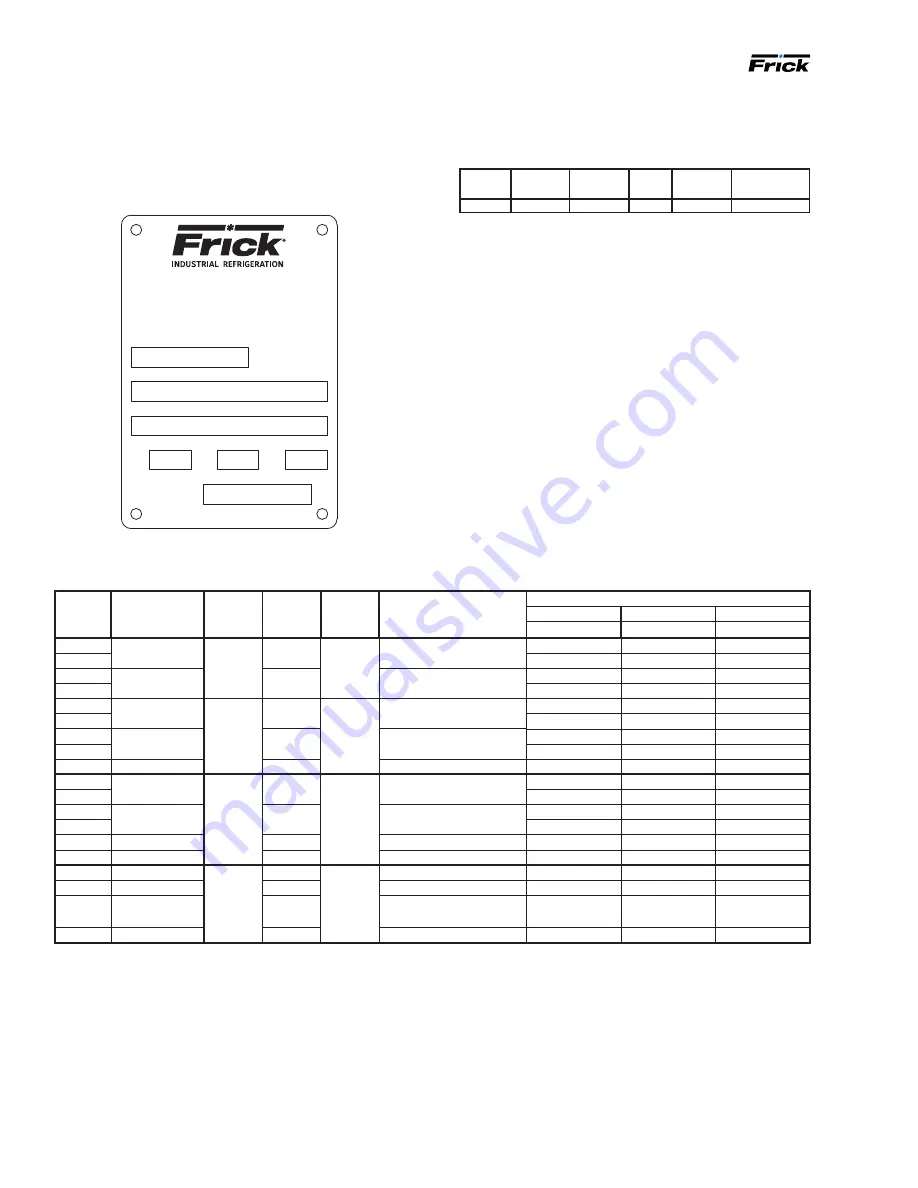
070.610-IOM (JUL 21)
Page 4
RWF II Rotary Screw Compressor Units
General Information
Compressor identification
Each compressor has an
identification data plate (see
below), containing compressor model and
serial number
mounted on the compressor body.
