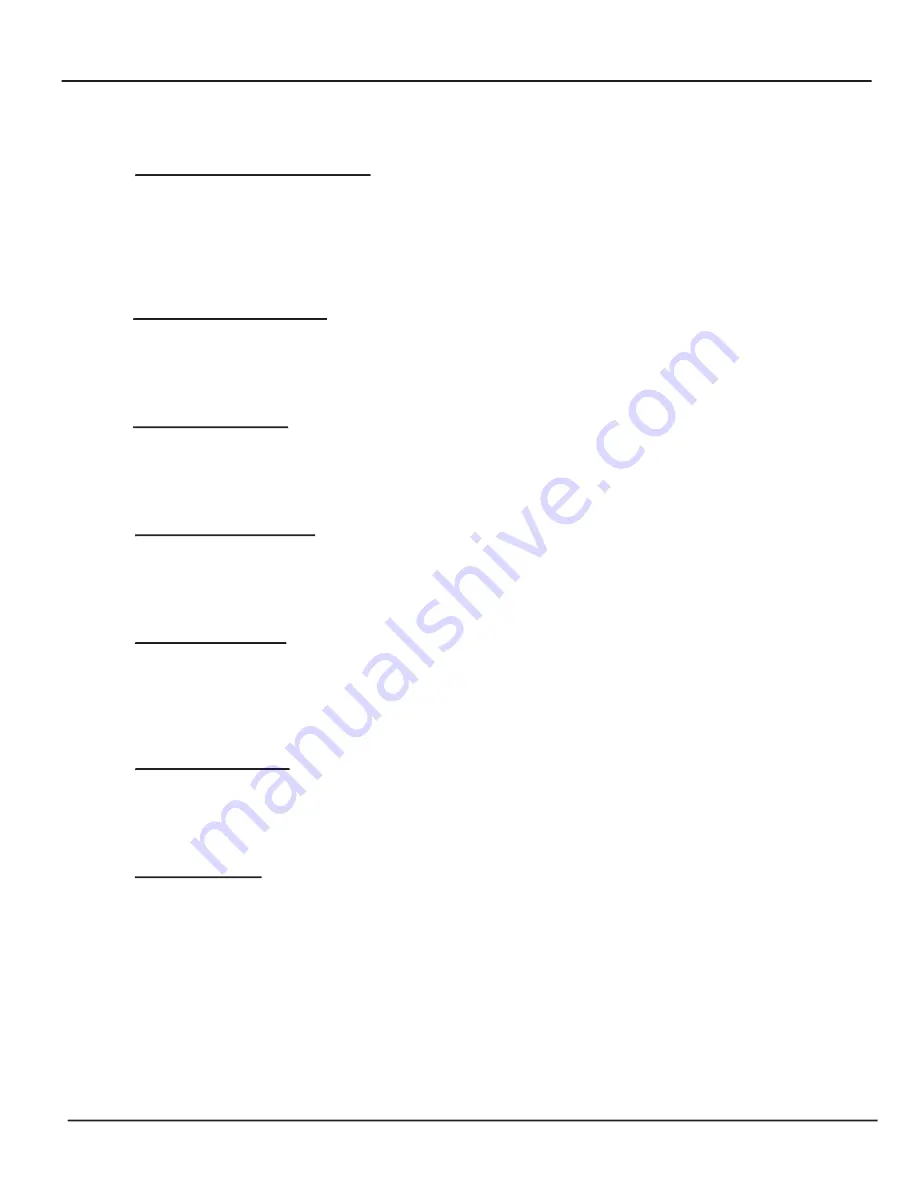
28
Automatic Control
APPENDIX I
Self Diagnosing Fault Codes
7. Proportional Voltage Diagnostics
Proportional Voltage Diagnostics
Description
: Danfoss Passive or Active fault monitoring
Location: Connector
– 10 socket
Pin
– B
Notes
: Passive Danfoss - Fault will clear when fault removed.
Active Danfoss - Fault will clear when fault removed and power cycled.
Possible External Causes:
PV signal exceeds 15% - 85% of supply, LVDT wires broken or shorted,
Spool position exceeds command.
9. Proportional Voltage Driver
Proportional Voltage Driver
Description
: Over current (>0.06 A)
Location: Connector
– 10 socket
Pin
– E
Notes
: Driver shuts off during fault. Fault will clear when fault removed
Possible External Causes:
Short in coil cables or connectors.
15. Remote Switch Driver
Description
: Over current
Location: Connector
– 7 socket
Pin
– F
Notes
: Fault will clear when fault removed
Possible External Causes:
Short in cables or connectors.
16. Receiver Communication
Description
: Loss of communication
Location: Connector
– 6 socket
Pin
– A,B,C,D
Notes
: Fault will clear when receiver communicates with the control box
Possible External Causes:
Loss of power to receiver, loss of communication with receiver.
18. Machine Low Voltage
Machine Low Voltage
Description
: Machine Power < 9.5V
Location: Connector
– 4 pin
Pin
– A,B,C,D
Notes:
Fault will clear when voltage returns to operating range.
Possible External Causes:
Low battery, voltage regulator, poor connections, undersized / over length
conductors.
19. Machine High Voltage
Machine High Voltage
Description
: Machine Power > 31.5V
Location: Connector
– 4 pin
Pin
– A,B,C,D
Notes:
Fault will clear when voltage returns to operating range. If sustained, fuse will blow.
Possible External Causes:
Voltage regulator, alternator, power spikes.
20. Internal Problems
Description
: Control Box Proc/Ram Check
Location: Connector
– N/A
Pin
– N/A
Notes:
Cycle control box power to clear fault. If fault doesn’t clear, control box needs serviced.
Possible External Causes:
Processor or RAM problems.