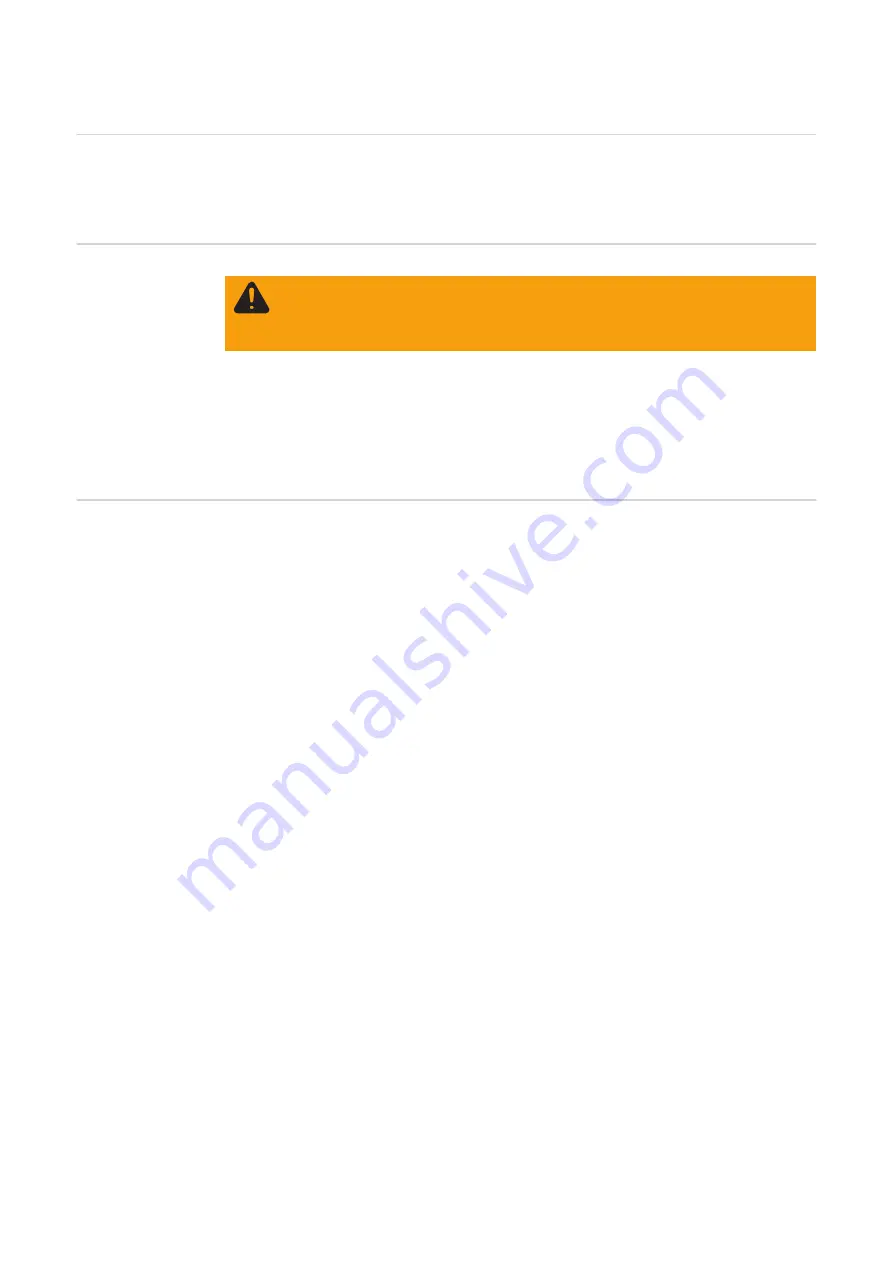
50
Care, maintenance and disposal
General
Under normal operating conditions, the device requires only a minimum of care and main-
tenance. However, it is vital to observe some important points to ensure the welding sys-
tem remains in a usable condition for many years.
Care and mainte-
nance
Observe the following points to ensure the KD 7000 gives you years of troublefree opera-
tion:
-
Carry out safety inspections at the stipulated intervals (see "Safety rules")
-
Depending on the installation location, but in any event at least twice a year, remove
the side panels and clean the KD 7000 with dry, reduced compressed air. Do not bring
the air nozzle too close to electronic components.
Disposal
Dispose of in accordance with the applicable national and local regulations.
WARNING!
An electric shock can be fatal. Before opening up the KD 7000, turn
the KD 7000 off at the mains switch, unplug the machine from the mains and put
up a warning sign to stop anybody inadvertently switching the machine back on
again.
Содержание KD 7000
Страница 2: ...2...
Страница 4: ...4...
Страница 30: ...30 TIG KD connection box wiring diagram...
Страница 32: ...32 KD 7000 wiring diagram...
Страница 45: ...45 EN 3 Inserting the wire spool 1 1 2 3 1 2 3 1...
Страница 52: ...52 Spare parts list KD 7000...
Страница 57: ...57...
Страница 58: ...58...
Страница 59: ...59...