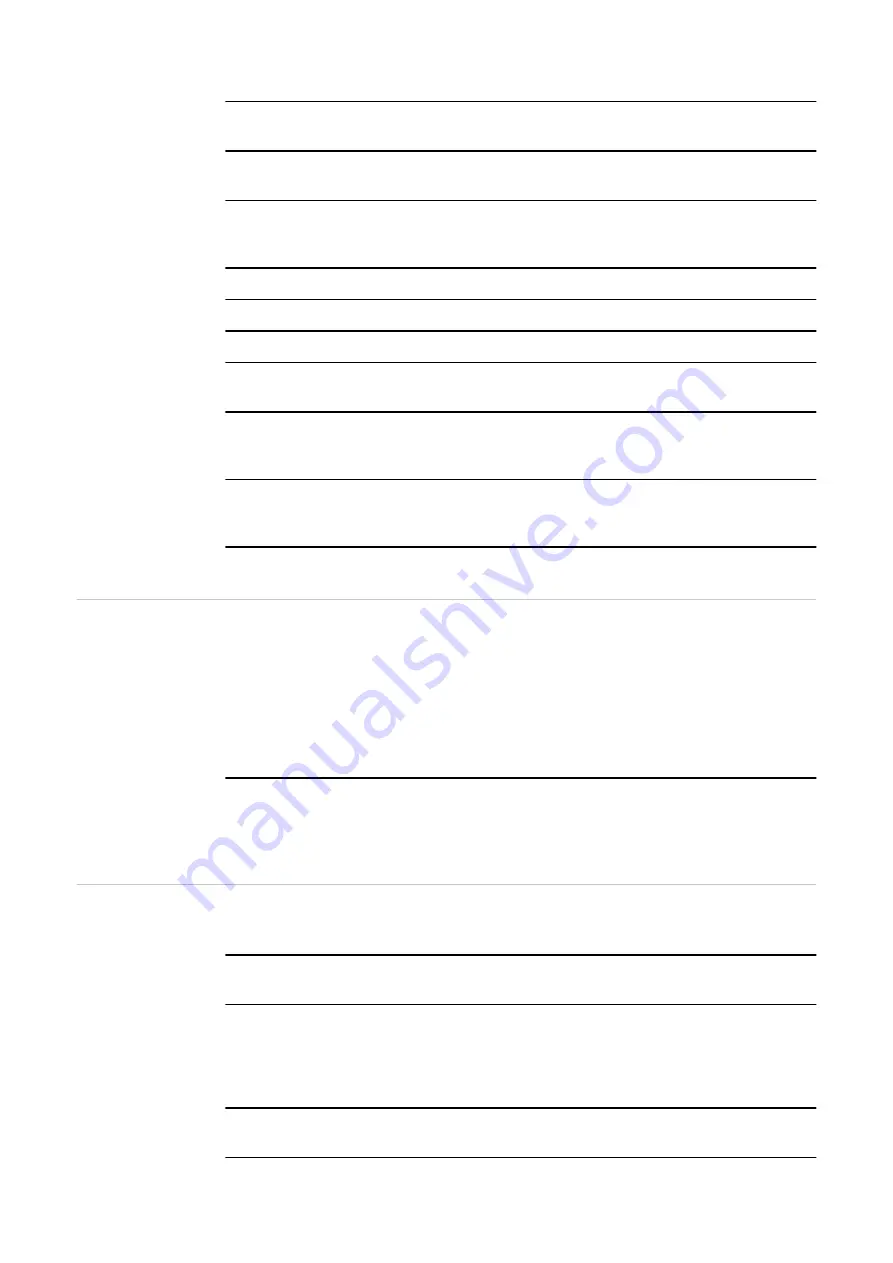
Before switching on the device, ensure that no one is likely to be endangered.
Check the device at least once a week for obvious damage and proper functioning of
safety devices.
Always fasten the shielding gas cylinder securely and remove it beforehand if the device
is to be transported by crane.
Only the manufacturer's original coolant is suitable for use with our devices due to its
properties (electrical conductibility, anti-freeze agent, material compatibility, flammability,
etc.).
Only use suitable original coolant from the manufacturer.
Do not mix the manufacturer's original coolant with other coolants.
Only connect the manufacturer's system components to the cooling circuit.
