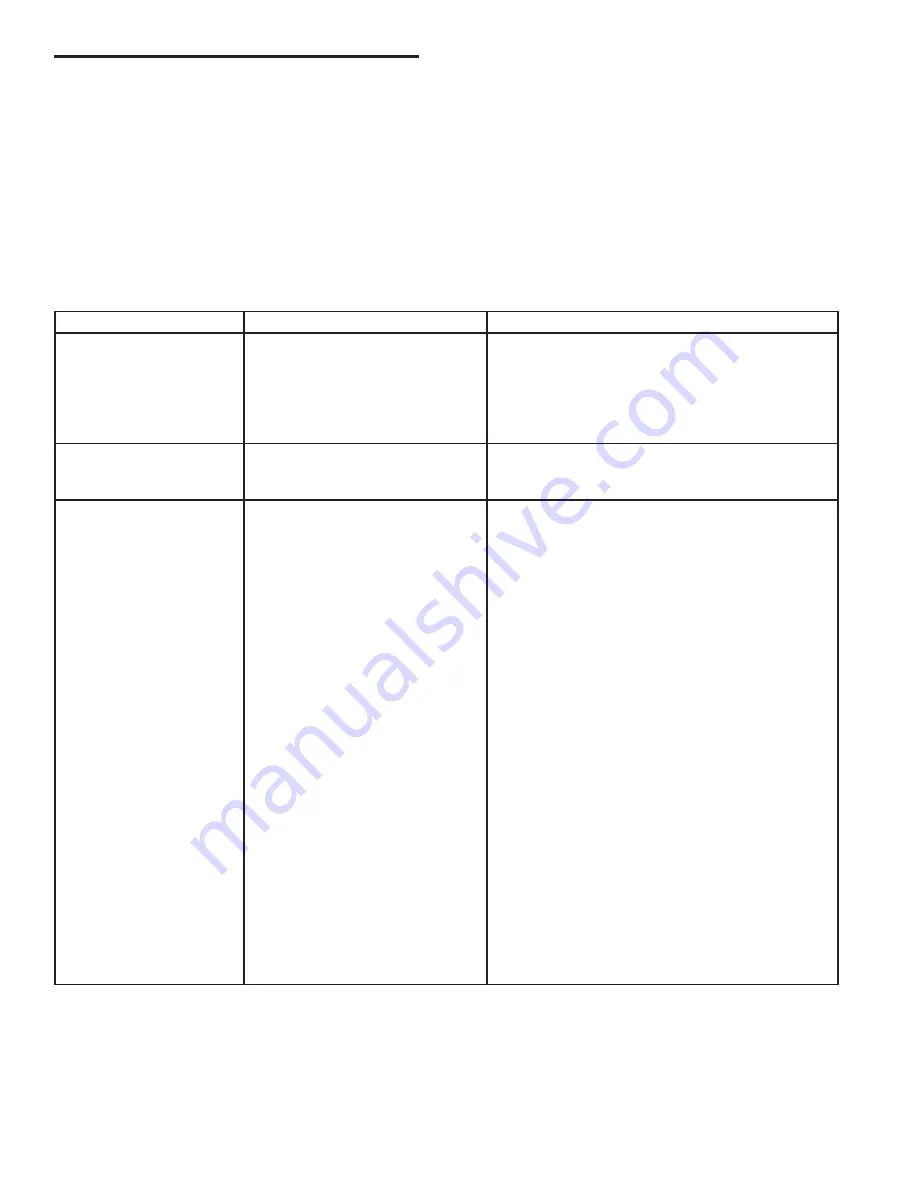
30
8.0 Troubleshooting
WARNING - A POTENTIAL ELECTRICAL SHOCK
HAZARD EXISTS. Some of the troubleshooting
checks may require gaining access to the dryer’s
electrical enclosure(s) while the power supply is
energized and should be performed by a qualified
electrical technician.
WARNING - Before performing any electrical or
mechanical repairs or maintenance, or removing
or disassembling any component, be sure to de-
energize and depressurize the dryer.
SYMPTOM
POSSIBLE CAUSE(S)
CORRECTIVE ACTION
Indicator lights not illuminated
1. No power to unit.
2. Loss of power supply to (or at) dryer’s
electrical disconnect switch or breaker.
(customer supplied)
3. Blown fuse.
4. Board malfunction.
1. Check voltage at terminal board.
2. Check disconnect switch or breaker closed. If tripped
breaker or blown fuse is noted, investigate and Remedy
cause.
3. Replace fuse.
4. Replace board.
Excessive pressure drop in dryer 1. Inlet/Outlet screens on desiccant
towers are dirty
2. Excessive flow rate
1. Clean screens; follow desiccant removal instructions in the
Maintenance section.
2. Check flow rate of inlet air. Reduce to design flow rate.
Low Pressure Alarm
Left Tower or Right Tower
Drying
1. Loss of dryer air supply.
2. Excessive air demand.
3. Faulty drying tower pressure switch
4. Drying tower Inlet Valve failed to open
5. Drying tower Purge Exhaust Valve
failed to close.
6. Drying tower Depressurization Valve
failed to close
7. Regenerating tower Outlet Check
Valve failed to close
1. Check compressor supplying dryer.
2. Check equipment downstream of dryer.
3. Check pressure switch operation using tower pressure
gauge for comparison. Replace switch if defective.
4a. Check for loss of pilot air - ensure manual drain valve on
bottom of pilot air filter is fully closed, ensure pilot air filter
cartridge is not clogged, ensure pilot air shut-off valve is
open
4b. Check for inlet pilot air solenoid valve failure. Check valve
operation. Repair or replace as necessary.
4c. Check for drying tower Inlet Valve failure - examine valve
and actuator for damage. Repair or replace as necessary.
5a. Check for air flow out of drying tower Purge Valve or
exhaust piping indicating valve is not completely closed.
5b. Check for loss of pilot air - ensure manual drain valve on
bottom of pilot air filter is fully closed, ensure pilot air filter
cartridge is not clogged, ensure pilot air shut-off valve is
open
5c. Check for purge pilot air solenoid valve failure. Check valve
operation. Repair or replace as necessary.
5d. Check for drying tower Purge Exhaust Valve failure -
examine valve and actuator for damage. Repair or replace
as necessary.
6. Check for air flow out of drying tower Depressurization
Muffler indicating valve is not completely closed. Repair or
replace as necessary.
7. Indicated by excessive flow out of regenerating tower
Purge Valve. Examine valve internals. Repair or replace
as necessary.