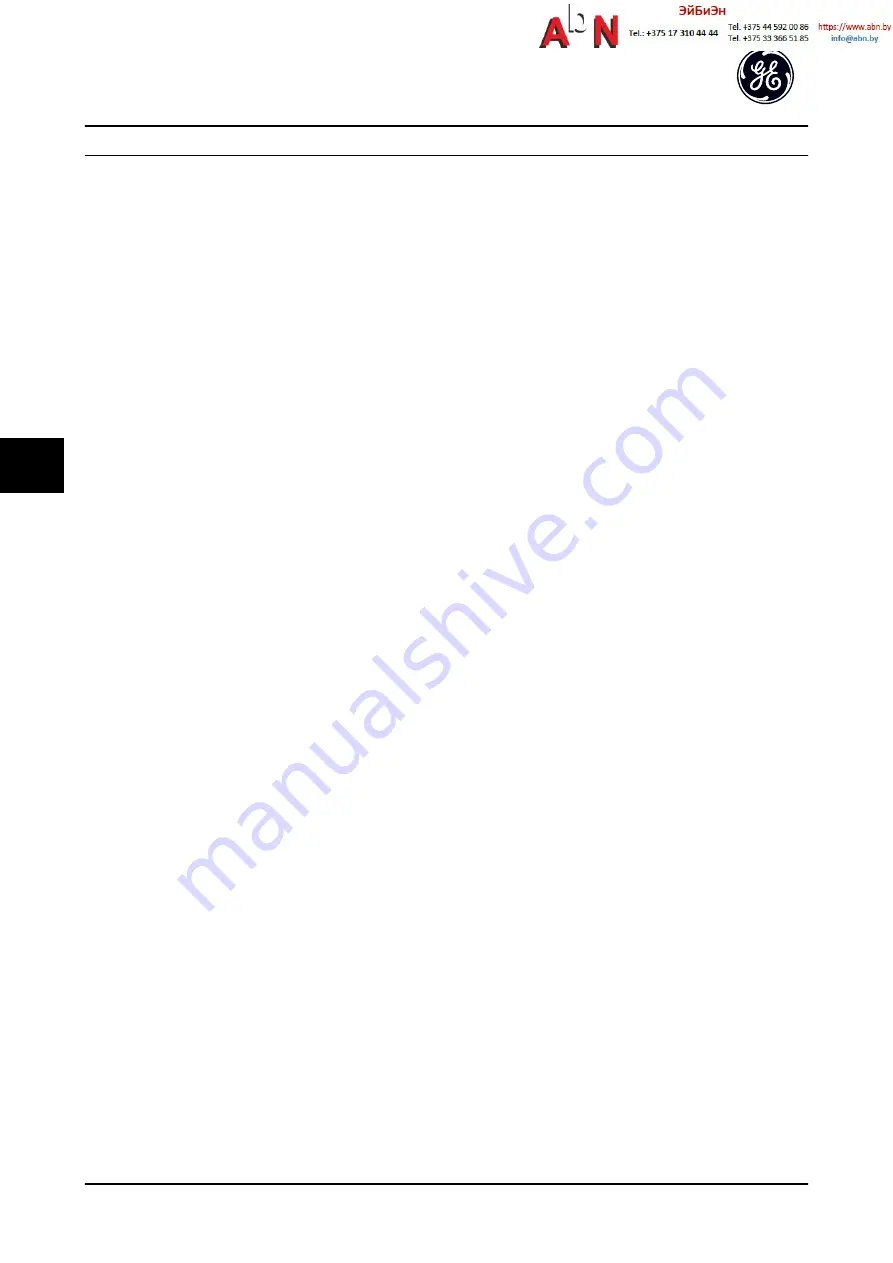
Optimization of the process regulator
The basic settings have now been made; all that needs to
be done is to optimize the proportional gain, the
integration time and the differentiation time (
PI-33 Process
PID Proportional Gain
,
PI-34 Process PID Integral Time
,
PI-35 Process PID Differentiation Time
). In most processes,
this can be done by following the guidelines given below.
1.
Start the motor
2.
Set
PI-33 Process PID Proportional Gain
to 0.3 and
increase it until the feedback signal again begins
to vary continuously. Then, reduce the value until
the feedback signal has stabilized. Now lower the
proportional gain by 40–60%.
3.
