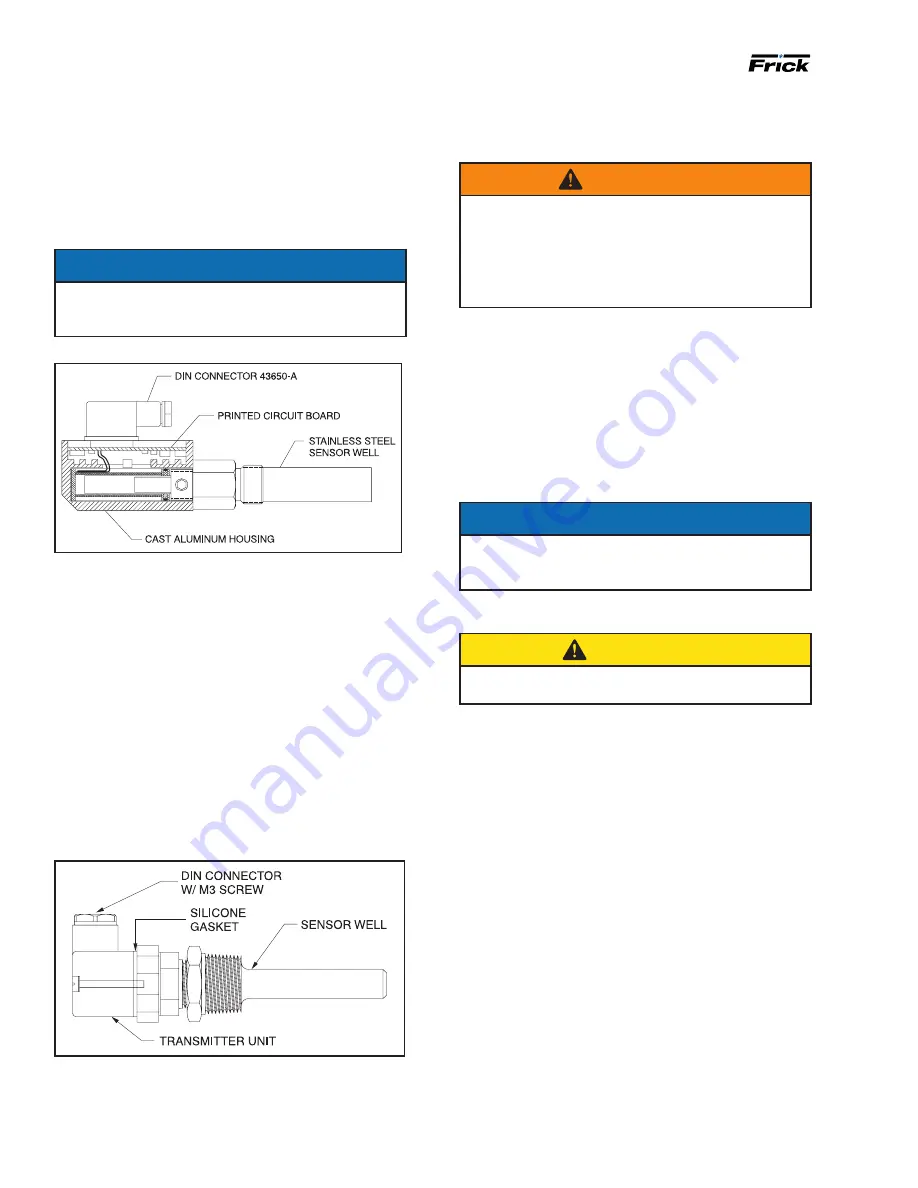
070.610-IOM (JUL 21)
Page 48
RWF II Rotary Screw Compressor Units
Maintenance
1.
Shut off control power.
2.
Remove
DIN connector plug from transmitter.
3.
Loosen set screws.
4.
Remove transmitter unit.
5.
Install new transmitter unit.
6.
Tighten set screws.
7.
Apply DIN connector plug to transmitter.
8.
Turn on control power.
NOTICE
For calibration of the volume ratio control unit, refer
to the Calibration Instructions in publication
090.040-O
.
Figure 50: Volume ratio control transmitter
Temperature sensor
Troubleshooting
Confirm the setup of the channel on the calibration or
analog board #1 setup screen. Is the temperature probe
reading bottom end -459°F or top end +463°F? If reading
bottom end, the probe or wire(s) to the probe are open or
the probe is shorted to ground pulling down the power/
excitation. Check the power at the analog board between
the + and – of the channel for that probe. In Example,
discharge temperature would be Channel 2 on the P4A
terminal strip of the analog board. Is there a signal of
12 VDC to 15 VDC? If yes, the probe is not shorted to
ground but is most likely open. Do continuity tests to
determine if it is the wiring or the sensor that is open.
Correct as necessary.
Figure 51: Temperature transmitter
If reading top end, the sensor is being shunted and full
signal is coming back to the board. Check the wiring by
unplugging the connector at the sensor, disconnecting
from the analog board, and doing a continuity test across
the wires removed from the board. If this is open, the
shunt is in the sensor. It is always a good idea to physically
inspect the wiring of t
he
DIN Plug.
WARNING
Be extremely careful not to loosen thermowell while
attempting to remove the temperature sensor.
The use of two wrenches will be necessary to ensure
the thermowell remains stationary. Loss of oil and/or
refrigerant could occur. Exposure to refrigerant fumes
and/or hot oil can cause injury or death.
Replacement
1.
Shut off control power.
2.
Remove
DIN connector plug from transmitter. See Figure
above.
3.
Unscrew knurled ring and remove
transmitter unit.
4.
Apply thermal compound to new sensor assembly,
insert into
thermal well, and tighten knurled ring.
5.
Apply DIN connector plug to transmitter.
6.
Turn on control power.
NOTICE
The temperature sensor is factory set. If calibration is
required, refer to Calibration Instructions in publica-
tion
090.040-O
for service technicians.
Oil level transmitter
CAUTION
This device is static sensitive. Please follow proper
ESD procedures when handling.
Troubleshooting
Are the red indicator lights on at the sensor? If yes, check
that 2CR or OLCR is energized and that module 13 of digi
-
tal board #1 is energized as well as the status of module
13 is ON at the service screen for digital board #1. Correct
as necessary. If No, is there oil present in the lower sight
glass of the separator? If No, add oil to the separator. If
Yes, confirm that 24 VDC is getting to the sensor for exci
-
tation. If yes, replace the oil level sensor. If No, check the
fuse of wire 1001. If blown, check for shorts of wire 1001;
correct and replace the fuse. If the fuse is good, check
for 24 VDC immediately upstream of the fuse back to the
power supply. Correct as necessary.
Replacement
The
Oil Level Transmitter is located on the front of the
separator near the bottom/center. See Figure below.
The linear transmitter with hermetic enclosure is based on
the capacitive measuring principle. It features removable
electronics (from the sensor well) eliminating the need to
evacuate the compressor for replacement. This transmitter
is dedicated to
oil level control and has no user adjust
-
ments.