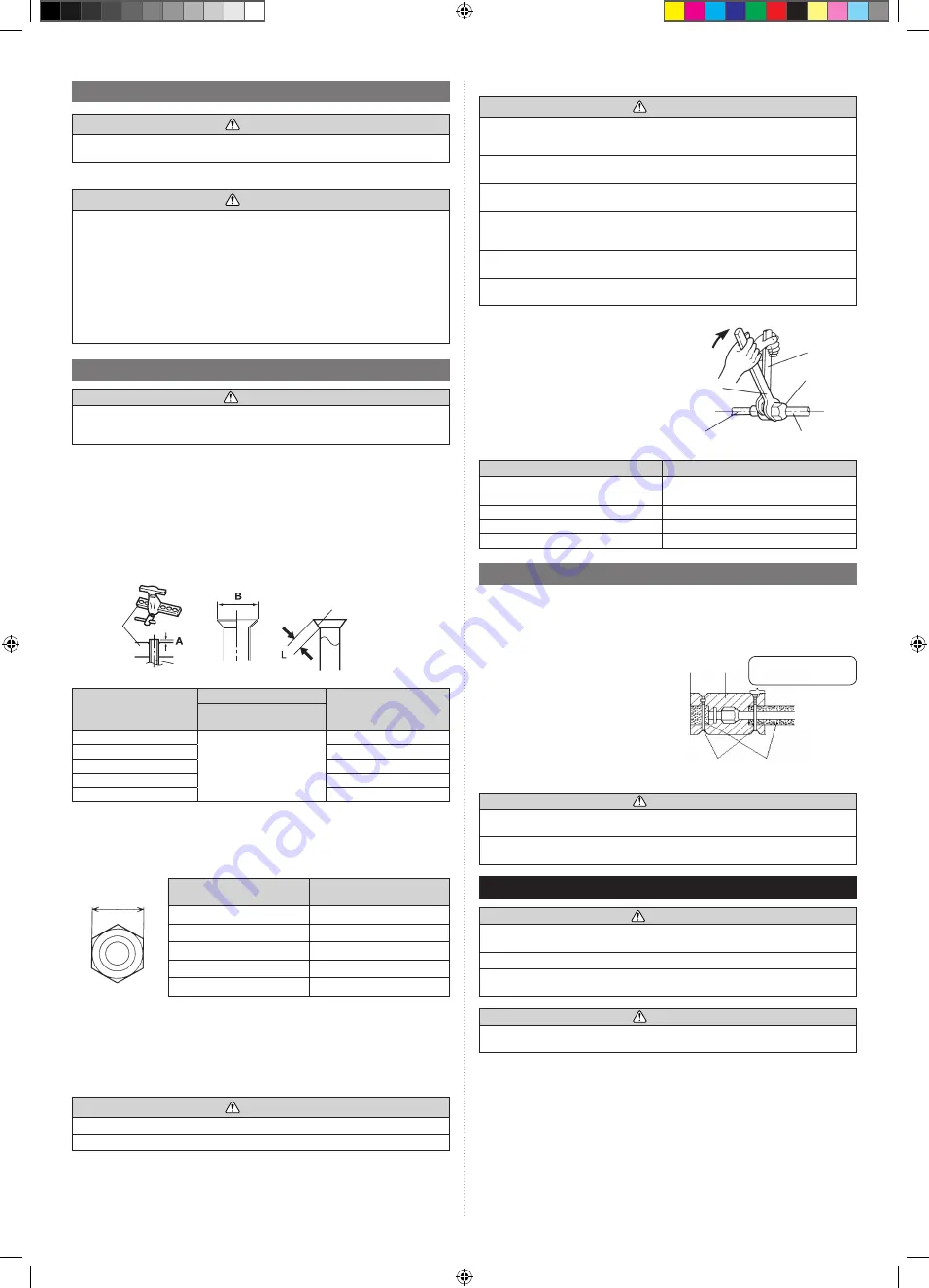
En-7
4.2. Pipe requirement
CAUTION
Refer to the Installation Manual of the outdoor unit for description of the length of con-
necting pipe or for difference of its elevation.
•
Use pipe with water-resistant heat insulation.
CAUTION
Install heat insulation around both the gas and liquid pipes. Failure to do so may cause
water leaks.
Use heat insulation with heat resistance above 248 °F (120 °C). (Reverse cycle model
only)
In addition, if the humidity level at the installation location of the refrigerant piping is
expected to exceed 70 %, install heat insulation around the refrigerant piping. If the
expected humidity level is 70 to 80 %, use heat insulation that is 9/16 in (15 mm) or
thicker and if the expected humidity exceeds 80 %, use heat insulation that is 13/16 in
(20 mm) or thicker. If heat insulation is used that is not as thick as specified, condensa-
tion may form on the surface of the insulation. In addition, use heat insulation with heat
conductivity of 0.045 W/(m·K) or less (at 68°F (20 °C).
4.3. Flare connection (pipe connection)
WARNING
Tighten the flare nuts with a torque wrench using the specified tightening method. Oth-
erwise, the flare nuts could break after a prolonged period, causing refrigerant to leak
and generate hazardous gas if the refrigerant comes into contact with a flame.
4.3.1. Flaring
•
Use special flare tool exclusive for R410A.
