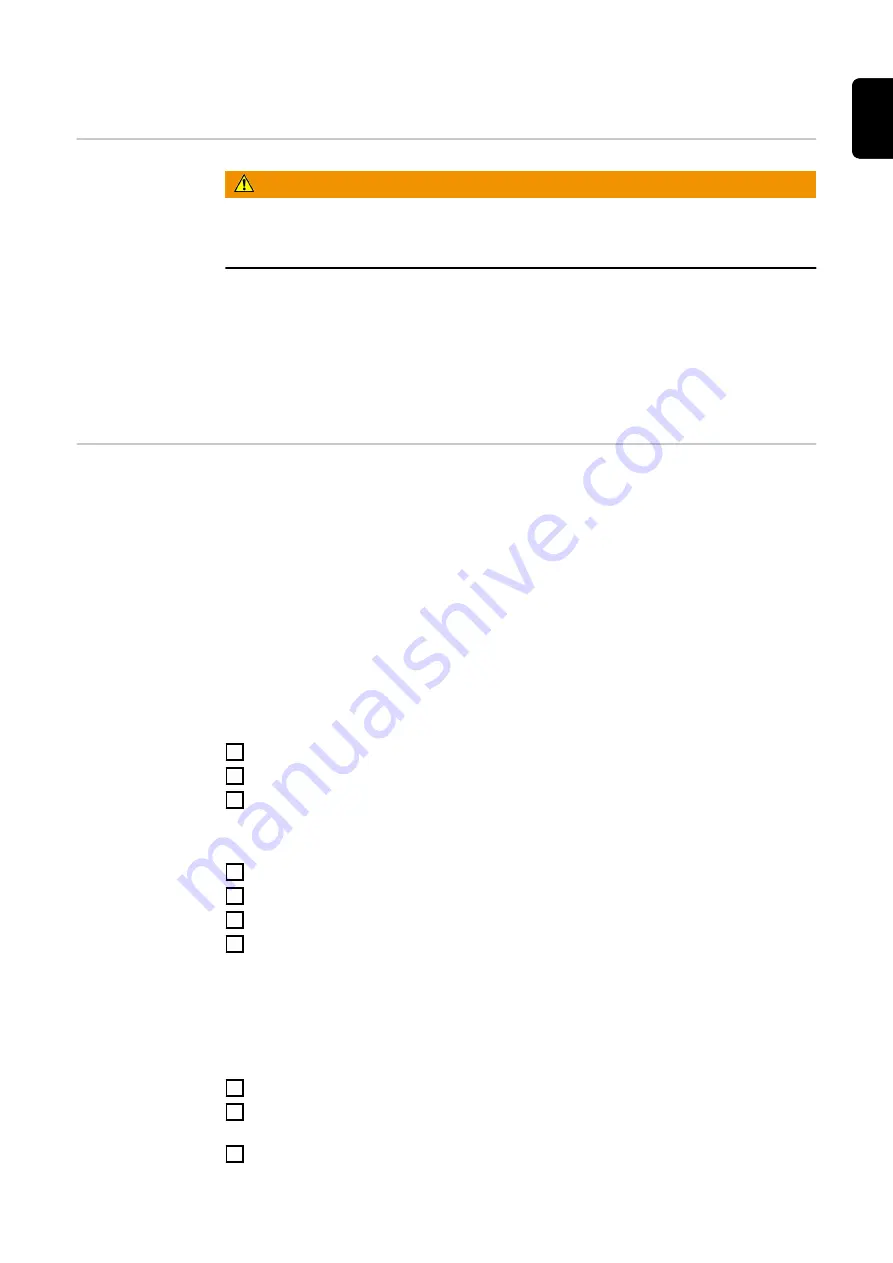
Before installation and initial operation
Setup regulations
WARNING!
Toppling or falling devices can be deadly.
▶
Set up all system components, upright brackets and trolleys so that they are stable
on a flat and solid surface.
The wirefeeder has been tested according to protection class IP 23. This means:
-
Protection against the penetration of solid foreign bodies with a diameter of more
than 12.5 mm (0.49 in.)
-
Protection against spraywater at any angle up to 60° from the vertical
The WF 30i TWIN wirefeeder can be set up and operated outdoors in accordance with
degree of protection IP 23. Direct moisture (e.g. from rain) must be avoided.
Installation –
overview
The following overview covers the installation work required for a TWIN welding system
in accordance with the system overview on page
The installation of similar TWIN systems is carried out analogously to this.
Initial situation:
-
The robot and robot controls are correctly positioned and fastened in the welding
cell.
-
The power sources are installed with the cooling units on the upright brackets and
correctly positioned and fastened in the welding cell.
-
The TWIN Controller is available and fastened close to the power sources (e.g., us-
ing a corresponding bracket directly on the power source).
-
The welding wire drums are correctly positioned and fixed in place.
Installing the TWIN wirefeeder and accessories on the robot
1
Install wirefeeder holder on the robot
2
Install wirefeeder on the wirefeeder holder
3
Install side holders for the interconnecting hosepacks on the robot
Laying, installing, and connecting interconnecting hosepacks
1
Connect interconnecting hosepacks to the wirefeeder
2
Fix interconnecting hosepacks in the side holder
3
Route interconnecting hosepacks to the power sources
4
Connect the interconnecting hosepacks to the power sources, cooling units, and
TWIN Controller
IMPORTANT!
Maintain a minimum distance of 30 - 50 cm between interconnecting
hosepacks to prevent any impairment of the welding results.
Connecting the TWIN Controller
1
Connect power sources to the TWIN Controller
2
Connect wirefeeder to the TWIN Controller (connect SpeedNet cable from the inter-
connecting hosepacks to the TWIN Controller)
3
Connect the TWIN Controller to the robot controls
79
EN-US
Содержание CMT Twin
Страница 2: ......
Страница 18: ...18...
Страница 19: ...General information 19...
Страница 20: ...20...
Страница 30: ...The balancer mounting Y piece can also be used instead of the robot support Y piece 30...
Страница 31: ...System components 31...
Страница 32: ...32...
Страница 44: ...44...
Страница 45: ...Welding Technology Aspects 45...
Страница 46: ...46...
Страница 64: ...64...
Страница 65: ...Operating controls connections and mechanical components 65...
Страница 66: ...66...
Страница 74: ...74...
Страница 75: ...Installation and commissioning TWIN Push 75...
Страница 76: ...76...
Страница 92: ...7 8 9 10 11 12 92...
Страница 96: ...1 2 4 1 5 96...
Страница 103: ...Installation and commissioning TWIN Push Pull CMT 103...
Страница 104: ...104...
Страница 126: ...7 8 9 10 11 12 126...
Страница 130: ...1 2 4 1 5 130...
Страница 137: ...Troubleshooting Maintenance and Disposal 137...
Страница 138: ...138...
Страница 146: ...146...
Страница 147: ...Technical data 147...
Страница 148: ...148...
Страница 159: ...159 EN US...