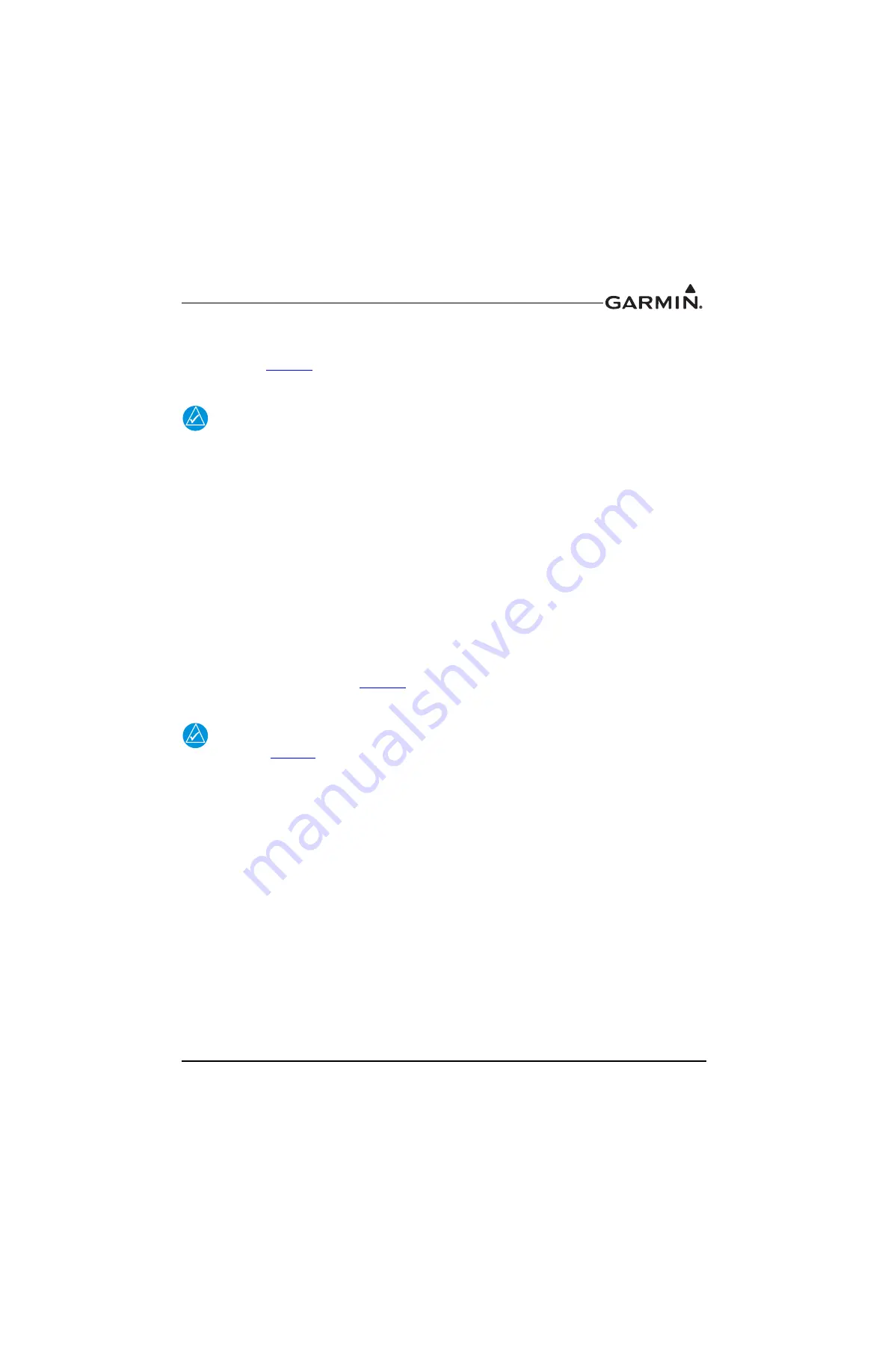
190-01639-00
GSU 75 ADAHRS Installation Manual
Rev. 6
Page 5-14
5.9 Site Evaluation of Magnetic Disturbances for Magnetometer Calibration
Procedure
As mentioned in
, the Magnetometer Calibration Procedure (Calibration Procedure B) must be
carried out at a site that is determined to be free of magnetic disturbances.
NOTE
Typically, a compass rose is an acceptable location to perform the magnetometer
calibration procedure. However, because not all compass roses are well maintained, even
an existing compass rose should be regularly evaluated using the method described here
to determine if it is free of magnetic disturbances. If evaluation of an existing compass
rose indicates that magnetic disturbances are present, then an alternative location must be
found to perform the Magnetometer Calibration Procedure.
A Garmin Integrated Flight Deck-equipped airplane can be used to evaluate a candidate site for magnetic
disturbances and determine whether it is a suitable location to perform the magnetometer calibration
procedure. The magnetometer calibration procedure itself contains the logic to simultaneously survey the
location for magnetic cleanliness while it is computing the magnetometer calibration parameters.
The Garmin Integrated Flight Deck-equipped airplane installation used to evaluate the site must have
already completed the pitch/roll offset compensation procedure (Procedure A-1). However, prior
completion of the Magnetometer Calibration Procedure (Procedure B) is not required.
In order to evaluate a candidate site, the Magnetometer Calibration Procedure must be performed twice:
once turning clockwise around the site, and once turning counter-clockwise. Both times, the procedure
should be conducted as described in
of this document, with the exception of the direction of turns
around the site.
NOTE
Although
indicates that the Magnetometer Calibration Procedure should be
performed by making a series of clockwise turns around the site, the procedure can also be
performed by making counter-clockwise turns for the purpose of evaluating the site for
magnetic disturbances.
If, upon completion of the Magnetometer Calibration Procedure in both the clockwise and counter-
clockwise directions, the PFD displays the “CALIBRATION SUCCESSFUL / SITE IS CLEAN” message,
then the candidate site is sufficiently free of magnetic disturbances and is acceptable for performing the
Magnetometer Calibration Procedure. It is important to perform the procedure in both the clockwise and
counter-clockwise directions to ensure that the magnetometer sweeps over a large enough area at the
candidate site.
340095
The document reference is online, please check the correspondence between the online documentation and the printed version.