(1) Cut the connection pipe to the necessary length with a pipe cutter.
(2) Hold the pipe downward so that cuttings will not enter the pipe and remove any burrs.
(3) Insert the flare nut (always use the flare nut attached to the indoor and outdoor units
(or RB unit) respectively) onto the pipe and perform the flare processing with a flare
tool. Use the special R410A flare tool, Leakage of refrigerant may result if other flare
nuts are used.
(4) Protect the pipes by pinching them or with tape to prevent dust, dirt, or water from
entering the pipes.
Pipe
Die
Check if [L] is flared uniformly and
is not cracked or scratched.
Pipe outside diameter [in
(mm)]
Dimension A [in (mm)]
Dimension B
0 (0)
-0.015 (-0.4)
[in (mm)]
Flare tool for R410A, clutch
type
1/4 (6.35)
0 to 0.020
(0 to 0.5)
3/8 (9.1)
3/8 (9.52)
1/2 (13.2)
1/2 (12.70)
5/8 (16.6)
5/8 (15.88)
3/4 (19.7)
3/4 (19.05)
15/16 (24.0)
When using conventional (R22) flare tools to flare R410A pipes, the dimension A should
be approximately 0.020 in (0.5 mm) more than indicated in the table (for flaring with
R410A flare tools) to achieve the specified flaring. Use a thickness gauge to measure the
dimension A. It is recommended that a R410A flaring tool is used.
Width across
flats
Pipe outside diameter [in
(mm)]
Width across flats of Flare nut
[in (mm)]
1/4 (6.35)
11/16 (17)
3/8 (9.52)
7/8 (22)
1/2 (12.70)
1 (26)
5/8 (15.88)
1-1/8 (29)
3/4 (19.05)
1-7/16 (36)
4.3.2. Bending pipes
•
If pipes are shaped by hand, be careful not to collapse them.
•
Do not bend the pipes in an angle more than 90°.
•
When pipes are repeatedly bend or stretched, the material will harden, making it difficult
to bend or stretch them anymore.
•
Do not bend or stretch the pipes more than 3 times.
CAUTION
To prevent breaking of the pipe, avoid sharp bends.
If the pipe is bent repeatedly at the same place, it will break.
4.3.3. Pipe connection
CAUTION
Be sure to install the pipe against the port on the indoor unit correctly. If the centering
is improper, the flare nut cannot tighten smoothly. If the flare nut is forced to turn, the
threads will be damaged.
Do not remove the flare nut from the indoor unit pipe until immediately before connect-
ing the connection pipe.
Hold the torque wrench at its grip, keeping it at a right angle with the pipe, in order to
tighten the flare nut correctly.
Tighten the flare nuts with a torque wrench using the specified tightening method. Oth-
erwise, the flare nuts could break after a prolonged period, causing refrigerant to leak
and generate hazardous gas if the refrigerant comes into contact with a flame.
Connect the piping so that the control box cover can easily be removed for servicing
when necessary.
In order to prevent water from leaking into the control box, make sure that the piping is
well insulated.
When the flare nut is tightened
properly by your hand, hold the body
side coupling with a separate spanner,
then tighten with a torque wrench.
(See the table below for the flare nut
tightening torques.)
Tighten with
2 wrenches.
Holding
wrench
Flare nut
Connection pipe
Torque wrench
Indoor unit pipe
(body side)
Flare nut [in (mm)]
Tightening torque [lbf·ft (N·m)]
1/4 (6.35) dia.
11.8 to 13.3 (16 to 18)
3/8 (9.52) dia.
23.6 to 31.0 (32 to 42)
1/2 (12.70) dia.
36.1 to 45.0 (49 to 61)
5/8 (15.88) dia.
46.5 to 55.3 (63 to 75)
3/4 (19.05) dia.
66.4 to 81.1 (90 to 110)
4.4. Installing heat insulation
Install the heat insulation material after performing a refrigerant leak check (see the Instal-
lation Manual for the outdoor unit for details).
4.4.1. Coupler heat insulation
•
Insulate by the coupler heat insulation
(accessories) around the gas pipe and
liquid pipe of indoor side.
•
After installing the coupler heat insula-
tion, wrap both end with vinyl tape so
that there is no gap.
•
After affixing the coupler heat insula-
tion, secure it with 2 cable ties (large),
one on each end of the insulation.
•
Make sure that the cable ties overlap
the heat insulation pipe.
Coupler heat
insulation
(accessories)
Cover this portion with
heat insulation.
Cable tie (large)
(accessories)
Heat insulation
CAUTION
After checking for gas leaks (refer to the Installation Manual of the outdoor unit), per-
form this section.
Install heat insulation around both the large (gas) and small (liquid) pipes. Failure to do
so may cause water leaks.
5. INSTALLING DRAIN PIPES
WARNING
Do not insert the drain piping into the sewer where sulfurous gas occurs. (Heat ex-
change erosion may occur)
Insulate the parts properly so that water will not drip from the connection parts.
Check for proper drainage after the construction by using the visible portion of transpar-
ent drain port and the drain piping final outlet on the body.
CAUTION
Do not apply adhesive agent on the drain port of the body.
(Use the attached drain hose and connect the drain piping)
9374342556-02_IM.indb 7
27-Sep-19 10:30:00 AM