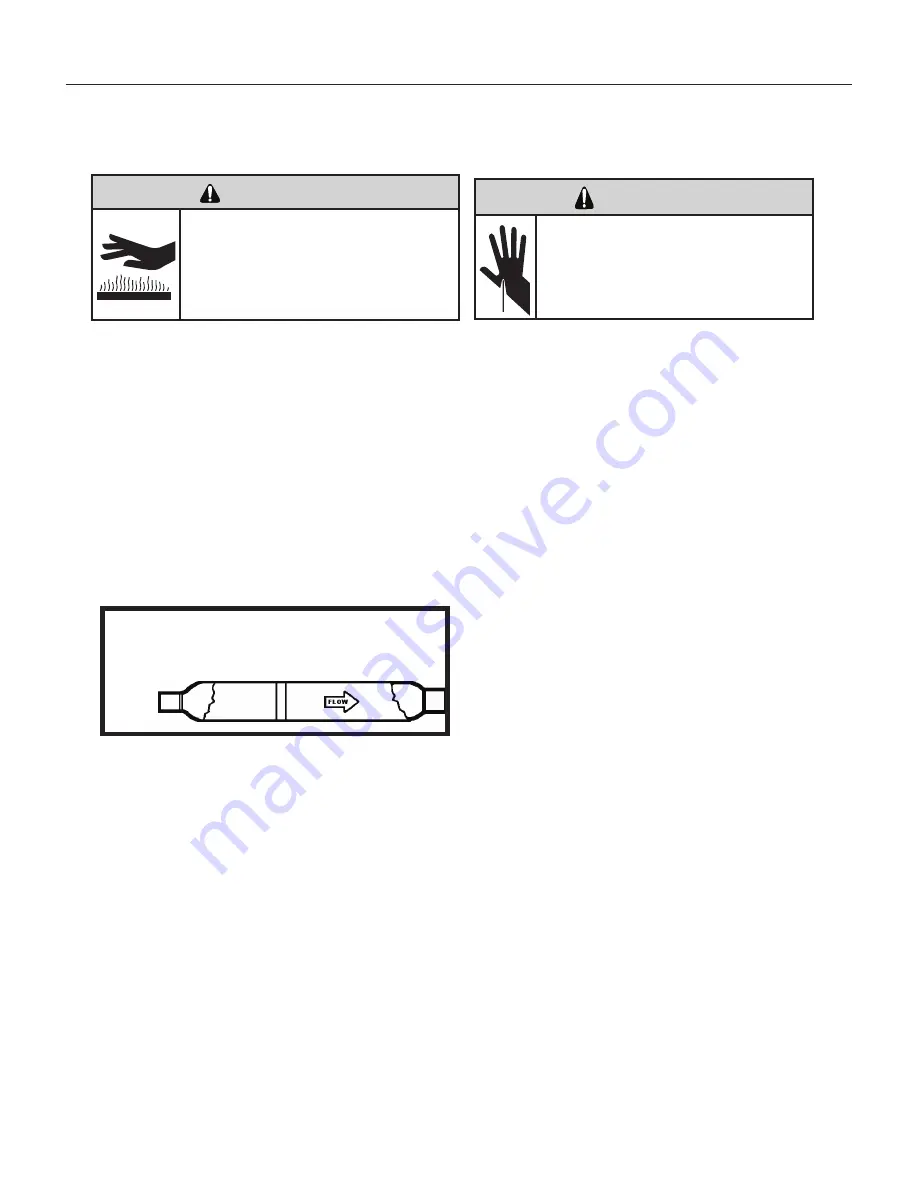
28
PB
Metering Device - Capillary Tube Systems
All units are equipped with capillary tube metering devices. Checking for restricted capillary tubes.
1. Connect pressure gauges to unit.
2. Start the unit in the cooling mode. If after a few minutes of operation the pressures are normal, the check valve and the
cooling capillary are not restricted.
3. Switch the unit to the heating mode and observe the gauge readings after a few minutes running time. If the system
pressure is lower than normal, the heating capillary is restricted.
4. If the operating pressures are lower than normal in both the heating and cooling mode, the cooling capillary is restricted.
Check Valve
A unique two-way check valve is used on the reverse cycle heat pumps. It is pressure operated and used to direct the flow of
refrigerant through a single filter drier and to the proper capillary tube during either the heating or cooling cycle.
NOTE:
The slide (check) inside the valve is made of teflon. Should it become necessary to replace the check valve, place a wet
cloth around the valve to prevent overheating during the brazing operation.
CHECK VALVE OPERATION
In the cooling mode of operation, high pressure liquid enters
the check valve forcing the slide to close the opposite port
(liquid line) to the indoor coil. Refer to refrigerant flow chart.
This directs the refrigerant through the filter drier and
cooling capillary tube to the indoor coil.
In the heating mode of operation, high pressure refrigerant
enters the check valve from the opposite direction, closing
the port (liquid line) to the outdoor coil. The flow path of
the refrigerant is then through the filter drier and heating
capillary to the outdoor coil.
Failure of the slide in the check valve to seat properly in
either mode of operation will cause flooding of the cooling
coil. This is due to the refrigerant bypassing the heating or
cooling capillary tube and entering the liquid line.
COOLING MODE
In the cooling mode of operation, liquid refrigerant from condenser (liquid line) enters the cooling check valve forcing the
heating check valve shut. The liquid refrigerant is directed into the liquid dryer after which the refrigerant is metered through
cooling capillary tubes to evaporator. (Note: liquid refrigerant will also be directed through the heating capillary tubes in a
continuous loop during the cooling mode).
HEATING MODE
In the heating mode of operation, liquid refrigerant from the indoor coil enters the heating check valve forcing the cooling
check valve shut. The liquid refrigerant is directed into the liquid dryer after which the refrigerant is metered through the
heating capillary tubes to outdoor coils. (Note: liquid refrigerant will also be directed through the cooling capillary tubes in a
continuous loop during the heating mode).
COMPONENT TESTING
Hermetic Components Check
BURN HAZARD
Proper safety procedures must be followed,
and proper protective clothing must be worn
when working with a torch.
Failure to follow these procedures could
result in moderate or serious injury.
WARNING
WARNING
CUT/SEVER HAZARD
Be careful with the sharp edges and corners.
Wear protective clothing and gloves, etc.
Failure to do so could result in serious injury.
One-way Check Valve
(Heat Pump Models)
Figure 701 (Check Valve)
Содержание UCT08A10A
Страница 14: ...14 OPERATION Control Panel mode and or HEAT...
Страница 44: ...44 WIRING DIAGRAMS ChillPremierCCF Figure 801 Models CCF05A10A CCF06A10A CCF08A10A CCF10A10A CCF12A10A E...
Страница 45: ...45 WIRING DIAGRAMS ChillPremierCCW Models CCW06B10A CCW24B30A Figure 802...
Страница 46: ...46 WIRING DIAGRAMS ChillPremierCCW CCW08B10A odels Models CCW10B10A CCW12B10A CCW15B10A Figure 803...
Страница 73: ...73 THIS PAGE LEFT INTENTIONALLY BLANK...