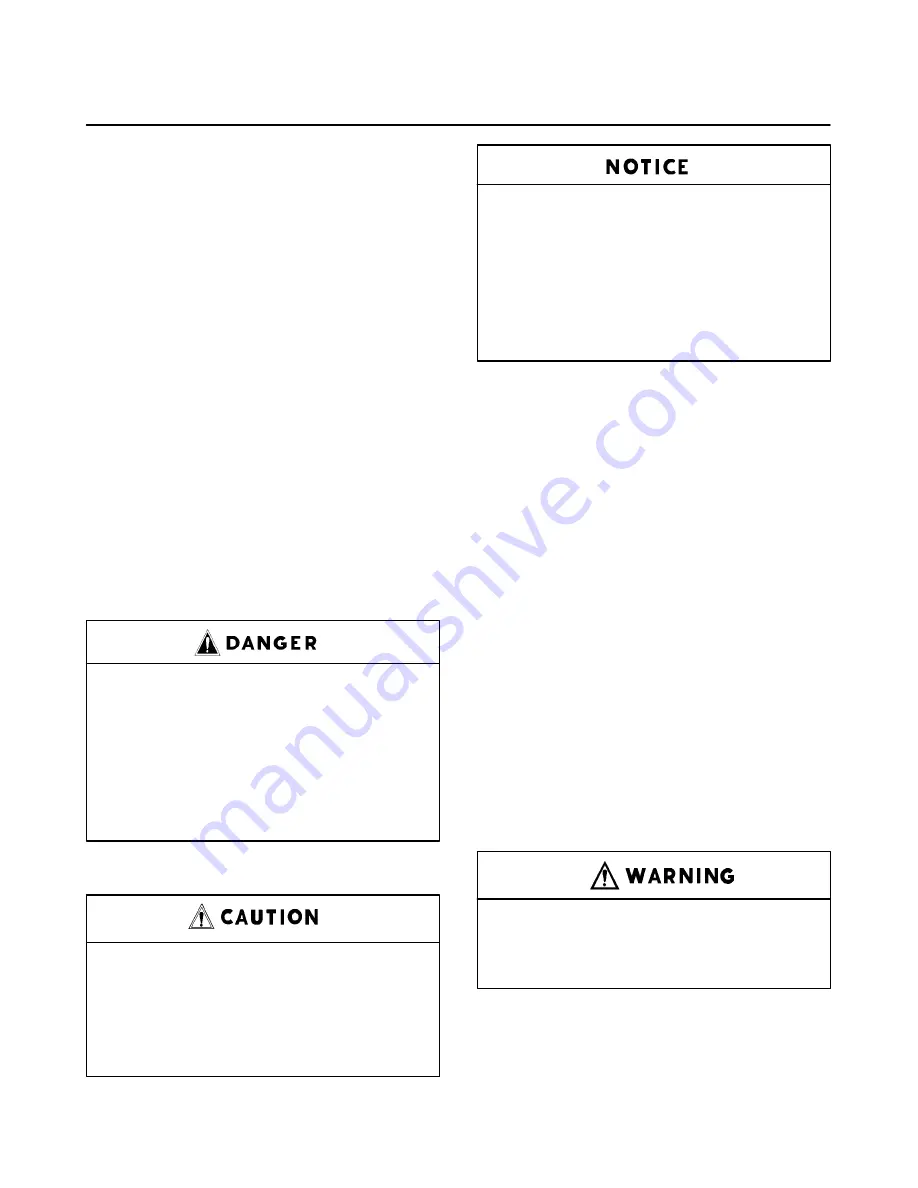
13–11–602 Page 19
SECTION 3
STARTING & OPERATING PROCEDURES
PRESTART–UP INSTRUCTIONS – A new unit as re-
ceived from the factory has been tested and then pre-
pared for shipping. Do not attempt to operate the unit
until checked and serviced as follows:
1.
Compressor Oil – Check reservoir oil level. Oil
must be within the operating range.
REPLACE OIL FILTER EVERY 8000 HOURS.
Initial fill, or filling after a complete draining of the
system, may show the oil level in the yellow “EX-
CESS OIL” range. After start–up, the oil will fall
into the green operating range as system compo-
nents are filled. If necessary, add oil to bring the
level to the top of the green range as read when
the unit is operating at full load and normal pres-
sure. See FIGURE 5–1, page 42.
