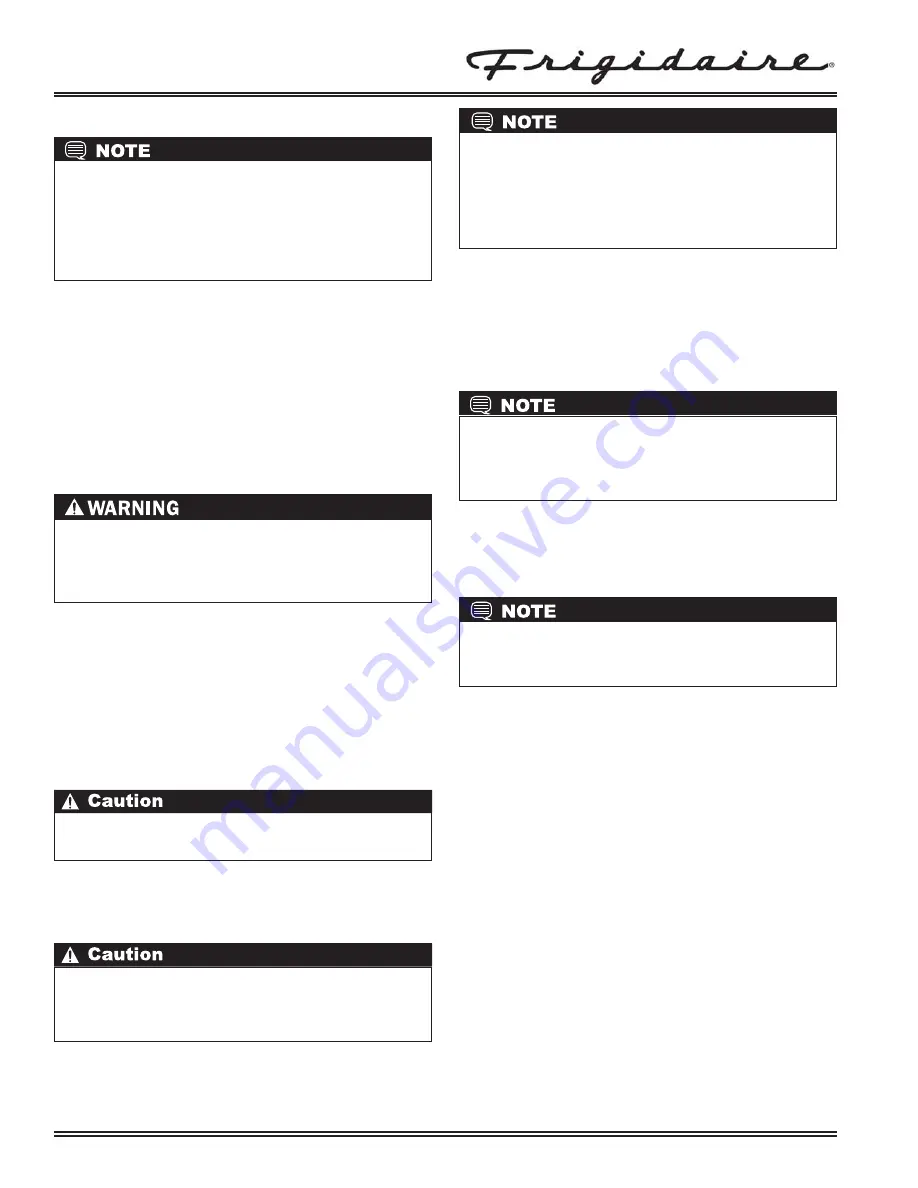
A new compressor which is cold (e.g. after having been
kept in a cold service van) should be left to warm to the
surrounding temperature before the plugs on the
compressor connections are removed. This will help
prevent condensation from forming in the oil and the
compressor. Also, avoid opening the system when any
of the components or lines are cold.
1. Disconnect electrical supply to refrigerator.
2. Remove compressor access panel.
3. Remove all components needed to pull the
compressor assembly from the unit.
4. Pull compressor assembly straight out.
5. Recover refrigerant by using EPA approved
recovery system.
6. Remove leads from compressor motor terminals.
7. Remove mounting clips and washers.
8. After refrigerant is completely recovered, cut
suction and discharge lines as close to compressor
as possible. Leave only enough tubing to pinch off
and seal defective compressor. Plug or tape any
open system tubing to avoid entrance of moisture
and air into system. Remove inoperable
compressor and transfer mounting parts to new
compressor.
9. Install new compressor in exact same manner as
original compressor.
3-6
Refrigeration System
Release holding charge (release slowly to avoid
oil discharge) on new compressor to ensure
there is no leak in seam or tubing. Reinstall
rubber plug.
The following instructions are generalized to
help the technician understand the procedures
of sealed system repairs. See Section 5
Component Teardown on the exact steps of
accessing the components of the refrigeration
system.
If low-side process tube is too short, silver
solder four inch piece of tubing onto process
tube at this time.
Installing a New Compressor
Replacement of compressor and installation of
filter-drier must be done in a continuous sequence so
system is exposed to atmosphere no longer than
necessary.
All replacement compressors are shipped with
rubber plugs in the suction, discharge and process
tubes and contain the correct oil charge and a holding
charge of inert gas. Compressors have a low-side
process tube attached to the compressor shell. A
high-side process tube is attached to the filter-drier.
Replacement compressors for refrigerators may have an
oil cooler even if the original compressor did not. If the
product is not equipped for an oil cooler, leave the
plastic caps in place and install the compressor
connecting only to the suction and discharge lines of the
new compressor.
Before installing the replacement compressor remove
the discharge plug and check for the pop sound of the
inert gas leaving the compressor.
If the compressor checks OK, reinstall the plug. Do not
remove any of the plugs again until the compressor is in
position and you are ready to braze the lines.
Entirely new compressors have been developed
for use with R-134a and Ester oil refrigeration
systems. Both compressor and electric motor
have been modified. Old compressors intended
for R-12 refrigerant must not be used for new
systems charged with R-134a.
DO NOT use compressor if you do not hear this
sound.
On R-134a systems, compressor must NOT be left
open to atmosphere for more than 10 minutes to
prevent moisture contamination of oil.
DO NOT OPERATE RECIPROCATING
COMPRESSOR WHEN CHARGING LIQUID
REFRIGERANT INTO SYSTEM THROUGH ITS
PROCESS TUBE.
Содержание FKCH17F7HW
Страница 2: ......
Страница 3: ...Basic Information 1 1 Section 1 Basic Information ...
Страница 9: ...Electronic Control 2 1 Section 2 Electronic Control ...
Страница 14: ...2 6 Electronic Control Notes ...
Страница 15: ...3 1 Refrigeration System Section 3 Refrigeration System ...
Страница 30: ...3 16 Refrigeration System HFC 134a CFC 12 Pressure Temperature Chart ...
Страница 33: ...4 1 Component Teardown Section 4 Component Teardown ...
Страница 47: ...5 1 Troubleshooting Section 5 Troubleshooting ...
Страница 52: ...5 6 Troubleshooting Notes ...
Страница 53: ...6 1 Wiring Diagrams Section 6 Wiring Diagrams ...
Страница 54: ...6 2 Wiring Diagrams 7 4 6 2 8 3 5 1 ...
Страница 56: ...7 1 Section 7 Installation Information Installation Information ...
Страница 62: ...7 7 Installation Information Model FKCH17F7HW Unit Dimensions ...
Страница 63: ...7 8 Installation Information Notes ...