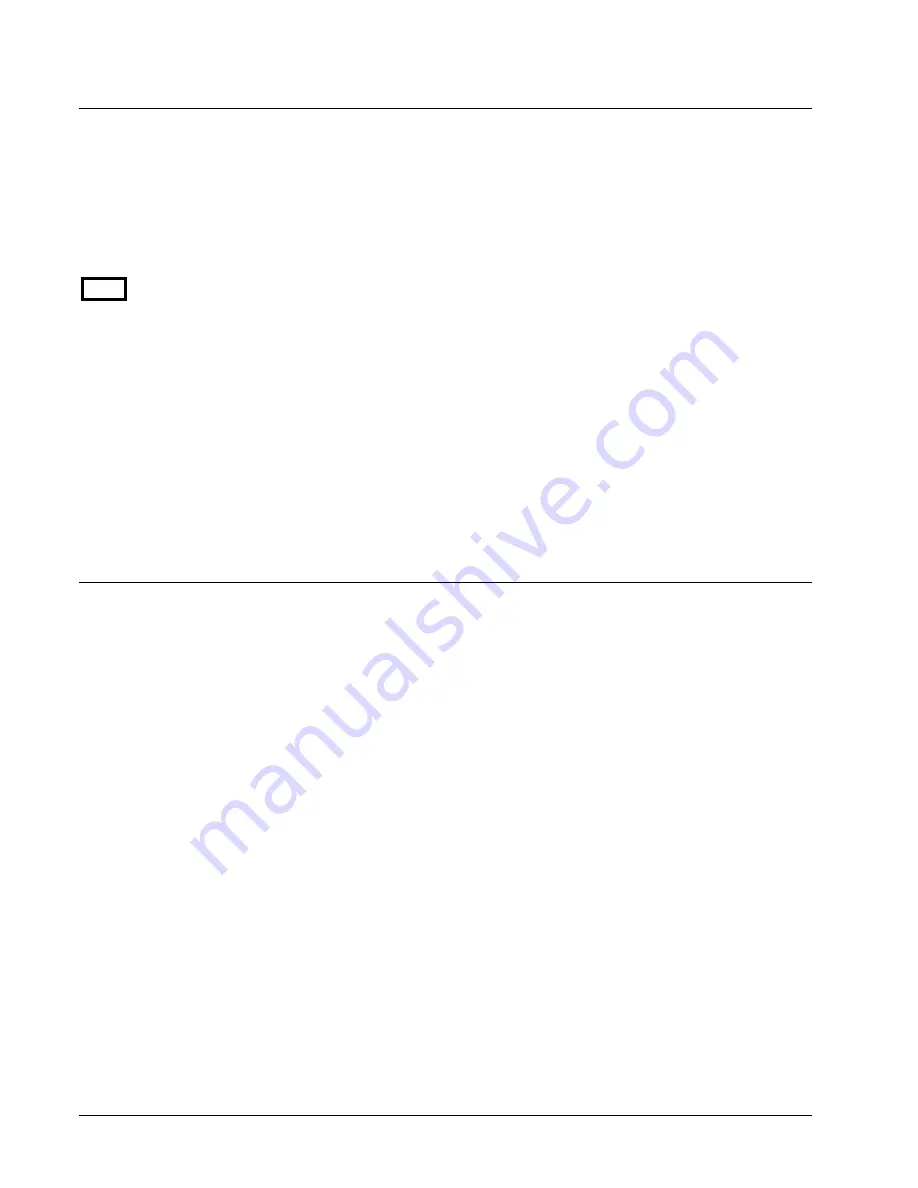
32
•
Chapter 3 Connecting Hardware
DMC-1000
TTL Outputs
The DMC-1000 provides eight general use outputs and an error signal output.
The general use outputs are TTL and are accessible by connections to OUT1 thru OUT8. These
outputs can be turned On and Off with the commands, SB (Set Bit), CB (Clear Bit), OB (Output Bit),
and OP (Output Port). For more information about these commands, see the Command Summary.
The value of the outputs can be checked with the operand _OP and the function @OUT[] (see Chapter
7, Mathematical Functions and Expressions).
1080
Controllers with 5 or more axes have an additional eight general use TTL outputs (connector JD5).
The error signal output is available on the main connector (J2, pin 3). This is a TTL signal which is
low when the controller has an error. This signal is not available through the phoenix connectors of
the ICM-1100.
Note: When the error signal is active, the LED on the controller will be on. An error condition
indicates one of the following conditions:
1.
At least one axis has a position error greater than the error limit. The error limit is set by using the
command ER.
2.
The reset line on the controller is held low or is being affected by noise.
3.
There is a failure on the controller and the processor is resetting itself.
4.
There is a failure with the output IC which drives the error signal.
Offset Adjustment
For each axis, the DMC-1000 provides offset correction potentiometers to compensate for any offset
in the analog output. These potentiometers have been adjusted at the factory to produce 0 Volts output
for a zero digital motor command. Before making any adjustment to the offset, send the motor off
command, MO, to the DMC-1000. This causes a zero digital motor command. Connect an
oscilloscope or voltmeter to the motor command pin. You should measure zero volts. If not, adjust
the offset potentiometer on the DMC-1000 until zero volts is observed.
Artisan Technology Group - Quality Instrumentation ... Guaranteed | (888) 88-SOURCE | www.artisantg.com