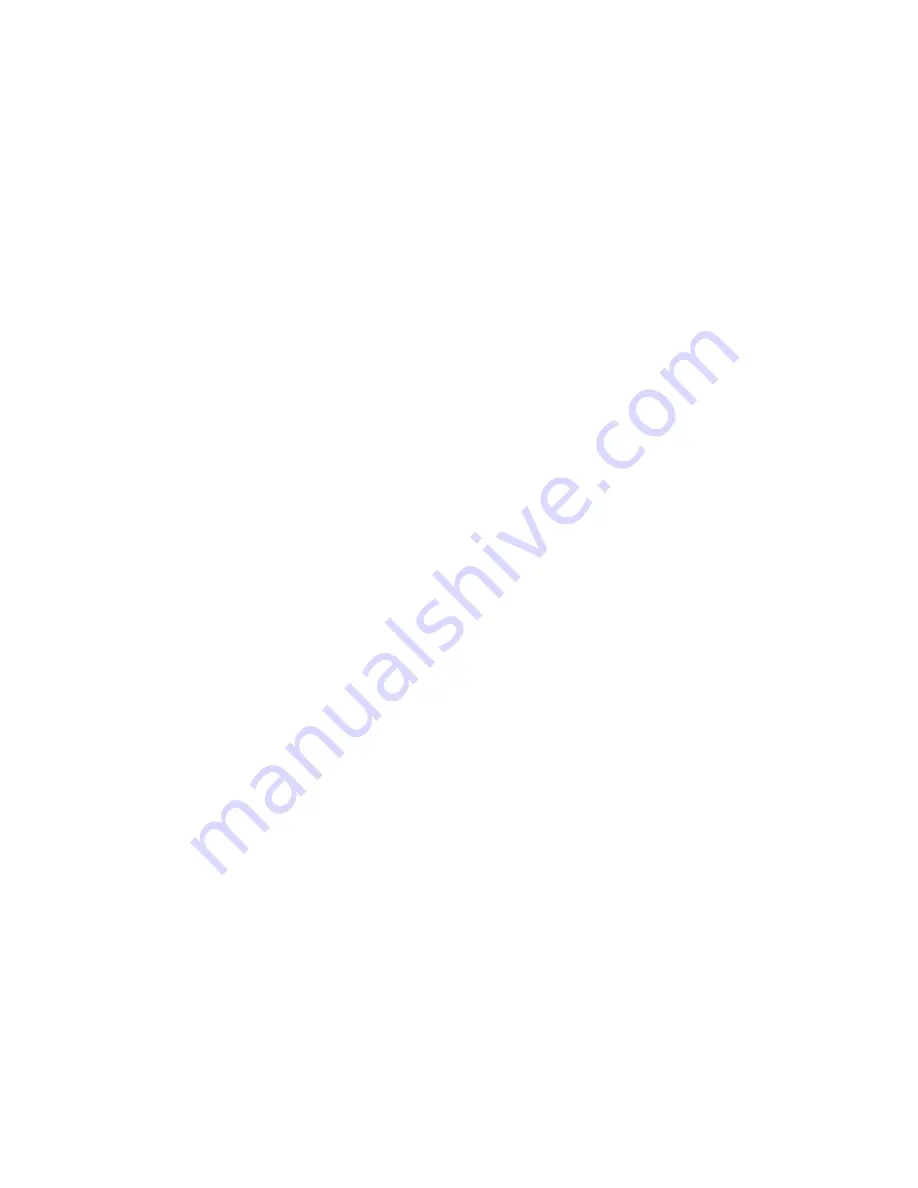
15
the PLC and shows as “1” on the PLC input display.
The PLC will perform a purge time sequence, during
which the booth will remain in the spray mode
temperature. At the end of the purge cycle the PLC
will begin timing the Bake Cycle and energize the
Changeover damper solenoid in the main control
panel. This places the booth in Bake Mode.
When the Changeover damper solenoid is energized,
the Changeover damper is pneumatically opened,
releasing the Damper Position Valve. When the
Damper Position Valve is released, the pressure
switch (RA), connected to the Damper Position
Valve, de-energizes and input is given to the PLC,
shown as “11” on the PLC input display. This
disconnects 110v power to the compressed air
solenoid, shown as “5” on the PLC output display,
and eliminates the 120v circuit to RL contactor,
turning off the booth lighting. If the burner switch is
in the SUMMER position, the PLC will give 120v to
the Gas Train Power Circuit, shown as “7” on the
PLC output display. In WINTER position the Gas
Train Power Circuit will already have 120v power.
The controls then initiate the ramp up time and
temperature. This begins the sequence of multiple
time and temperature settings.
At the completion of the bake time, the PLC stops
the bake time sequence and begins the Cool Down
time sequence (Shutdown mode).
SHUTDOWN MODE:
The power to the Changeover damper solenoid and
RP relay is interrupted. The Changeover damper
closes, RA is energized, the booth lights come back
on, and the booth temperature returns to the Spray
Temperature. The output from the PLC will be de-
energized, shutting off the burner if the Burner
switch on the touch screen display is set to
SUMMER position. If the Burner switch is set to
WINTER position, the burner circuit will remain
energized.
The PLC also begins and internal time cycle,
normally 10 minutes. All functions of the booth will
shut down completely at the end of the time
cycle. After the time cycle is complete, the
logic of the PLC will not allow the booth to
restart until the OFF-SPRAY-BAKE switch,
displayed on the touch screen, is set to the OFF
position. The Operator may interrupt the
Shutdown Mode at any time before the time
cycle is complete, by placing the OFF-
SPRAY-BAKE switch in the SPRAY
position.
GAS TRAIN POWER CIRCUIT:
When the BURNER switch (on the touch
screen display) is set to the WINTER position
there will be input to terminal 4 of the PLC and
will show number “3” on the input display of
the PLC. The PLC checks to make sure that
the input is at “0” on the input display and
outputs to “7” on the output display, giving
power to the low gas pressure switch. The PLC
then makes a scan of the input to “4,5, 6 & 7”,
on the input screen, and then gives output to
“11” on the output display, giving power to the
Fireye unit and power to “1” on the output
display giving power to the burner green light.
The PLC will have input at “8” on the input
display, showing power to the airflow switch.
When the Fireye has done its’ job there should
be power to “9” on the input screen, showing
that power has been given to the vent and
blocking valves on the gas train. The PLC will
also make the signal connection “0” on the
output display, making the connection between
the gas modulating valve and the temperature
controls. In the event the Fireye goes into the
alarm state, there will be input to “10” on the
input display and no input to “9” on the PLC
input display. There will also be output to “2”
on the output display, giving power to the
burner red light, and discontinuing the power
to the burner green light, output to “1” on the
display,.
The Low Gas and High Gas Limit, the Proof
of Closure switch (all three are located on the