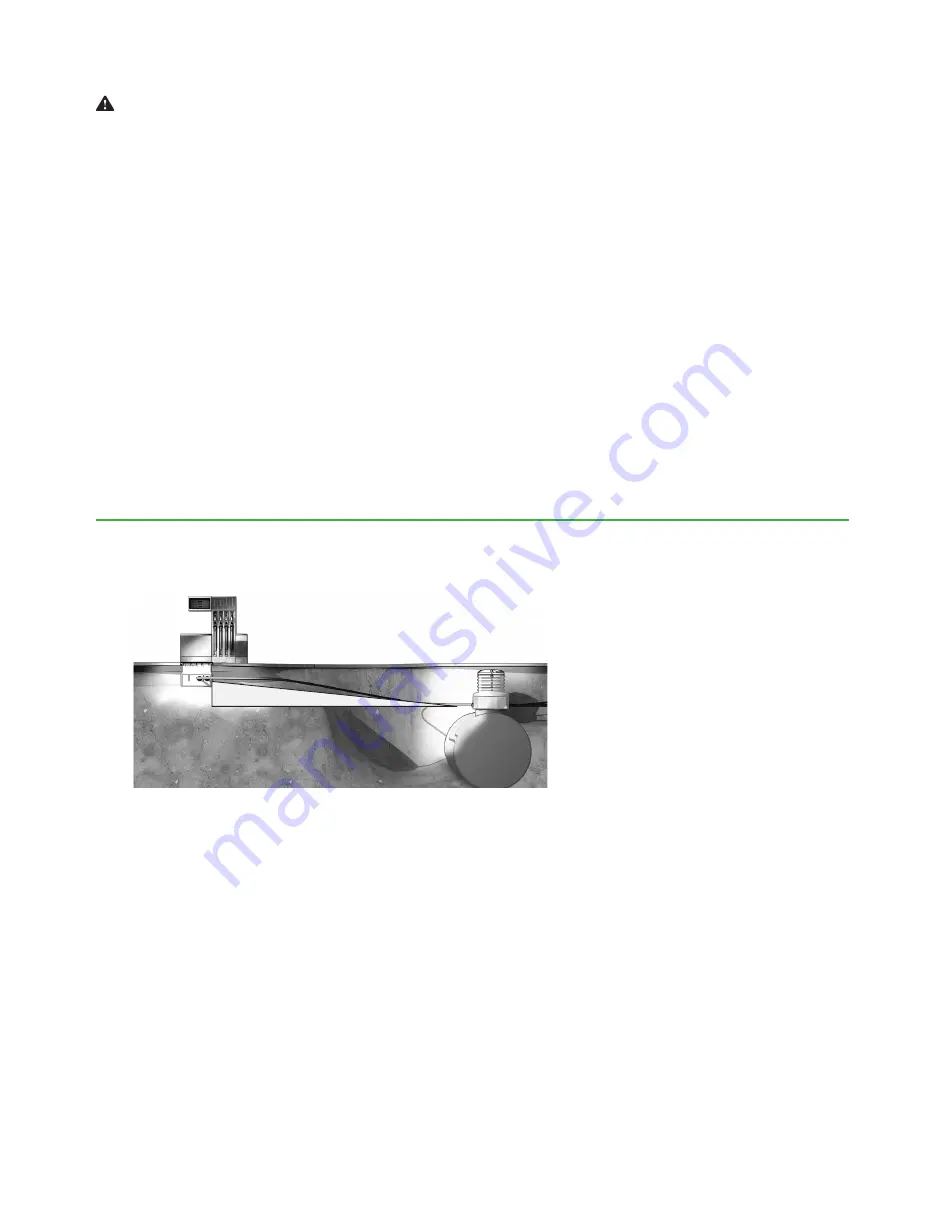
7
WARNING:
The pipe can straighten with considerable force. Take care when releasing pipe from the coil and
secure the straightened pipe.
Let the pipe rest in its uncoiled state for about eight hours. High ambient temperatures can reduce this “layout”
time and low temperatures may increase it. Pipe can be laid in its final position to “relax” before connecting up.
• You need at least three people to uncoil and cut pipe. The coil is taped up in layers to make it easier to
uncoil at manageable intervals.
• The area in which the pipe is uncoiled on site must be clear, safe and free of sharp objects.
• Remove the tape around the tail end on the outer winding and secure this end.
• With the coil in the vertical position, roll the coil out cutting and removing tape as you find it (ensuring to
release only the next turn of pipe in the coil).
• Do not drag the pipe.
• The natural curves from coiling can be used to change pipe direction and bags of sand, pea gravel or stakes
can be used to hold it in place until it is ready for connecting.
• One person should hold the pipe whilst another cuts it to the desired length.
• The cut ends will have a prominent hook that can be partially removed when weight is placed on it (bags of
sand or pea gravel), or use the hook end to your advantage when turning direction into a chamber or pump
sump.
PIPE BURIAL GUIDELINES
Recommended burial depth of UPP
®
pipe is a minimum of 300 mm (12").
• All trenches should be sloped back towards the storage tanks. The fall back (slope) for all pipework to the
tank chambers should be a minimum of 1 m every 100 m or 1/8" per foot.
1:100 Fall-back (Slope) to
tank
• This may vary to meet local requirements. The position of the entry fittings at the furthest dispenser sump
away from the tank chambers may be considerably higher than that of the entry fittings on the closest
dispenser sump.
• Vapor return lines should have a slope of 2 m/100 m (1/4 in/ft) and never less than 1 m/100 m (1/8 in/ft) back
towards the tank farm, unless in-line joints such as elbows are to be used.
• Trench corners should have a radius of 1.5 m (5').
• A recommended 150 mm (6") bed of backfill material should be laid underneath the pipe prior to installation
and there must never be voids under or around the pipe. Acceptable backfill materials are:
•
Well-rounded pea gravel size 3 mm (1/8") to 20 mm (3/4").
•
Crushed rock size 3 mm (1/8") to 16 mm (3/8").
•
Clean washed sand.
•
At installation, backfill cannot be contaminated with petroleum products or other contaminants.
Содержание UPP PIPING
Страница 1: ...UPP PIPING INSTALLATION GUIDE ...
Страница 16: ...408001016 r7 ...