The manufacturer accepts no liability for damage resulting from use of other system
components or a different coolant. In addition, all warranty claims will be forfeited.
Cooling Liquid FCL 10/20 does not ignite. The ethanol-based coolant can ignite under
certain conditions. Transport the coolant only in its original, sealed containers and keep
well away from any sources of ignition.
Used coolant must be disposed of properly in accordance with the relevant national and
international regulations. The coolant safety data sheet may be obtained from your ser-
vice centre or downloaded from the manufacturer's website.
Check the coolant level before starting to weld, while the system is still cool.
Commissioning,
maintenance and
repair
It is impossible to guarantee that bought-in parts are designed and manufactured to meet
the demands made of them, or that they satisfy safety requirements.
-
Use only original spare and wearing parts (also applies to standard parts).
-
Do not carry out any modifications, alterations, etc. to the device without the manu-
facturer's consent.
-
Components that are not in perfect condition must be replaced immediately.
-
When ordering, please give the exact designation and part number as shown in the
spare parts list, as well as the serial number of your device.
The housing screws provide the ground conductor connection for earthing the housing
parts.
Only use original housing screws in the correct number and tightened to the specified
torque.
Safety inspection
The manufacturer recommends that a safety inspection of the device is performed at
least once every 12 months.
The manufacturer recommends that the power source be calibrated during the same 12-
month period.
A safety inspection should be carried out by a qualified electrician
-
after any changes are made
-
after any additional parts are installed, or after any conversions
-
after repair, care and maintenance has been carried out
-
at least every twelve months.
For safety inspections, follow the appropriate national and international standards and
directives.
18
Toowoomba Welding Supplies : tweld.com.au : Ph +61 7 4659 0044
Содержание CMT 4000 Advanced
Страница 2: ...Toowoomba Welding Supplies tweld com au Ph 61 7 4659 0044...
Страница 20: ...20 Toowoomba Welding Supplies tweld com au Ph 61 7 4659 0044...
Страница 21: ...General information 21 Toowoomba Welding Supplies tweld com au Ph 61 7 4659 0044...
Страница 22: ...22 Toowoomba Welding Supplies tweld com au Ph 61 7 4659 0044...
Страница 30: ...30 Toowoomba Welding Supplies tweld com au Ph 61 7 4659 0044...
Страница 31: ...Control elements and connections 31 Toowoomba Welding Supplies tweld com au Ph 61 7 4659 0044...
Страница 32: ...32 Toowoomba Welding Supplies tweld com au Ph 61 7 4659 0044...
Страница 71: ...Installation and commissioning 71 Toowoomba Welding Supplies tweld com au Ph 61 7 4659 0044...
Страница 72: ...72 Toowoomba Welding Supplies tweld com au Ph 61 7 4659 0044...
Страница 95: ...Welding 95 Toowoomba Welding Supplies tweld com au Ph 61 7 4659 0044...
Страница 96: ...96 Toowoomba Welding Supplies tweld com au Ph 61 7 4659 0044...
Страница 131: ...Setup settings 131 Toowoomba Welding Supplies tweld com au Ph 61 7 4659 0044...
Страница 132: ...132 Toowoomba Welding Supplies tweld com au Ph 61 7 4659 0044...
Страница 173: ...Troubleshooting and maintenance 173 Toowoomba Welding Supplies tweld com au Ph 61 7 4659 0044...
Страница 174: ...174 Toowoomba Welding Supplies tweld com au Ph 61 7 4659 0044...
Страница 188: ...188 Toowoomba Welding Supplies tweld com au Ph 61 7 4659 0044...
Страница 189: ...Appendix 189 Toowoomba Welding Supplies tweld com au Ph 61 7 4659 0044...
Страница 190: ...190 Toowoomba Welding Supplies tweld com au Ph 61 7 4659 0044...
Страница 209: ...209 EN Toowoomba Welding Supplies tweld com au Ph 61 7 4659 0044...
Страница 210: ...210 Toowoomba Welding Supplies tweld com au Ph 61 7 4659 0044...
Страница 211: ...211 EN Toowoomba Welding Supplies tweld com au Ph 61 7 4659 0044...
Страница 212: ...Toowoomba Welding Supplies tweld com au Ph 61 7 4659 0044...