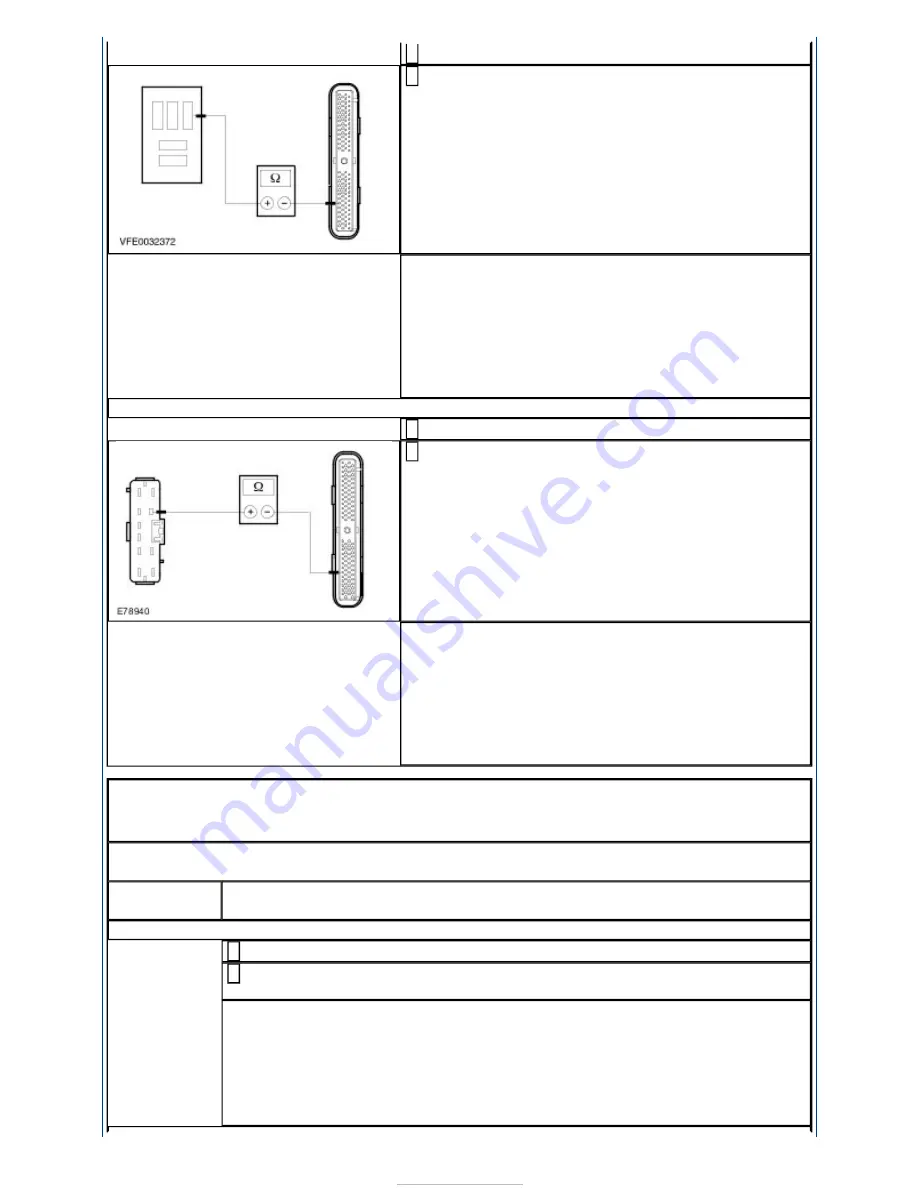
Disconnect PCM C415.
1
Measure the resistance between engine run relay,
socket C1024, pin 1, wiring harness side and PCM,
connector C415, pin 6, circuit 31S-PA19 (BK/GN),
wiring harness side.
2
Is a resistance of less than 2 Ohm registered?
Yes
CHECK the PCM and RENEW as necessary. CHECK
the operation of the system.
No
LOCATE and REPAIR the open circuit between the
engine run relay and the PCM using the Wiring
Diagrams. CHECK the operation of the system.
B25: CHECK THE CIRCUIT BETWEEN THE CJB AND THE PCM FOR CONTINUITY.
Disconnect connector C10 from CJB.
1
Measure the resistance between the CJB,
connector C10, pin 3, circuit 31S-PA19 (BK/GN),
wiring harness side and the PCM, connector C415,
pin 6, circuit 31S-PA19 (BK/GN), wiring harness
side.
