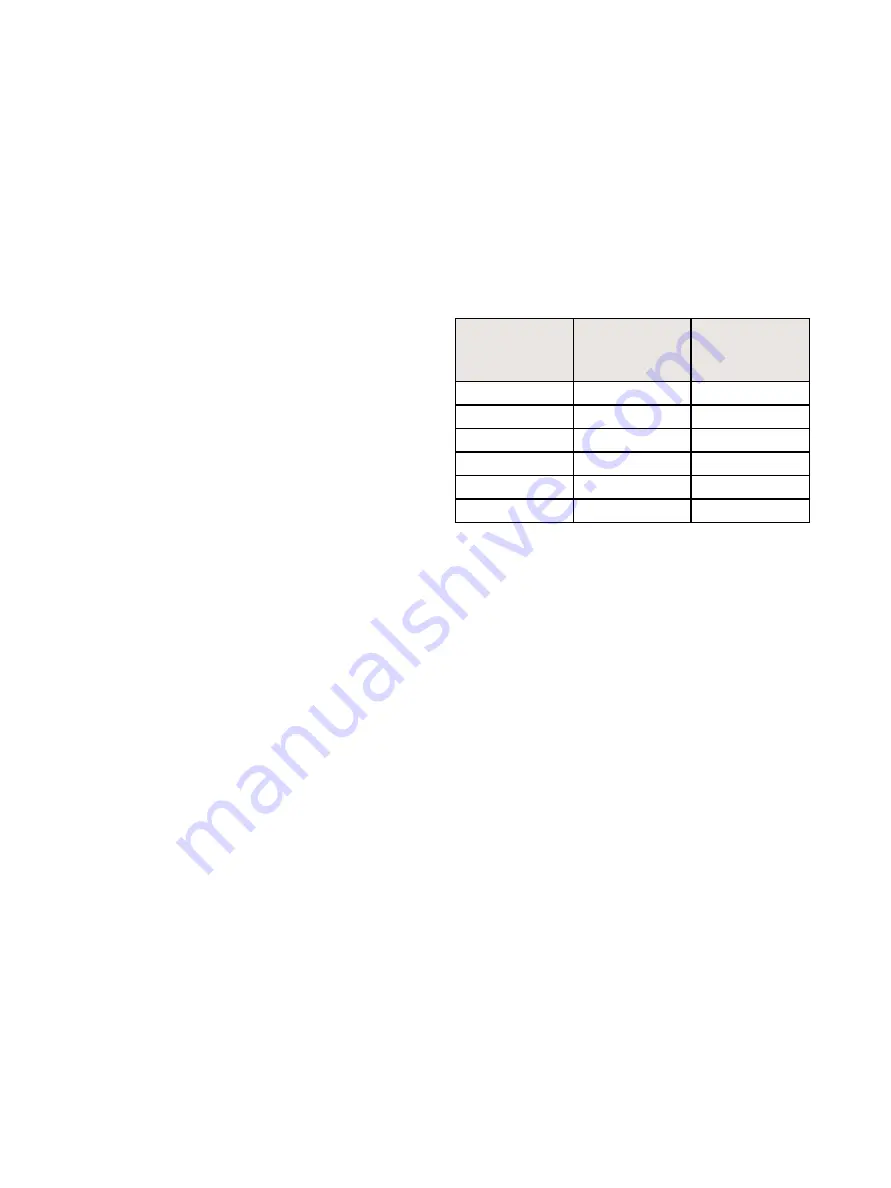
4 |
GE Oil & Gas
© 2014 General Electric Company. All rights reserved.
Description
The spring-diaphragm actuator is a simple, powerful,
mechanical device. There are two general types:
Air-to-Extend Stem and Air-to-Retract Stem. Actuators
are designated by case size: Nos. 9, 11, 13, 15, 18
and 18L.
The nominal range of a spring-diaphragm actuator is
the air pressure range in pounds per square inch (psi)
for rated stroke under no load. Common ranges are
3–15 psi and 6–30 psi. The spring range and maximum
allowable supply pressure are marked on the serial
plate. For a 3–15 psi nominal range, the stem will start
to stroke when the air pressure reaches 3 psi, and will
complete the stroke when the pressure reaches 15 psi
(plus or minus 5%).
In the air-to-extend actuator, conformation of the
molded diaphragm to the diaphragm plate serves as
a flexible upper guide for the actuator stem (26). The
lower guide is an oil-impregnated bronze bushing (37)
located in the spring adjustor (36). The air-to-retract
actuator differs from the air-to-extend unit in that the
spring (22), spring barrel (71) and spring adjustor (36) are
located above the diaphragm plate (40) and diaphragm
(39) which are inverted. A gasket (19) at the joint of the
diaphragm case and yoke and a packing box around
the actuator stem prevents air leakage. The diaphragm
acts as a flexible upper guide and the packing box
assembly as the lower guide for the actuator stem.
Air connections are 1/4" NPT. Connections are located in
the upper diaphragm case (air-to-extend actuators) or
yoke (air-to-retract actuators).
Standard
Actuator Size
Effective
Diaphragm
Area (sq. in.)
Maximum
Stroke (in.)
9
45
¾
11
71
1
13
105
1
½
15
145
2
18
200
2
½
18L
200
4
Maintenance
Air-to-Extend Actuators (Type 37)
Diaphragm Replacement. Before disassembling the
actuator, all spring compression should be relieved
by turning the spring adjustor (36), to prevent the
upper case popping up when the cap screws (45) are
removed. This is especially important on actuators
with a high initial spring setting. Remove cap screws
(45), nuts (46) and upper diaphragm case (43). Remove
nut (30) and washer (41) to release the diaphragm (39).
If possible, the replacement diaphragm should be of
the molded type supplied by Masoneilan, but in an
emergency a diaphragm may be cut from flat sheet
stock for up to and including No. 15 actuators. To allow
sufficient stroke without restriction due to flatness of
the diaphragm, the diaphragm bolt circle should be
about 10% greater than that of the diaphragm case.
Replace washer (41), nut (30) and upper diaphragm
case.
Spring Adjustment. An air supply, with a gauge and
regulator, should be piped to the upper diaphragm
case for this adjustment. Adjust spring compression so
that the actuator sem (26) just begins to move when
air pressure reaches minimum pressure of the range
stamped on the serial plate. This movement is most
easily detected by feeling the stem as air pressure is
applied.
Note: Adjust spring compression only when
there is no air pressure on diaphragm.
Air-to-Retract Actuators (Type 38)
Diaphragm Replacement. The procedure is the same
as for air-to-extend actuators except that the entire
upper case assembly (including spring barrel (71), spring
(22), spring seats (33 and 34), nut (30) and diaphragm
plate (40) must be removed to release the diaphragm.
Install a new diaphragm and reassembly the above
parts.
Spring Adjustment. The procedure is identical with that
for air-to-extend actuators except that supply air is
piped to the 1/4" port in the yoke.
Packing Box. The packing box is subject to low air
pressure only and requires minimum maintenance.
The packing rings have a square section and are made
of carbon core with braided PTFE jacket. The packing
may be added to or completely replaced without
disassembling either the actuator or the mechanism (or
valve) to which it is attached. Be sure to tighten packing
nut (20) lightly. Over-tightening will cause excessive
friction, resulting in sluggish performance.