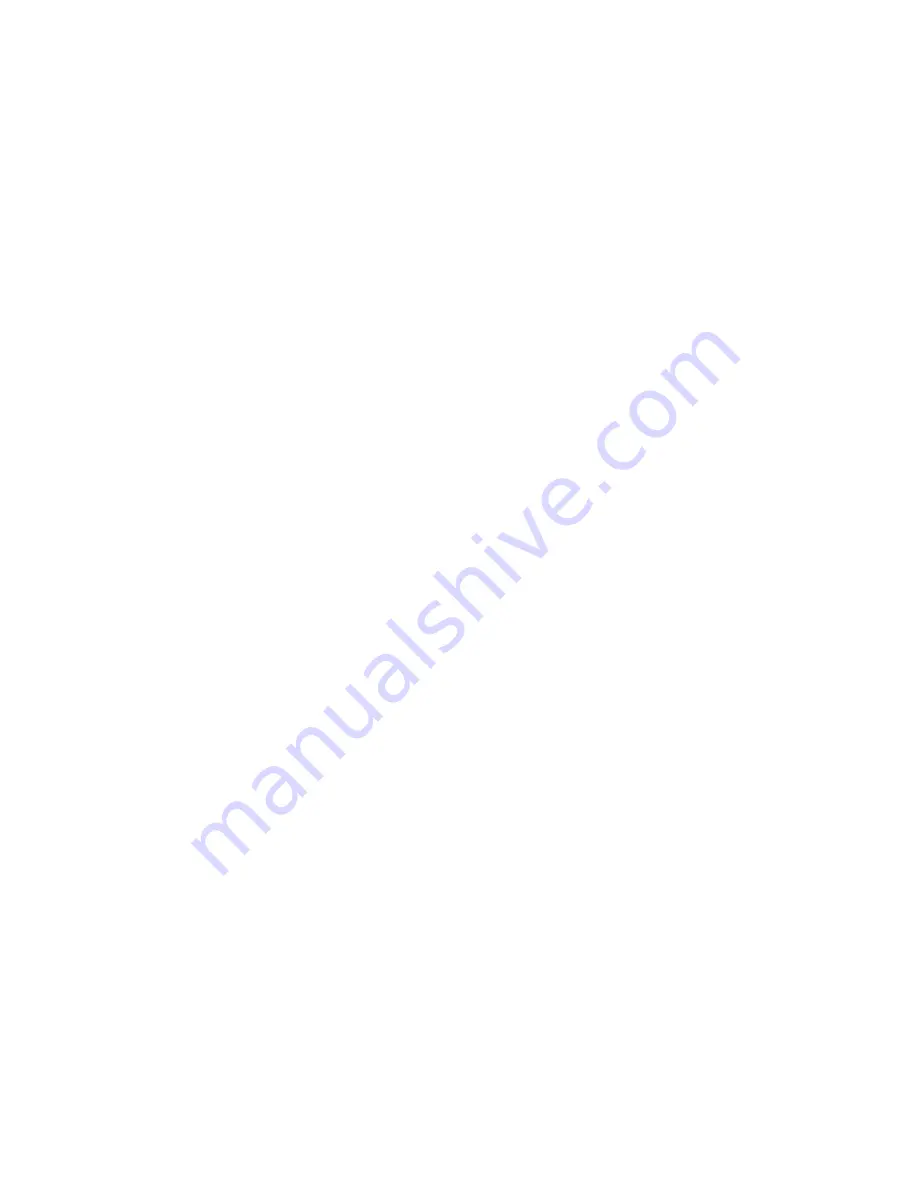
GEK-65525
BEARINGS
The lower jewel screw can be removed from the unit by means of an offset screwdriver
or an end wrench.
The jewel may be tested for cracks by exploring its surface with
the point of a fine needle.
If it is necessary to replace the jewel, a new pivot
should be screwed into the bottom of the shaft at the same time.
The lower jewel bearing should be screwed all the way in until its head engages the
end of the threaded core.
The upper bearing should be adjusted to allow about 1/32
inch end play of the shaft.
Press down on the contact arm near the shaft to check the clearance between the iron
core and the inside of the rotor cup; this will depress the spring-mounted jewel
until the cup strikes the iron; the shaft should move about 1/16 inch.
VOLTAGE BIAS
1.
Unwind the upper control spring until the moving contact assembly is floating
approximately half way between the right contact and the left contact.
This
should be done with the relay mounted in a level position and with no voltage
or current applied to the relay.
2.
Apply rated three-phase voltage to the potential circuit, using the same
connections as shown on the external connection diagram (Figure 2).
With no
current in the current coils, the moving contact should stay in the float
position set in Step 1.
Should the moving contact arm move enough to close the
right or left contact, it will be necessary to readjust the core.
The core is
adjusted by loosening the core locknut and rotating the core slightly to the
right or left to return the moving contact arm to its floating position.
The
core locknut is located in the center of the lower iron casting.
The core is
turned by putting an offset screwdriver into the jewel screw slot. The locknut
shou
1
d only be
1
oosened enough to a
11
ow the core to be turned.
When the
contact assembly is set for the float position by turning the core, the locknut
should be tightened.
Recheck that the moving contact assembly is still
floating when the locknut is tight.
POLARITY
The polarity of the coils can be checked using the connections of Figure 10.
Each
unit is checked separately, and each should produce a torque in the direction to
close the left contact.
If in any of the three tests the torque is in the direction to close the
right
contact, the polarity is reversed.
To correct the polarity, the connections of that
potential circuit should be reversed at the cradle terminals.
For example, if the
polarity was reversed when the top unit was tested, then the potential coil lead to
terminal 13 should be moved to terminal 14, and the lead going to terminal 14 should
be connected to terminal 13.
ANGLE OF MAXIMUM TORQUE
If the maximum angle of torque (30° lead) of the relay has been disturbed, it may be
restored by referring to Figure 12.
With rated voltage and frequency applied to the
potential circuit, and 5 amperes flowing in the current circuit, the potential
13
www
. ElectricalPartManuals
. com