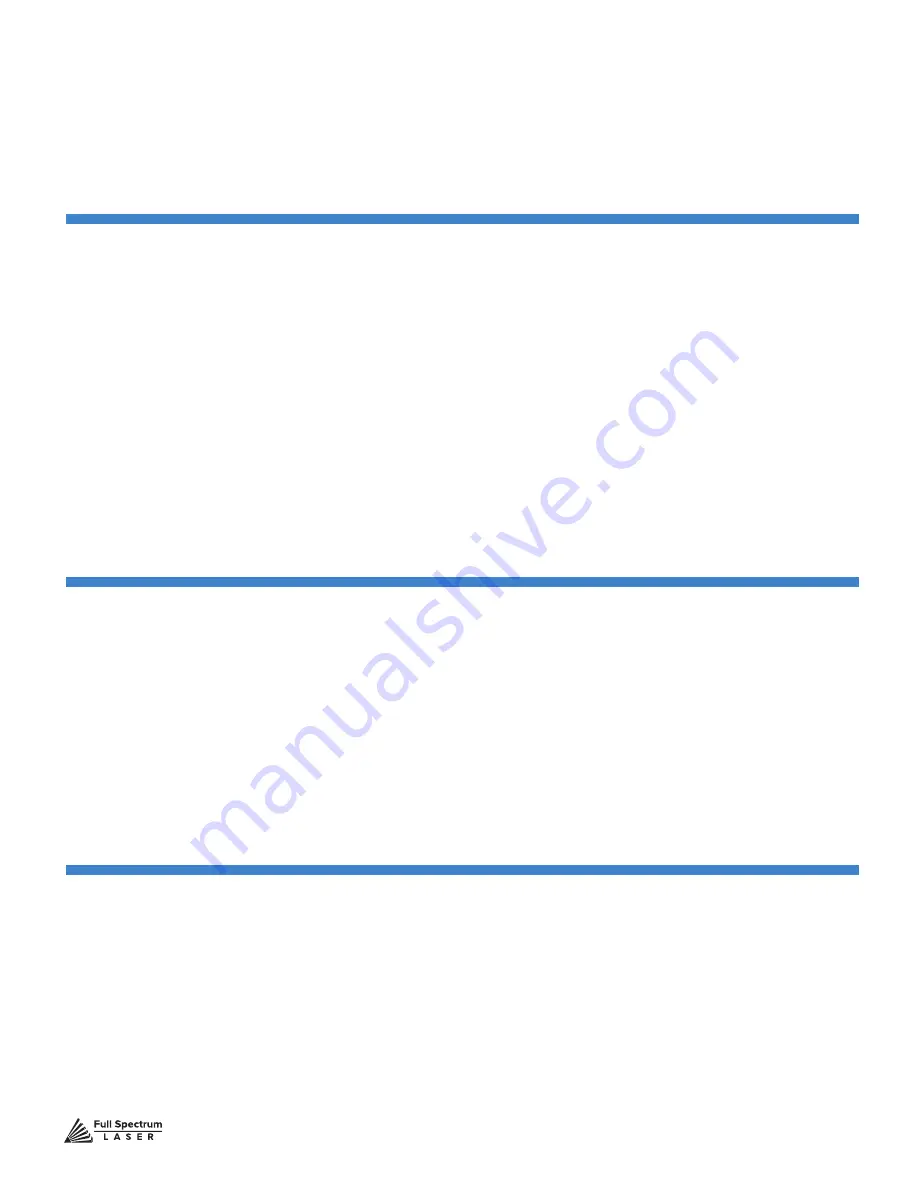
Technical Support is available from 8am to 5pm (PST) M - F at [email protected].
70
Appendix A: Troubleshooting
As w
ith any machinery, individual user results may vary. In this section we will discuss the most
common issues users report and the simple solutions to fix them and get back to work. If you cannot
find the solution to your problem in this section, please don’t hesitate to contact customer support for
personalized discussion of your issue.
PROBLEM: LASER DOES NOT FIRE .
POSSIBLE CAUSE
1. Laser cover is open or magnet wires are disconnected.
2. Water is flowing in the wrong direction or water sensor is not working.
SOLUTIONS
1. Make sure that the cover of your laser is closed during jobs or test fires. Check that the magnet
wires are connected to the terminals on the power supply.
2. Be sure that water is flowing from right to left through the laser tube. If confirmed and issue persists
contact support.
PROBLEM: ENGRAVED LINES ARE DIFFUSE; CUTTING FAILS EVEN AT HIGH POWER.
POSSIBLE CAUSE
1. Laser is not in focus.
SOLUTIONS
1. Check that your laser is in focus. Rest the included focus billet on top of your work piece. Loosen
the lens slide so the output nozzle rests on the focus billet. Retighten the slide.