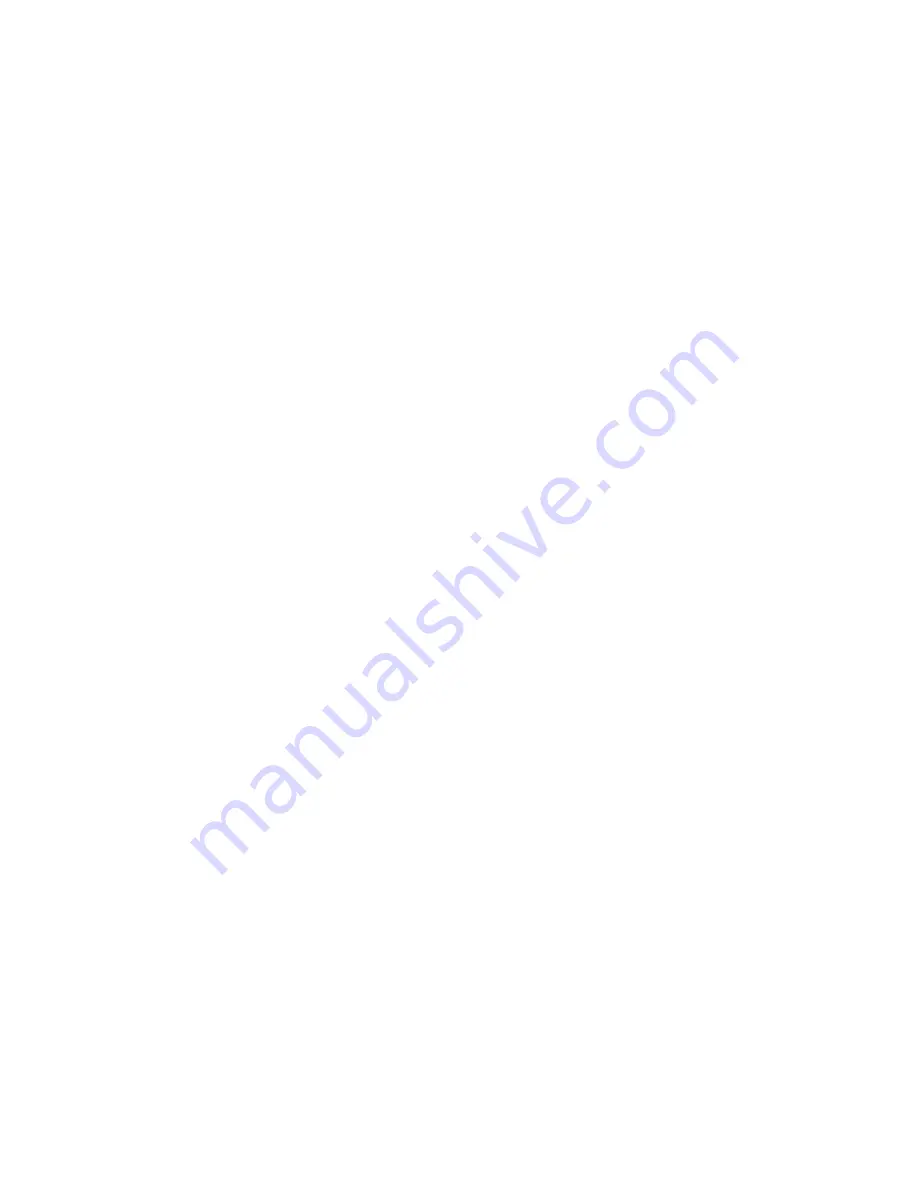
25
Two mainline outlet and two smaller purge line check
valves are installed in the upper piping to control the flow
of outlet and purge air. Check valve sticking will result in
excessive air discharge through a muffler. Excessive air
discharge through the muffler can be associated with a
leaking outlet check valve on the same side or a purge
check valve of the opposite side tower.
Dryers are equipped with a single safety relief valve that
has been sized to provide overpressure protection due
to a fire for both desiccant towers.
The tower pressure gauge of the online tower should
read line pressure. Air should not be leaking from the
purge-repressurization valve of the on-line tower.
The tower pressure gauge of the off-line tower should
read below 2 psig (0.14 kgf/ cm
2
) while that tower is
purging. If excessive air is exhausting during the purge
cycle, the inlet-switching valve on the same side may
have failed to close or a check valve may be sticking.
6.8 Dryer Shut Down
1. If the dryer installation is equipped with dryer bypass
and inlet and outlet isolation valves, the bypass valve
should be opened and the inlet and outlet isolation
valves closed.
2. De-energize the dryer’s electrical supply.
3. SLOWLY open the tower blow down valves (refer
to Figure 3 for general location) to vent the dryer
internal pressure.
4. When all dryer pressure gauges indicate zero pres-
sure, close the tower blow down valves. Depres-
surization is complete.
6.9 Loss of Power
Control valves are designed so that upon loss of power
the air dryer is capable of drying air until the desiccant
exposed to the airflow is saturated.
6.9.1 Power Recovery:
6.9.1.1 On loss of electrical power –
All controller outputs turn off causing the dryer operating
valves will react as follows:
1. For models with poppet style inlet valves (models
300 - 600): both inlet valves will open. Both towers
will repressurize.
2. For models with butterfly inlet valves (models 750 -
3200): inlet valves will remain in position. Any minor
leakage through the inlet valve or check valve will
slowly repressurize the off-line tower.
3. Purge exhaust valves close.
4. Purge supply valve fails open,
5. Venturi suction valve fails closed
6. Depressurization solenoid valves (where used)
close.
7. The off-line tower repressurizes to line pressure.
6.9.1.2 On restoration of power –
1. If power is lost when the off-line tower is in either
the HEAT or COOL step, the off-line tower will have
repressurized (either partially or completely) and the
sequence:
a. Resumes at the DEPRESSURIZATION step to
let down the pressure in the off-line tower then,
b. Advances directly to the beginning of whichever
stage of HEAT or COOL it had been at when
power was interrupted.
2. If the off-line tower was at any other step
( S W I T C H O V E R , D E P R E S S U R I Z AT I O N ,
REPRESSURIZATION or HOLD) when power was
lost, then the sequence simply resumes at that step.
6.9.1.3 Sequence Steps & Stages:
When power is restored the sequence doesn’t return
to the precise moment where power was lost, rather, it
resumes from the beginning of the last incomplete step
as described below:
1. “Hold” then Switchover: LT goes on-line, RT goes
off-line.
2. RT Depressurization
3. RT Heat Stage 1: 0 minutes
4.
Stage 2: 31.15 minutes
5.
Stage 3: 62.30 minutes
6.
Stage 4: 93.45 minutes
7.
Stage 5: 124.60 minutes
8. RT Cool Stage 1: 0 minutes
9.
Stage 2: 30 minutes
10. RT Repressurization
11. “Hold” then Switchover: RT goes on-line, LT goes
off-line.
12. LT Depressurization
13. LT Heat Stage 1: 0 minutes
14.
Stage 2: 31.15 minutes
15.
Stage 3: 62.30 minutes
16.
Stage 4: 93.45 minutes
17.
Stage 5: 124.60 minutes
18. LT Cool Stage 1: 0 minutes
19.
Stage 2: 30 minutes
20. LT Repressurization
The sequence then continues normally.