2
Is a resistance of less than 2 Ohm registered?
Yes
CHECK the CJB and RENEW as necessary. CHECK
the operation of the system.
No
LOCATE and REPAIR the open circuit between the
CJB and the PCM with the aid of the Wiring
Diagrams. CHECK the operation of the system.
PINPOINT TEST C : BLOWER MOTOR INOPERATIVE WHEN FUEL-FIRED
BOOSTER HEATER SWITCHED ON - VEHICLES WITH PROGRAMMABLE
FUEL-FIRED BOOSTER HEATER
NOTE: Before switching on the programmable fuel-fired booster heater the blower motor
needs to be switched to its lowest setting via the blower switch.
TEST
CONDITIONS
DETAILS/RESULTS/ACTIONS
C1: TEST FUSE FA
Ignition switch in position 0.
1
CHECK Fuse FB (auxiliary fuse box) (vehicles built from 02/2004: fuse
holder 3).
2
Is the fuse OK?
Yes
GO to C2
.
No
RENEW fuse FA (30 A). If the fuse blows again, LOCATE and RECTIFY the
short circuit using the Wiring Diagrams. CHECK the operation of the
system.
Стр
. 17
из
27
06.02.2013
http://127.0.0.1:8888/wsm/js/procedure.do?variantId=941&proc-uid=G218553&guid...
http://vnx.su
Содержание Tourneo Connect 2002
Страница 59: ...Torque Specifications Description Nm lb ft lb in Tie rod end locknut 47 35 http vnx su ...
Страница 79: ...12 Tighten the strut and spring assembly top mount retaining nuts http vnx su ...
Страница 201: ...5 6 7 8 http vnx su ...
Страница 202: ...Installation 1 NOTE Only tighten the nuts and bolt finger tight at this stage 2 Torque 9 Nm http vnx su ...
Страница 203: ...3 2 Torque 50 Nm 3 Torque 23 Nm 4 5 Torque 28 Nm http vnx su ...
Страница 204: ...6 7 8 http vnx su ...
Страница 230: ...12 Install the air intake cover http vnx su ...
Страница 321: ...3 Install the steering gear For additional information refer to Steering Gear in this section http vnx su ...
Страница 407: ...7 Install the cylinder head For additional information refer to Cylinder Head in this section http vnx su ...
Страница 410: ...8 Install the timing belt For additional information refer to Timing Belt in this section http vnx su ...
Страница 442: ...Installation 1 NOTE Install a new valve cover gasket if necessary To install reverse the removal procedure http vnx su ...
Страница 463: ...http vnx su ...
Страница 616: ...5 Fill the engine with engine oil 5 Fill the engine with engine oil http vnx su ...
Страница 625: ...16 General Equipment Hose clamp remover installer 17 http vnx su ...
Страница 626: ...18 19 General Equipment Hose clamp remover installer 20 General Equipment Hose clamp remover installer http vnx su ...
Страница 631: ...11 General Equipment Hose clamp remover installer Torque 23 Nm 12 Torque 18 Nm http vnx su ...
Страница 929: ...http vnx su ...
Страница 1059: ...Vehicles without air conditioning 2 To install reverse the removal procedure http vnx su ...
Страница 1060: ...http vnx su ...
Страница 1062: ...Vehicles without air conditioning 2 To install reverse the removal procedure http vnx su ...
Страница 1063: ...http vnx su ...
Страница 1111: ...http vnx su ...
Страница 1118: ...3 To install reverse the removal procedure http vnx su ...
Страница 1123: ...1 To install reverse the removal procedure http vnx su ...
Страница 1140: ...Description PCM Inertia fuel cut off switch Item 1 2 http vnx su ...
Страница 1170: ...1 Using the special tool remove the HO2S http vnx su ...
Страница 1221: ...6 Torque 35 Nm http vnx su ...
Страница 1223: ...http vnx su ...
Страница 1229: ...All vehicles 3 Lower the vehicle http vnx su ...
Страница 1236: ...33 Remove the transaxle http vnx su ...
Страница 1246: ...8 9 10 http vnx su ...
Страница 1248: ...14 15 16 http vnx su ...
Страница 1252: ...27 28 29 30 Secure to one side http vnx su ...
Страница 1254: ...36 37 38 Special Tool s 303 290A 39 Refer to Lifting 100 02 Jacking and Lifting Description and Operation 40 http vnx su ...
