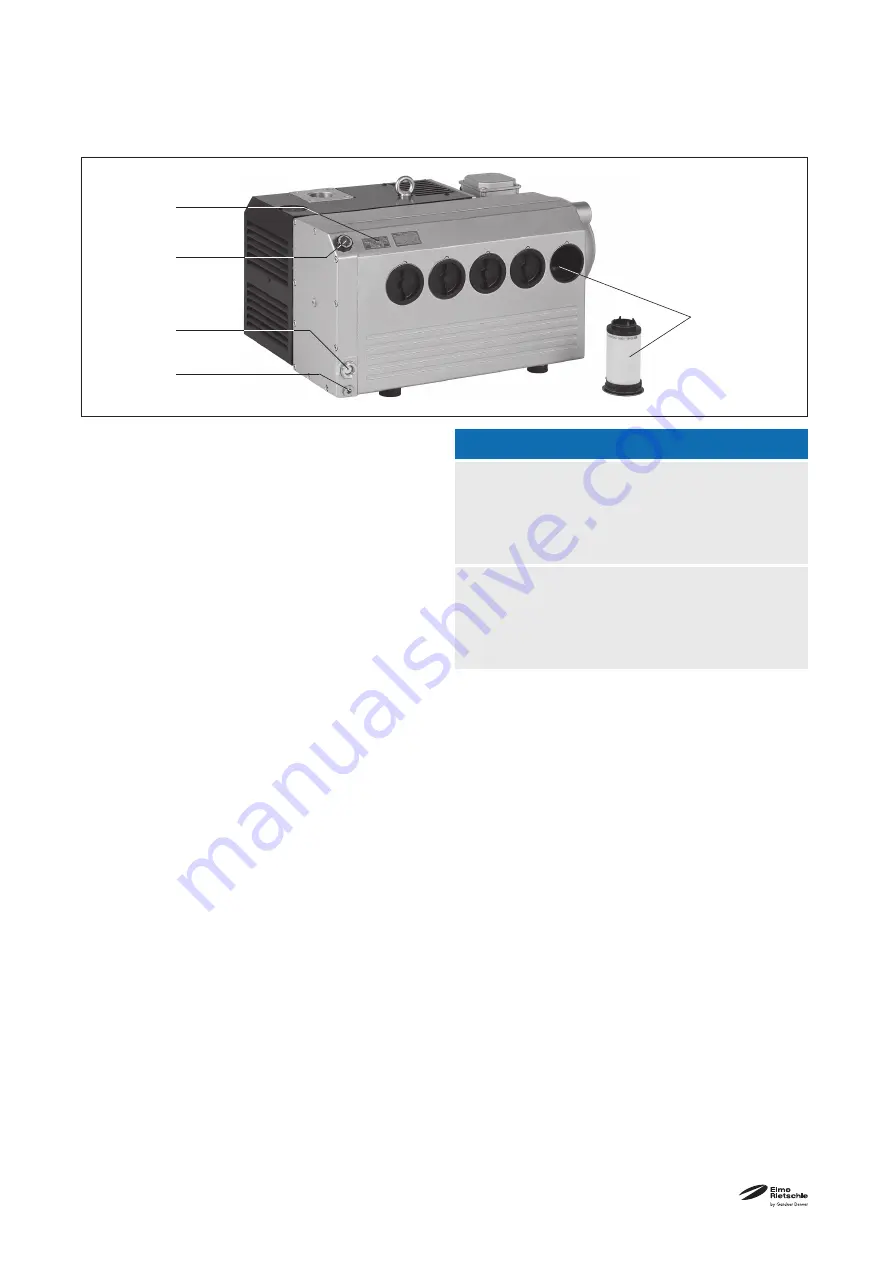
22
|
www.gd-elmorietschle.com
© Gardner Denver Schopfheim GmbH, Gardner Denver Deutschland GmbH
Maintenance and repair
H
M
L
I
K
7.2.3 Lubrication
NOTICE
Always change the oil when the machine is at
operating temperature and in an atmospherically
ventilated area. If it is not completely emptied the
amount that can be refilled is reduced.
he waste oil must be disposed of in compliance with
the local environmental protection regulations.
If you change the type of oil, empty the oil tank
completely.
The oil level must be checked at least once a day,
if necessary top the oil up to the upper edge of the
sight glass (Fig. 7/I) First oil change after 500 hours
of operation. Subsequent oil changes after 500-
2000 hours of operation. Reduce the change inter-
vals accordingly depending on how contaminated
the discharged medium is.
Only vacuum pump oils as per DIN 51506-VDL, ISO
6743-3 DVA and DVC or a synthetic oil released by
Elmo Rietschle may be used. The viscosity of the
oil must comply with ISO VG 100 as per DIN 51519.
Elmo Rietschle oil types:
MULTI-LUBE 100 (mineral
oil) and SUPER-LUBE 100 (synthetic oil) see also oil
recommendation plate (Fig. 7/M)).
If the oil is subject to high temperatures (ambient or
intake temperatures over 30 °C, insufficient cooling,
60 Hz operation etc.) the oil change interval may be
extended by using the recommended synthetic oil.
Fig. 7 Lubrication and removing oil
H
Oil filling point
I
Oil sight glass
K
Oil discharge point
L
Oil separator element
M
Oil recommendation plate