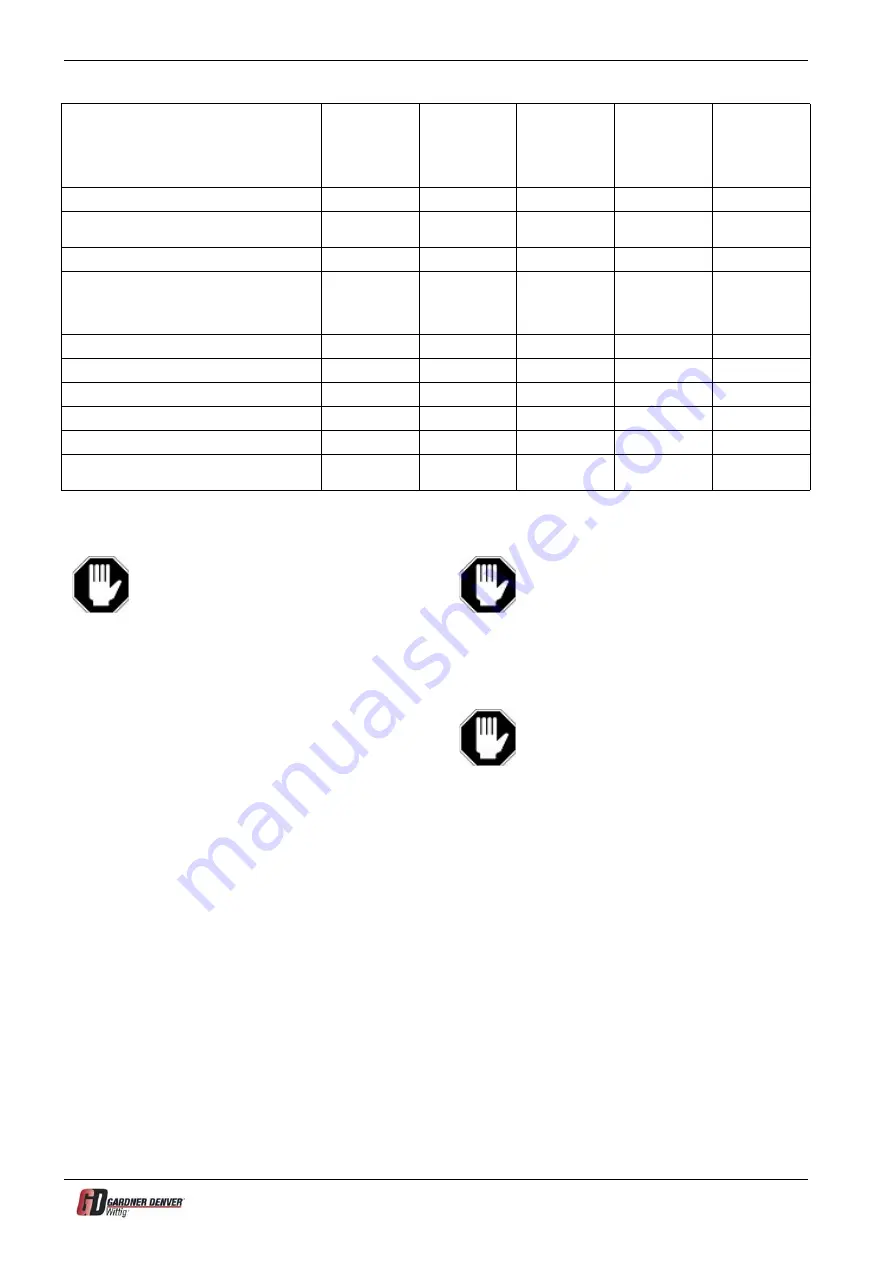
14 T-BA/ET-1250-0-GB-
10
-
11
6.0 Operation
Monitoring periods
6.3 Possible operating errors
Operating errors can cause machine
failure.
To be avoided at all costs:
•
Excessively low or high speeds
•
Excessive pressure
•
With the pressure pipe closed, blow off the total
volumetric flow through the safety valve
•
Vacuum too low
•
Compressed air temperature too high (see 6.2)
•
Poor cooling (affecting supply of cooling air)
•
Blocked vacuum filter
•
Block exhaust silencer
•
Intake of fluid
•
Water hammer due to failure to drain away con-
densate in time from the safety tanks (risk of freez-
ing in winter)
•
Lack of lube oil
•
Wrong lube oil
•
Do not open tank when vacuum is applied
•
Empty only with pump at a standstill
In the event of damage due to operating
errors, no warranty claim can be submit-
ted to Gardner Denver.
6.4 Action for prolonged standstill
•
Clean the machine thoroughly.
When cleaning with a pressure washer,
there is a risk of water penetration.
•
After wet cleaning, run machine for several minu-
tes until warm so as to prevent the rotary slide
valve from sticking.
Where the rotary compressor/compressor vacuum
pump fitted in the vehicle is to remain unused for more
than one month, we recommend operating the
machine once each month for at least 15 minutes.
This will ensure a fresh supply of oil to all components
that are endangered by corrosion.
see chapter
During
operation
every 10 -
20 minutes
after every
use
daily
weekly
Operating speed
6.2
•
Operating pressure, respectively vacuum
Identification
plate
•
Air outlet temperature
6.2
•
Drain off condensate (
contains oil!
)
Silencer oil trap
Safety tank
6.2
•
•
Oil level
6.2
•
Actuate safety valve
6.2.1
•
Actuate vent valve
6.2.1
•
Clean the machine
•
Clean air intake and outlet openings
•
Check fastening of the fan cowl and cover
panels
•