Страница 1256: ...45 WARNING This step requires the aid of another technician General Equipment Transmission jack http vnx su ...
Страница 1272: ...http vnx su ...
Страница 1275: ...special tool and a press http vnx su ...
Страница 1301: ...8 Torque 80 Nm 9 Lower the Vehicle 10 Special Tool s 303 290A 11 Torque 80 Nm http vnx su ...
Страница 1308: ...39 40 41 http vnx su ...
Страница 1313: ...Gearshift cable mounting point on the selector lever shaft Selector shaft lever 12 13 http vnx su ...
Страница 1328: ...11 Lower the vehicle http vnx su ...
Страница 1370: ...detector 5 Repair the detected leak Test the system for normal operation http vnx su ...
Страница 1395: ...Description Muffler Description Item 1 Item Part Number Part Number http vnx su ...
Страница 1403: ...Description Muffler Description Item 1 Item Part Number Part Number http vnx su ...
Страница 1416: ...1 Install the fuel filter and the fuel filter support bracket until an audible click is heard http vnx su ...
Страница 1434: ...http vnx su ...
Страница 1457: ...Installation 1 To install reverse the removal procedure http vnx su ...
Страница 1510: ...Installation 1 NOTE Note the direction of flow of the pollen filter Refit the components in reverse order http vnx su ...
Страница 1517: ...Installation 1 Install the components in the reverse order http vnx su ...
Страница 1519: ...Left hand drive vehicles 6 7 8 Torque 9 Nm http vnx su ...
Страница 1520: ...All vehicles 9 10 11 http vnx su ...
Страница 1521: ...12 13 http vnx su ...
Страница 1522: ...Installation 14 1 To install reverse the removal procedure http vnx su ...
Страница 1537: ...8 9 General Equipment Electric drill General Equipment 4 mm drill bit General Equipment Blind rivet gun 10 11 12 http vnx su ...
Страница 1540: ...24 Torque 25 Nm 25 26 27 http vnx su ...
Страница 1542: ...35 36 Torque 28 Nm 37 Torque 25 Nm 38 http vnx su ...
Страница 1610: ...Installation 1 Install the components in the reverse order http vnx su ...
Страница 1630: ...To install reverse the removal procedure http vnx su ...
Страница 1634: ...Install the components in the reverse order http vnx su ...
Страница 1652: ...Installation 1 To install reverse the removal procedure http vnx su ...
Страница 1655: ...Refit the components in reverse order http vnx su ...
Страница 1657: ...Installation 1 To install reverse the removal procedure http vnx su ...
Страница 1791: ...18 Torque 25 Nm 19 20 http vnx su ...
Страница 1792: ...21 22 Torque 25 Nm 23 On both sides http vnx su ...
Страница 1794: ...28 Torque 10 Nm 29 30 Torque 28 Nm 31 Torque 25 Nm http vnx su ...
Страница 1795: ...Installation 32 1 To install reverse the removal procedure http vnx su ...
Страница 1798: ...Installation 1 To install reverse the removal procedure http vnx su ...
Страница 1804: ...18 Torque 25 Nm 19 20 http vnx su ...
Страница 1805: ...21 22 Torque 25 Nm 23 On both sides http vnx su ...
Страница 1807: ...28 Torque 10 Nm 29 30 Torque 28 Nm 31 Torque 25 Nm http vnx su ...
Страница 1809: ...Installation 1 To install reverse the removal procedure http vnx su ...
Страница 1938: ...16 Template for LHD vehicles left hand headlamp 1 Alignment edge on the headlamp lens 2 Reference point http vnx su ...
Страница 1939: ...17 Template for RHD vehicles right hand headlamp 1 Alignment edge on the headlamp lens 2 Reference point http vnx su ...
Страница 1940: ...18 Template for RHD vehicles left hand headlamp 1 Alignment edge on the headlamp lens 2 Reference point http vnx su ...
Страница 1941: ...http vnx su ...
Страница 1943: ...http vnx su ...
Страница 2084: ...20 21 22 23 24 25 26 http vnx su ...
Страница 2085: ...27 28 29 30 31 32 33 http vnx su ...
Страница 2086: ...34 35 36 37 38 39 40 http vnx su ...
Страница 2087: ...41 42 43 44 45 46 47 http vnx su ...
Страница 2090: ...64 65 66 http vnx su ...
Страница 2091: ...67 On both sides 68 On both sides 69 70 http vnx su ...
