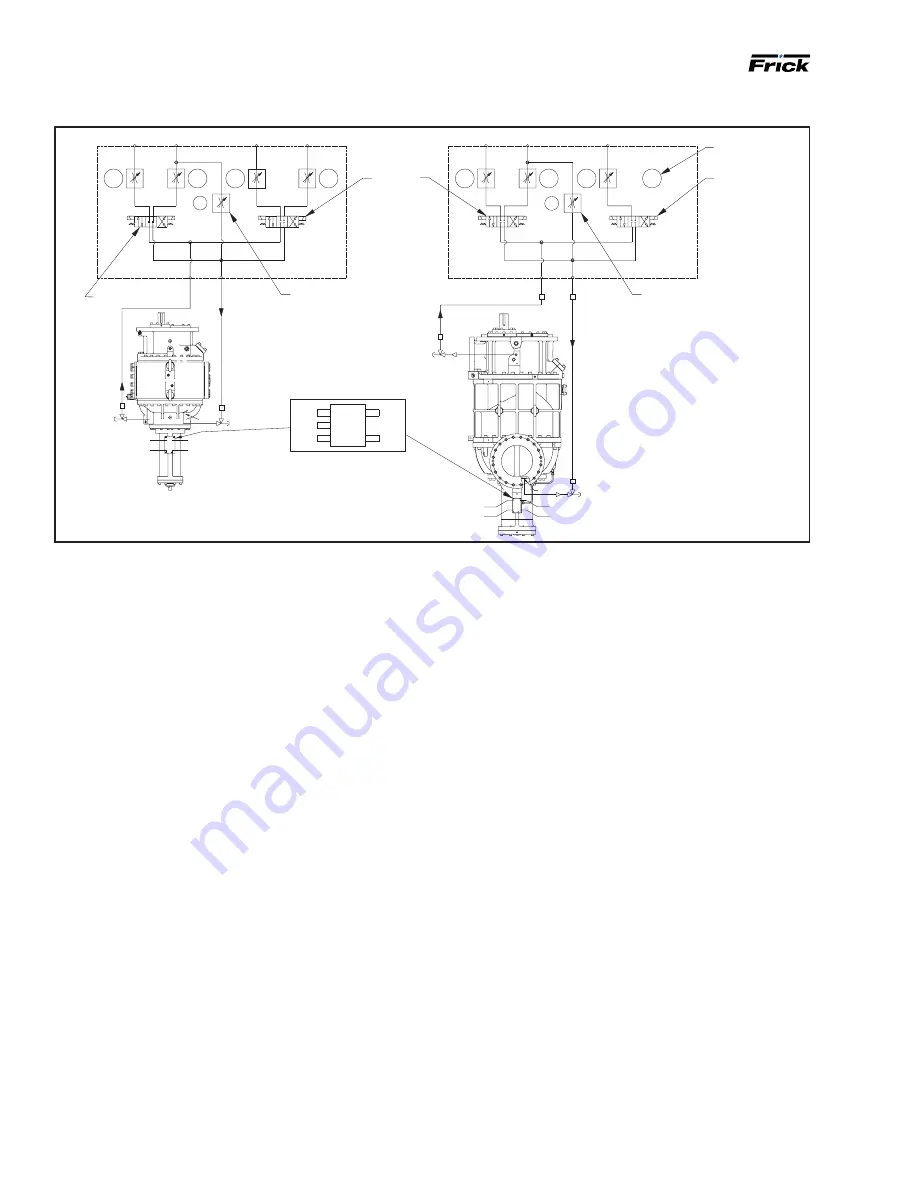
070.610-IOM (JUL 21)
Page 26
RWF II Rotary Screw Compressor Units
Operation
from the
oil manifold through valve ports P and A to com
-
pressor port SC3, enters the increase side of the cylinder
and overcomes the decrease spring tension. Simultane
-
ously, oil flows from SC4 port through valve ports B and T
to compressor suction. On models 496, 676, 856, and 1080
the SC4 port does not exist. The inboard side of the slide
stop piston is at suction pressure.