Set
PI-34 Process PID Integral Time
to 20 s and
reduce the value until the feedback signal again
begins to vary continuously. Increase the
integration time until the feedback signal
stabilizes, followed by an increase of 15%–50%.
4.
Only use
PI-35 Process PID Differentiation Time
for
very fast-acting systems only (differentiation
time). The typical value is four times the set
integration time. The differentiator should only be
used when the setting of the proportional gain
and the integration time has been fully
optimized. Make sure that oscillations in the
feedback signal are sufficiently damped by the
low-pass filter on the feedback signal.
NOTE!
If necessary, start/stop can be activated a number of times
in order to provoke a variation of the feedback signal.
6.6 Brake
Functions
The brake function is applied for braking the load on the
motor shaft, either as dynamic braking or static braking.
6.6.1 Mechanical Holding Brake
A mechanical holding brake mounted directly on the
motor shaft normally performs static braking. In some
applications, the static holding torque statically holds the
motor shaft (usually synchronous permanent motors). A
holding brake is either controlled by a PLC or directly by a
digital output from the adjustable frequency drive (relay or
solid state).
NOTE!
When the holding brake is included in a safety chain:
An adjustable frequency drive cannot safely control a
mechanical brake. A redundancy circuit for the brake
control must be a part of the total installation.
6.6.2 Dynamic Braking
Dynamic Brake established by:
•
Resistor brake: A brake IGBT keeps the
overvoltage under a certain threshold by
directing the braking energy from the motor to
the connected brake resistor (
B-10 Brake Function
= [1]).
•
AC brake: The braking energy is distributed in the
motor by changing the loss conditions in the
motor. The AC brake function cannot be used in
applications with high cycling frequency since
this will overheat the motor (
B-10 Brake Function
= [2]).
•
DC brake: An over-modulated DC current added
to the AC current works as an eddy current brake
(par. B-02 and B-03
≠
off).
6.6.2.1 Selection of Brake Resistor
To handle higher demands by generatoric braking, a brake
resistor is necessary. Using a brake resistor ensures that the
energy is absorbed in the brake resistor and not in the
adjustable frequency drive. For more information, see the
Brake Resistor Design Guide, DET-700
If the amount of kinetic energy transferred to the resistor
in each braking period is not known, the average power
can be calculated on the basis of the cycle time and
braking time also called intermittent duty cycle. The
resistor intermittent duty cycle is an indication of the duty
cycle at which the resistor is active. The below figure
shows a typical braking cycle.
NOTE!
Motor suppliers often use S5 when stating the permissible
load which is an expression of intermittent duty cycle.
The intermittent duty cycle for the resistor is calculated as
follows:
Duty cycle = t
b
/T
T = cycle time in s
t
b
is the braking time in s (of the cycle time)
Application Setup Examples
AF-650 GP
TM
Design and Installation Guide
6-22
DET-767A
6
6
Содержание AF-650 GP Series
Страница 3: ...Safety AF 650 GPTM Design and Installation Guide DET 767A ...
Страница 9: ...Contents AF 650 GPTM Design and Installation Guide DET 767A ...
Страница 19: ...Introduction AF 650 GPTM Design and Installation Guide 1 10 DET 767A 1 1 ...
Страница 35: ...Installation AF 650 GPTM Design and Installation Guide 2 16 DET 767A 2 2 ...
Страница 41: ...Start Up and Functional Tes AF 650 GPTM Design and Installation Guide 3 6 DET 767A 3 3 ...
Страница 55: ...About Programming AF 650 GPTM Design and Installation Guide 5 10 DET 767A 5 5 ...
Страница 91: ...Application Setup Examples AF 650 GPTM Design and Installation Guide 6 36 DET 767A 6 6 ...
Страница 103: ...Status Messages AF 650 GPTM Design and Installation Guide 8 4 DET 767A 8 8 ...
Страница 123: ...Warnings and Alarms AF 650 GPTM Design and Installation Guide 10 10 DET 767A 10 0 ...
Страница 127: ...Basic Troubleshooting AF 650 GPTM Design and Installation Guide 11 4 DET 767A 11 1 ...
Страница 129: ...Terminal and Applicable Wir AF 650 GPTM Design and Installation Guide 12 2 DET 767A 12 2 ...
Страница 161: ...Specifications AF 650 GPTM Design and Installation Guide 13 32 DET 767A 13 3 ...