Страница 2096: ...17 18 Torque 25 Nm 19 20 21 http vnx su ...
Страница 2100: ...42 43 General Equipment Draw cord 44 General Equipment Draw cord 45 General Equipment Draw cord http vnx su ...
Страница 2101: ...46 On both sides 47 On both sides 48 49 http vnx su ...
Страница 2106: ...16 17 18 19 20 http vnx su ...
Страница 2107: ...21 22 23 24 25 http vnx su ...
Страница 2108: ...26 27 28 29 30 http vnx su ...
Страница 2109: ...31 32 33 34 35 http vnx su ...
Страница 2110: ...36 37 38 39 40 http vnx su ...
Страница 2111: ...41 42 43 44 45 http vnx su ...
Страница 2112: ...46 47 48 On both sides 49 On both sides 50 On both sides http vnx su ...
Страница 2113: ...51 52 On both sides 53 On both sides 54 Remove the dashboard together with the dashboard crossmember 55 56 http vnx su ...
Страница 2114: ...57 58 59 http vnx su ...
Страница 2116: ...2 Follow the disassembly procedure in reverse order http vnx su ...
Страница 2119: ...16 Torque 8 Nm 17 18 Torque 25 Nm 19 20 http vnx su ...
Страница 2121: ...26 27 28 On both sides 29 http vnx su ...
Страница 2123: ...36 Torque 10 Nm 37 38 Torque 28 Nm 39 Torque 25 Nm 40 http vnx su ...
Страница 2124: ...41 42 43 http vnx su ...
Страница 2125: ...Installation 44 1 To install reverse the removal procedure http vnx su ...
Страница 2127: ...All Vehicles 10 11 12 13 14 15 1 Torque 22 Nm http vnx su ...
Страница 2128: ...16 17 18 19 20 Torque 8 Nm http vnx su ...
Страница 2131: ...34 35 36 37 38 Lower the vehicle 39 40 Torque 5 Nm http vnx su ...
Страница 2132: ...41 42 43 44 http vnx su ...
Страница 2138: ...On Combi unlock all the doors 4 http vnx su ...
Страница 2148: ...Installation 1 To install reverse the removal procedure http vnx su ...
Страница 2154: ...Installation 1 To install reverse the removal procedure http vnx su ...
Страница 2166: ...Reinforcements of the seat mounting points 2 http vnx su ...
Страница 2173: ...Installation 17 Lower the vehicle 18 Remove the fender 1 To install reverse the removal procedure http vnx su ...
Страница 2175: ...Installation 10 Remove the radiator grille opening panel 1 To install reverse the removal procedure http vnx su ...
Страница 2177: ...7 1 Torque 7 Nm 2 Torque 25 Nm 8 Torque 25 Nm 9 1 Torque 7 Nm 2 Torque 25 Nm 10 Torque 25 Nm http vnx su ...
Страница 2178: ...11 Torque 25 Nm 12 On both sides Torque 7 Nm 13 Torque 11 Nm 14 1 Torque 25 Nm 2 Torque 7 Nm 15 http vnx su ...
Страница 2179: ...Installation 1 To install reverse the removal procedure http vnx su ...
Страница 2189: ...Installation 1 To install reverse the removal procedure http vnx su ...
Страница 2191: ...Installation 1 To install reverse the removal procedure http vnx su ...
Страница 2201: ...All vehicles 4 On both sides 5 6 http vnx su ...
Страница 2203: ...Installation 1 To install reverse the removal procedure http vnx su ...
Страница 2205: ...6 1 On both sides Torque 40 Nm 2 On both sides Torque 35 Nm 7 http vnx su ...
Страница 2206: ...Installation 1 To install reverse the removal procedure http vnx su ...
Страница 2208: ...Installation 1 To install reverse the removal procedure http vnx su ...
Страница 2229: ...HC11 GN WH TEST the system for normal operation http vnx su ...
Страница 2231: ...Installation 1 To install reverse the removal procedure http vnx su ...
Страница 2239: ...Installation 5 6 1 General Equipment hog ring plier 2 To install reverse the removal procedure http vnx su ...
Страница 2246: ...1 To install reverse the removal procedure http vnx su ...
Страница 2248: ...6 7 8 9 http vnx su ...
Страница 2249: ...Installation 10 CAUTION Make sure that the component is not bent 1 To install reverse the removal procedure http vnx su ...
