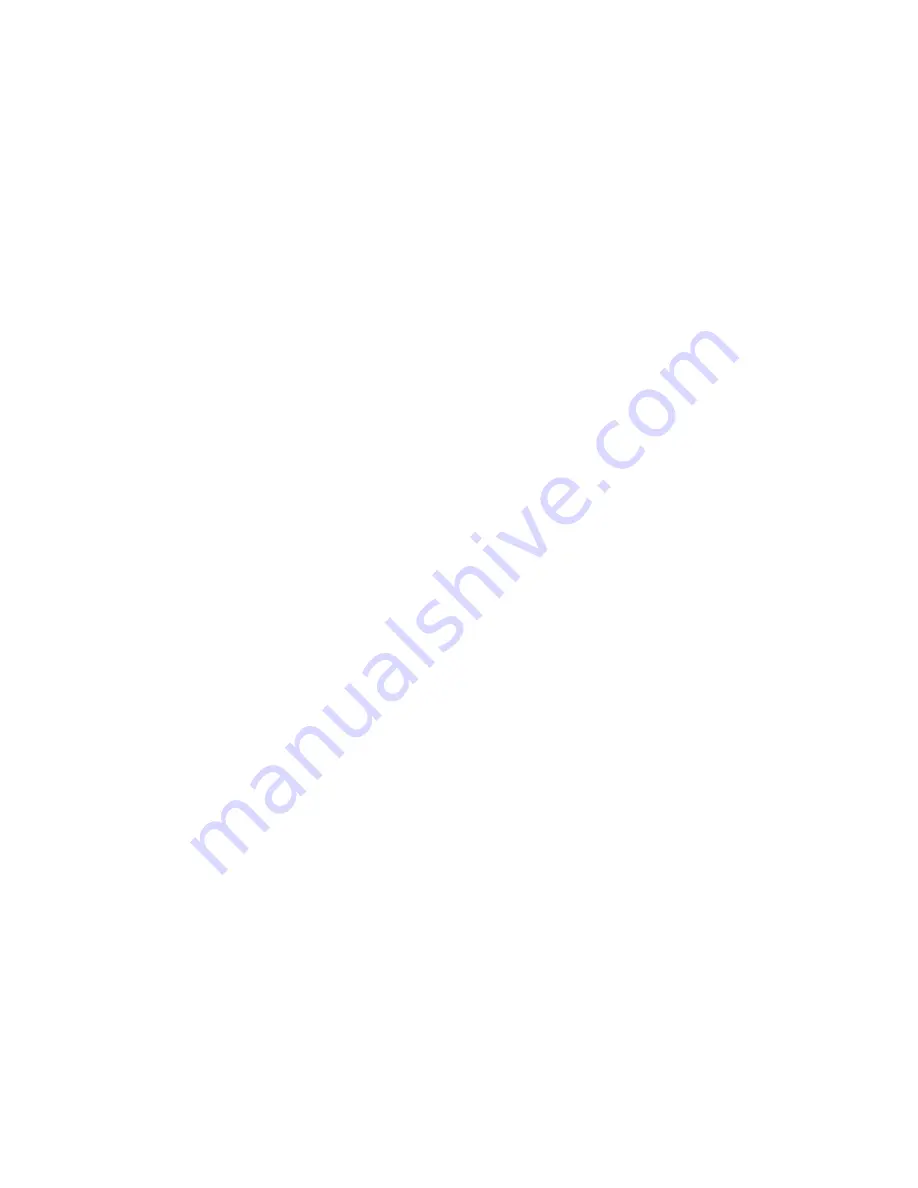
6–4
350 FEEDER PROTECTION SYSTEM – INSTRUCTION MANUAL
SETPOINTS MAIN MENU
CHAPTER 6: SETPOINTS
If
<ELEMENT_NAME> FUNCTION
: “Control” the feature is operational. When an output
is generated, the feature operates any selected output relays. The “Trip”, “Alarm”, and
“Control” function setpoint values are also used to select those operations that will be
stored in the Event Recorder.
•
OUTPUT RELAY setpoint
: The
<ELEMENT_NAME> OUTPUT RELAYS
setpoint selects the
relays required to operate when the feature generates an output. The range is
“Operate” or “Do Not Operate”, and can be applied to any combination of the auxiliary
output relays. The default setting is “Do Not Operate”.
The available auxiliary relays are output relays 3 to 6.
•
PICKUP setpoint
: The
<ELEMENT_NAME> PICKUP
setpoint selects the threshold above
which the measured parameter causes an output from the measuring element.
•
BLOCK setpoint
: The
<ELEMENT_NAME> BLOCK
setpoint applies the selected input to
block the function. More than one BLOCK setpoint may be available for a given
element; a single high input always blocks the function..
The range depends on order code, and can include Contact Input 1 to 10, Virtual Input
1 to 32, Remote Input 1 to 32, Logic Elements 1 to 16, 2nd Harmonic Alarm, 2nd
Harmonic, CT Fail Alarm PKP, and CT Fail Alarm OP. The default setting is “Off”.
•
DELAY setpoint
: The
<ELEMENT_NAME> DELAY
setpoint selects a fixed time interval to
delay an input signal from appearing at the output. The time from a contact input
change of state or an AC parameter input level change to a contact closure of the 1
Trip relay, is the time selected as time delay in this setpoint plus approximately up to 2
power frequency periods.
•
DIRECTION setpoint
: The
<ELEMENT_NAME> DIRECTION
setpoint is available for
overcurrent features which are subject to control from a directional element. The
range is “Disabled”, “Forward”, and “Reverse”. If set to “Disabled”, the element is
allowed to operate for current flow in any direction. There is no supervision from the
directional element. If set to “Forward”, the element is allowed to operate for current
flow in the forward direction only, as determined by the directional element. If set to
“Reverse”, the element is allowed to operate for current flow in the reverse direction
only, as determined by the directional element.
Logic diagrams
The logic diagrams provide a complete comprehensive understanding of the operation of
each feature. These sequential logic diagrams illustrate how each setpoint, input
parameter, and internal logic is used in the feature to obtain an output. In addition to these
logic diagrams, written descriptions are provided in the setpoints chapter which includes
each feature.
•
Setpoints
: Shown as a block with a heading labeled ‘
SETPOINT
’. The exact wording of
the displayed setpoint message identifies the setpoint. Major functional setpoint
selections are listed below the name and are incorporated in the logic.
•
Compensator Blocks
: Shown as a block with an inset box labeled ‘
RUN
’ with the
associated pickup/dropout setpoint shown directly above. Element operation of the
detector is controlled by the signal entering the ‘RUN’ inset. The measurement/
comparison can only be performed if a logic ‘1’ is provided at the ‘
RUN
’ input. The
relationship between setpoint and input parameter is indicated by the following
symbols: “
<
” (less than) "
>
” (greater than), etc.
•
Time Delays
: Shown as a block with either pickup, drop-out, or both; times in
milliseconds or seconds. If the delay is adjustable, associated delay setpoint is shown
with block
SETPOINT
on the top of the delay block.
•
LED Indicators
: Shown as the following schematic symbol,
□
. The exact wording of
the front panel label identifies the indicator.