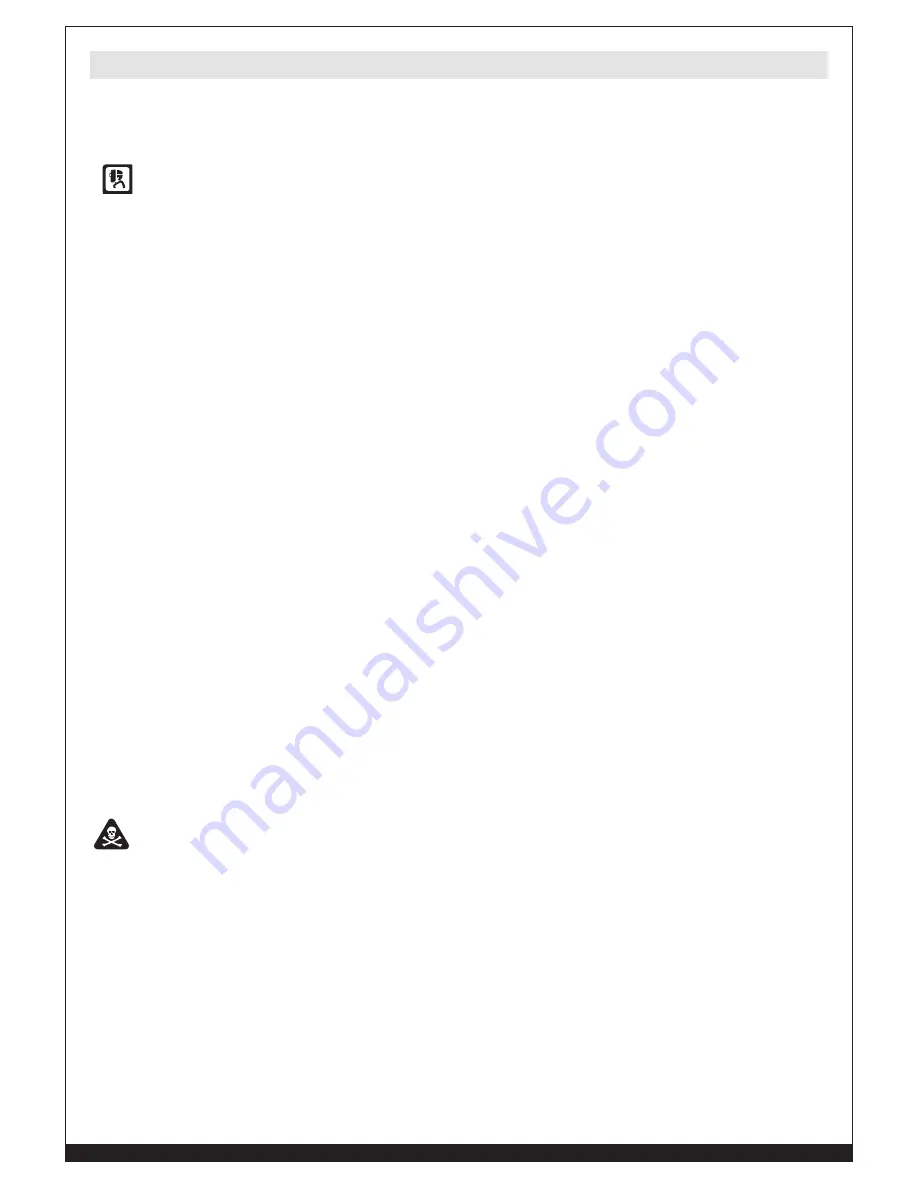
6
WWW.FORNEYIND.COM
Personal Protection
Welding processes of any kind can be dangerous not only to the operator but to any person situated
near the equipment, if safety and operating rules are not strictly observed.
THE WELDING ARC PRODUCES VERY BRIGHT ULTRAVIOLET AND INFRARED
LIGHT. THESE ARC RAYS WILL DAMAGE YOUR EYES AND BURN YOUR SKIN IF
YOU ARE NOT PROPERLY PROTECTED.
To reduce the risk of injury from arc rays, read,
understand, and follow the safety instructions. In addition, make certain that anyone else that
uses this welding equipment, or is a bystander in the welding area understands and follows
these safety instructions as well. Helmets and filter should conform to ANSI Z87.1 stan dards.
• Do not look at an electric arc without proper protection. A welding arc is extremely bright
and intense and, with inadequate or no eye protection, the retina can be burned, leav ing
a permanent dark spot in the field of vision. A shield or helmet with a #10 shade filter lens
(minimum) must be used.
• Do not strike a welding arc until all bystanders and you (the welder) have welding shields
and/or helmets in place.
• Do not wear a cracked or broken helmet and replace any cracked or bro ken filter lenses
immediately.
• Do not allow the uninsulated portion of the wire feed gun to touch the ground clamp or
grounded work to prevent an arc flash from being created on contact.
• Provide bystanders with shields or hel mets fitted with an appropriate shade filter lens.
• Wear protective clothing. The intense light of the welding arc can burn the skin in much
the same way as the sun, even through light-weight clothing. Wear dark clothing of heavy
material. The shirt worn should be long sleeved and the collar kept buttoned to protect chest
and neck.
• Protect against reflected arc rays. Arc rays can be reflected off shiny sur faces such as a glossy
painted surface, aluminum, stainless steel, and glass. It is possible for your eyes to be injured
by reflected arc rays even when wearing a protective helmet or shield. If welding with a
reflective surface behind you, arc rays can bounce off the surface and off the fil ter lens. It can
get inside your helmet or shield and into your eyes. If a reflective background exists in your
welding area, either remove it or cover it with something non-flammable and non-reflective.
Reflective arc rays can also cause skin burn in addition to eye injury.
• Flying sparks can injure. Wear proper safety equipment to protect eyes and face. Shape
tungsten electrode on grinder wearing proper protection and in a safe location. Keep
flammables away and prevent fire from flying sparks.
FUMES, GASSES, AND VAPORS CAN CAUSE DISCOMFORT, ILLNESS, AND
DEATH!
To reduce the risk, read, understand, and follow the safety instructions. In addition,
make certain that anyone else that uses this welding equipment or is a bystander in the welding
area, understands and follows these safety instructions as well.
• Read and understand manufacturers SDS and MSDS.
• Do not weld in an area until it is checked for adequate ventilation as described in ANSI
standard Z49.1. If ventilation is not adequate to exchange all fumes and gasses generated
during the welding process with fresh air, do not weld unless you (the welder) and all
bystanders are wearing air-supplied respirators.
• Do not heat metals coated with, or that contain, materials that produce toxic fumes (such as
galvanized steel), unless the coating is removed. Make certain the area is well ventilated, and
the operator and all bystanders are wearing air-sup plied respirators.
• Do not weld, cut or heat lead, zinc, cad mium, mercury, beryllium, antimony, cobalt,
manganese, selenium, arsenic, copper, silver, barium, chromium, vanadium, nickel, or similar
met als without seeking professional advice and inspection of the ventilation of the welding
Содержание 125 FC
Страница 25: ...25 WWW FORNEYIND COM Wiring Diagram...
Страница 27: ...27 WWW FORNEYIND COM...