Compressor Vi decrease:
The volume ratio Vi is de
-
creased when MSS solenoid valve YY4 is energized and
oil flows from the oil manifold through valve ports P and
B to compressor port SC4, enters the decrease side of the
cylinder. Simultaneously, oil flows form SC3 port through
valve ports A and T to compressor suction. On models
496, 676, 856, and 1080 the SC4 port does not exist. On
these models, YY4 is energized which permits oil to vent
from port A to T with assistance from the
unloader spring.
Note:
To control the rate of Vi change, throttle the needle
valve at SC3 port.
Compressor oil cooling systems
The RWF II unit can be equipped with one of several sys-
tems for controlling the
compressor oil tempera ture. They
are single or
dual-port
liquid injection and thermo syphon or
water-cooled oil coolers. Each system is autom ati cally con-
trolled, independent of compressor loading or unloading.
Oil cooling systems should maintain oil temperature within
the following ranges for R-717:
Liquid injection
External*
Oil cooling
Oil cooling
130°F to 170°F
120°F to 160°F
* Thermosyphon oil cooling (TSOC) or water-cooled oil
cooling (WCOC).
A
P
DIRECTION
CONTROL VALVE
SV-2
Valve 1
Valve 1
Valve 2
Valve 2
P
T
SC2
1
P
T
A
B
2
SC1
SC1
1
1
BP
1
2
SC2
2
2
SC3
SC3
SCREW IN FLOW
REGULATING
NEEDLE VALVE
SV-3
1
T
B
SC4
2
SC4
DIRECTION
CONTROL
VALVE
HYDRAULIC SCHEMATIC
SIZES: 100-480, 546
P
T
YY4 (DECREASE VI)
YY2 (LOAD)
(INCREASE VI) YY3
(UNLOAD) YY1
SC4
BP
SC2
SC3
SC1
YY1
YY2
YY3
YY4
SC3
2
SC4
SC3
1
2
SC2
SC1
2
SC2
1
1
2
A
B
1
P
T
BP
B
A
T
P
SC1
SV-3
T
HYDRAULIC SCHEMATIC
SIZES: 496, 676, 856, 1080
P
SV-2
SCREW IN FLOW
REGULATING
NEEDLE VALVE
SC 4 NOT USED
DIRECTION
CONTROL VALVE
SC-5
SP-1
YY2 (LOAD)
YY4 (DECREASE VI)
COMPRESSOR TOP VIEW
COMPRESSOR TOP VIEW
YY1
YY2
YY3
YY4
(UNLOAD) YY1
(INCREASE VI) YY3
Single-port liquid injection
The
single-port liquid injection system is desig ned to per
-
mit liquid refrigerant injection into one port on the com
-
pressor at any given moment and operates as outlined.
The liquid injection solenoid valve is energized by the
micro processor when the temperature sensor, in stalled in
the compressor discharge, exceeds the setpoint. High-
pressure liquid
refriger ant is then supplied to the tempera-
ture control valve (TCV). See
to
for
piping and instrumentation drawings.
Dual-port liquid injection
The dual-port liquid injection system is design ed to obtain
the most efficient compressor performance at high and
low compression ratios by permitting injection of
liquid
refriger ant into one of two ports optimally located on
the com pressor. This minimizes the performance penalty
incurred with liquid injection oil cooling.
The dual-port system contains all the com ponents of the
single-port system with the addition of a
3-way motorized
valve and operates as outlined.
The liquid injection solenoid valve is energized by the
microprocessor when the temperature sensor, installed
in the compressor discharge, exceeds the setpoint. Then,
liquid refrigerant flows through the motorized expansion
valve to the 3-way motorized valve. Depending on the
compressor’s operating volume ratio (Vi), the micropro
-
cessor will select the flow of the liquid refrigerant to the
optimum compressor port.
Figure 29: Hydraulic schematic - all package sizes