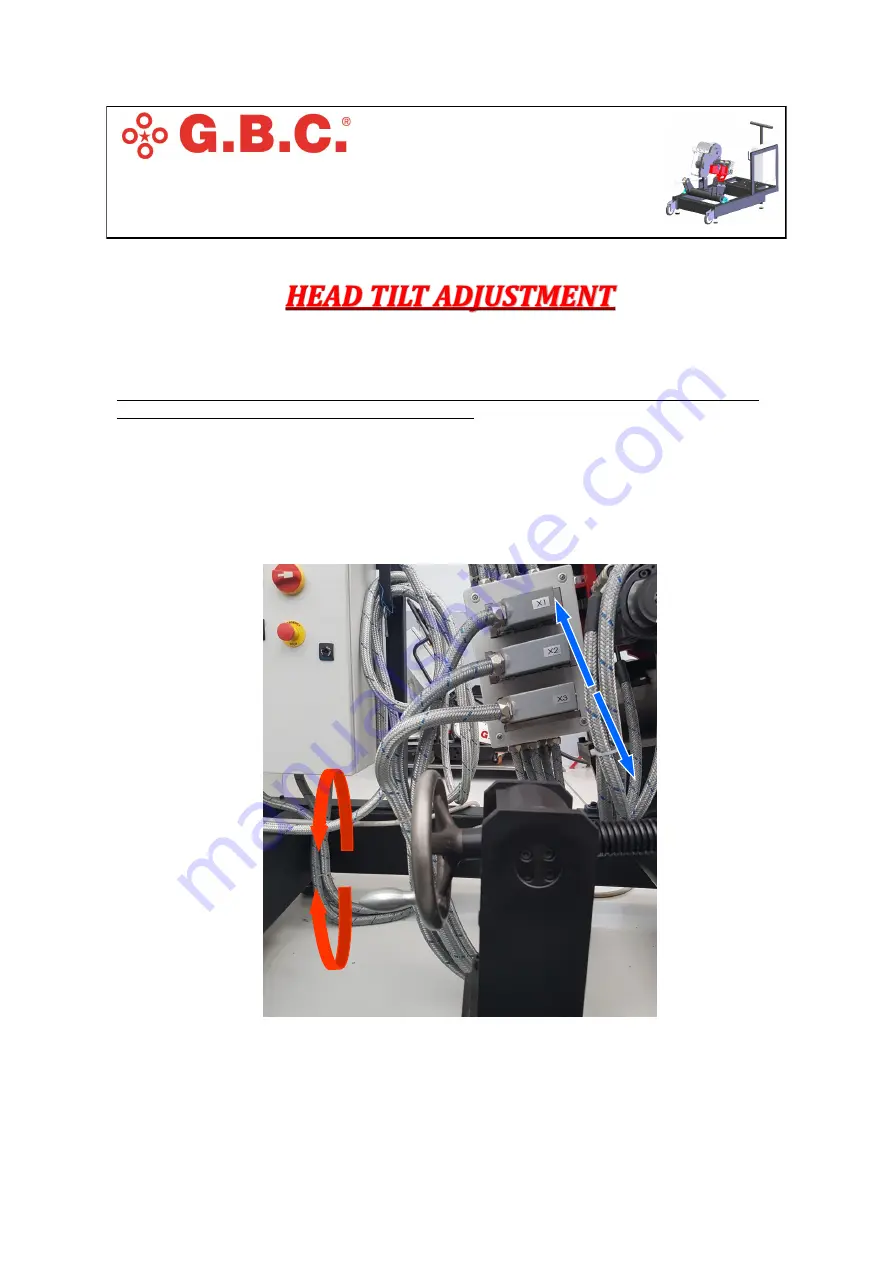
14
GRINDER G400
Original Instructions Rev.01
-
2017 in compliance with the § 1.7.4 of the Machines Directive 2006/42/CE
G.B.C. Industrial Tools S.p.A.
Via Sandro Pertini 41/43 –
25046
Cazzago San Martino (Bs) –
Italia –
Tel. + 39 030 7451154 –
email: [email protected]
The head tilt adjustment is achieved by rotating the handwheel in one way or another. This will
cause the head to tilt accordingly.
N.B. It is advisable that the head tilt does not exceed 10°÷45° and possibly that the head
axis is lined up with the workpiece to be worked.