Страница 2255: ...6 7 8 2 Torque 25 Nm 9 NOTE This step requires considerable force Remove the armrest from the tapered shaft 10 http vnx su ...
Страница 2271: ...7 8 9 Torque 45 Nm 10 Torque 45 Nm 11 http vnx su ...
Страница 2275: ...http vnx su ...
Страница 2277: ...Assembly 6 Torque 35 Nm 7 To install reverse the removal procedure http vnx su ...
Страница 2293: ...for normal operation No REPAIR circuit 30 DA1 RD TEST the system for normal operation http vnx su ...
Страница 2297: ...http vnx su ...
Страница 2299: ...panel http vnx su ...
Страница 2307: ...http vnx su ...
Страница 2318: ...http vnx su ...
Страница 2347: ...16 Torque 8 Nm 17 18 Torque 25 Nm 19 20 http vnx su ...
Страница 2350: ...All vehicles 32 33 34 Torque 10 Nm 35 Torque 10 Nm http vnx su ...
Страница 2351: ...36 37 Torque 28 Nm 38 Torque 25 Nm 39 1 Torque 8 Nm 2 Torque 8 Nm http vnx su ...
Страница 2352: ...Installation 40 41 Torque 25 Nm 1 To install reverse the removal procedure http vnx su ...
Страница 2354: ...2 Remove the power socket if equipped http vnx su ...
Страница 2356: ...Installation 4 1 To install reverse the removal procedure http vnx su ...
Страница 2358: ...Installation 1 To install reverse the removal procedure http vnx su ...
Страница 2360: ...Installation 5 Torque 17 Nm 1 To install reverse the removal procedure http vnx su ...
Страница 2375: ...Hood lock and latch retaining bolt Hood latch Hood lock 2 To install reverse the removal procedure 12 13 14 http vnx su ...
Страница 2391: ...Installation 1 To install reverse the removal procedure http vnx su ...
Страница 2393: ...cable retaining tangs and detach the sliding door remote control cable http vnx su ...
Страница 2467: ...http vnx su ...
Страница 2479: ...Installation 1 To install reverse the removal procedure http vnx su ...
Страница 2484: ...6 On both sides 7 1 Torque 12 Nm 8 On both sides http vnx su ...
Страница 2485: ...Installation 9 1 To install reverse the removal procedure http vnx su ...
Страница 2487: ...7 8 On both sides 9 http vnx su ...
Страница 2623: ...12 Install the instrument panel lower panel to the instrument panel 1 Secure the clips 2 Install the screws http vnx su ...
Страница 2636: ...Vehicles without navigation system All vehicles 7 8 1 Torque 8 Nm 2 Torque 8 Nm 9 http vnx su ...
Страница 2637: ...Installation 1 To install reverse the removal procedure http vnx su ...
Страница 2731: ...Overview of parts side panels vehicles with long wheel base LWB http vnx su ...
Страница 2732: ...Overview of parts load space floor and rear side member Description ItemPart Number http vnx su ...
Страница 2733: ...Load space floor all models Rear side member all models 1 2 http vnx su ...
Страница 2737: ...http vnx su ...
Страница 2744: ...http vnx su ...
Страница 2746: ...http vnx su ...
Страница 2749: ...3 Side member Resistance spot weld 4 Side member Resistance spot weld http vnx su ...
Страница 2752: ...5 Side member with fender apron panel 1 Resistance spot weld 2 Puddle weld http vnx su ...
Страница 2758: ...http vnx su ...
Страница 2765: ...http vnx su ...
Страница 2767: ...2 Back panel 1 Puddle weld 2 Resistance spot weld 3 Back panel 1 Resistance spot weld 2 Puddle weld http vnx su ...
Страница 2770: ...Side panel 1 Resistance spot welding 2 Puddle weld http vnx su ...
Страница 2772: ...Resistance spot weld 2 Rear floor panel 1 Continuous MIG weld butt weld 2 Resistance spot weld http vnx su ...
Страница 2780: ...http vnx su ...
Страница 2792: ...2 Valid for three and five door vehicles http vnx su ...
Страница 2793: ...3 Valid for three and five door vehicles http vnx su ...
Страница 2794: ...4 Valid for four door vehicles http vnx su ...
Страница 2795: ...5 Valid for four door vehicles http vnx su ...
Страница 2796: ...6 Valid for estate vehicle http vnx su ...
Страница 2797: ...7 Valid for estate vehicle http vnx su ...