Oil level must be within the operating range. Add
or drain oil to correct level using the same type of
oil. Check to ensure the vent is installed in the top
of the oil reservoir and is open to allow free pas-
sage of air.
Air and water under pressure will
cause severe personal injury or
death. Shut down compressor, relieve
system of all pressure, disconnect,
tag and lockout power supply to the
starter before removing valves, caps,
plugs, fittings, bolts, and filters.
Use of improper lubricants will cause
damage to equipment. Do not mix dif-
ferent types of lubricants or use infe-
rior lubricants. See Section 5, page
41, for lubrication recommendations.
Regular maintenance and replace-
ment at required intervals of the oil fil-
ter, air filter and water filter is neces-
sary to achieve maximum service of
this screw compressor. Use only gen-
uine Gardner Denver filters designed
and specified for this compressor.
After shutdown, the system will partially drain
back into the oil reservoir and the oil level may
read higher than when operating on load. DO
NOT DRAIN OIL TO CORRECT; on the next
loaded cycle or start, oil will again fill the system
and the gauge will indicate the operating level.
2.
Air Filter – Inspect the air filter to be sure it is clean
and tightly assembled. Refer to Section 6, “Air Fil-
ter,” page 45, for complete servicing instructions.
Be sure the inlet line, if used, is tight and clean.
3.
Coupling – Check all bolts and cap screws for
tightness. See Section 7, page 47.
4.
Piping – Refer to Section 2, “Installation,” page
9, and make sure piping meets all recommenda-
tions.
5.
Electrical – Check the wiring diagrams furnished
with the unit to be sure it is properly wired. See
FIGURE 4–10 and FIGURE 4–11, pages 38 and
39, for general wiring diagrams and Section 2,
page 9 for installation instructions.
6.
Grounding – Equipment must be properly
grounded according to Table 250–95 of the Na-
tional Electrical Code.
Failure to properly ground the com-
pressor package could result in con-
troller malfunction.
7.
Rotation – Check for correct motor rotation using
“JOG MODE.” An arrow on the compressor/motor
adaptor shows correct rotation. Rotation must be
clockwise standing facing compressor coupling.
Содержание TWISTAIR EWDQ D
Страница 14: ...13 11 602 Page 4 FIGURE 1 6 AIR WATER SCHEMATIC FIGURE 1 7 OIL SCHEMATIC...
Страница 17: ...13 11 602 Page 7 DECALS 206EAQ077 212EAQ077 218EAQ077 211EAQ077 207EAQ077...
Страница 18: ...13 11 602 Page 8 DECALS 216EAQ077 206EWD077 222EAQ077 221EAQ077 208EAQ077...
Страница 35: ...13 11 602 Page 25 FIGURE 4 2 FLOW CHART FOR SET UP PROGRAMMING...
Страница 44: ...13 11 602 Page 34 FIGURE 4 6 CONTROL TUBING SCHEMATIC 206EWD797 A Ref Drawing...
Страница 46: ...13 11 602 Page 36 FIGURE 4 8 CONTROL SCHEMATIC COMPRESSOR UNLOADED CONSTANT SPEED MODE 208EWD797 A Ref Drawing...
Страница 47: ...13 11 602 Page 37 FIGURE 4 9 CONTROL SCHEMATIC COMPRESSOR UNLOADED LOW DEMAND MODE 209EWD797 A Ref Drawing...
Страница 48: ...13 11 602 Page 38 FIGURE 4 10 WIRING DIAGRAM FULL VOLTAGE 202EWD546 REF DRAWING...
Страница 49: ...13 11 602 Page 39 FIGURE 4 11 WIRING DIAGRAM WYE DELTA 203EWD546 REF DRAWING...
Страница 50: ...13 11 602 Page 40 FIGURE 4 12 AUTO SENTRY ES CONTROLLER DISPLAY...
Страница 53: ...13 11 602 Page 43 FIGURE 5 2 FLOW DIAGRAM AIR COOLED 202EWD797 B Ref Drawing...
Страница 54: ...13 11 602 Page 44 FIGURE 5 3 FLOW DIAGRAM WATER COOLED 203EWD797 A Ref Drawing...
Страница 68: ......