Figure 2: Compressor data plate
534B2722
COMPRESSOR SHAFT
CLOCKWISE ROTATION
534B2721
534B2720
534B2719
R22
COMPRESSOR OPERATES ON AND IS
COMPATIBLE WITH THE FOLLOWING
REFRIGERANTS
R290, R1270, NATURAL GAS
COMPRESSOR OPERATES ON AND IS
COMPATIBLE WITH THE FOLLOWING
REFRIGERANTS
R50, R134a, R170, R290, R404A, R410A, R507,
R513A, R600, R600A, R717, R728, R729, R744,
R1150, NATURAL GAS
COMPRESSOR OPERATES ON AND IS
COMPATIBLE WITH THE FOLLOWING
REFRIGERANTS
534C2934H01
SGXB2 4021
US2430125370500010
10241A89999999R
3600
600
41
USA
REFERENCE MATERIAL FIELD ON
SHEET 1 OF PRODUCTION ORDER
REFERENCE TABLE ON
SHEET 2 AND NOTE 3
REFERENCE TABLE
ON SHEET 2
REFERENCE TABLE ON
SHEET 2 AND NOTE 2
GENERATED BY SAP
ASSEMBLY PLANT LOCATION
534C2933H01
USA
US2430129999900010
10241A89999999R
100 CUMBERLAND VALLEY AVENUE
WAYNESBORO, PA 17268
ROTARY SCREW COMPRESSOR
MODEL NO.
MAX DRIVER SPEED
MAX ALLOWABLE PRESSURE
PART NO.
RPM
PSIG
BARG
ASSEMBLED IN
FROM FOREIGN AND DOMESTIC MATERIALS
SERIAL NO.
41
600
3600
SGXB2 4021
Rotary screw compressor serial numbers are defined by
the following information:
Example: 10240A90000015Z
Plant
Decade Month
Year Global
Additional
seq. no. remarks
1024
0
A
9
0000015 Z
Plant:
1024 = Waynesboro, 1153 = Monterrey
Month:
A = JAN, B = FEB, C = MAR, D = APR, E = MAY, F = JUN,
G = JUL, H = AUG, K = SEP, L = OCT, M = NOV, N = DEC.
Additional Remarks:
R = Remanufactured;
R1 = Rebuild;
R2 = Rebuild Plus;
Z = Deviation from standard configuration.
RWF II
model
Compressor
model
Rotor
diameter
Rotor
Max
speed
Geo. swept volume
drive shaft end
Displacement
4150 rpm
3550 rpm
2950 rpm
mm
L/d
rpm
ft³/ rev (m³/rev)
cfm (m³/h)
cfm (m³/h)
cfm (m³/h)
100
SGC 1913
193
1.35
4,500
0.16653 (0.00472)
-
591 (1,004)
491 (835)
119 SS
691 (1,174)
-
-
134
SGC 1918
1.8
0.22204 (0.00629)
-
788 (1,339)
655 (1,113)
159 SS
921 (1,566)
-
-
177
SGC 2313
233
1.35
4,500
0.29301 (0.00830)
-
1,040 (1,767)
864 (1,469)
209 SS
1,216 (2,066)
-
-
222
SGC 2317
1.7
0.36897 (0.01045)
-
1,310 (2,225)
1,088 (1,849)
264 SS
1,531 (2,602)
-
-
270
SGC 2321
2.1
0.45580 (0.01291)
-
1,618 (2,749)
1,345 (2,285)
316
SGC 2813
283
1.35
4,200
0.52501 (0.01487)
-
1,864 (3,167)
1,549 (2,631)
375 SS
2,179 (3,702)
-
-
399
SGC 2817
1.7
0.66113 (0.01872)
-
2,347 (3,988)
1,950 (3,314)
472 SS
2,744 (4,662)
-
-
480
SGC 2821
2.1
0.79546 (0.02253)
-
2,824 (4,798)
2,347 (3,987)
546
SGC 2824
2.4
0.90402 (0.02560)
-
3,209 (5,453)
2,667 (4,531)
496
SGCH/B 3511
355
1.1
3,600
0.82248 (0.02329)
-
2,920 (4,961)
2,426 (4,122)
676
SGCH/B 3515
1.5
1.12154 (0.03176)
-
3,981 (6,765)
3,309 (5,621)
856
SGCH/B 3519
SGXH/B 3519
1.9
1.42748 (0.04042)
-
5,068 (8,610)
4,211 (7,155)
1080
SGXH 3524
2.4
1.80328 (0.05106)
-
6,402 (10,876)
5,320 (9,038)
852
SGXH 4013
408
1.3
3,600
1.41180 (0.03998)
-
5,012 (8,515)
4,165 (7,076)
1179
SGXH 4018
1.8
1.95481 (0.05535)
-
6,940 (11,790)
5,767 (9,798)
1395
SGXH 4021
2.1
2.31320 (0.06550)
-
8,212 (13,952)
6,824 (11,594)
Note:
SS indicates a super speed model.
Table 1: Geometrical swept volume and displacement