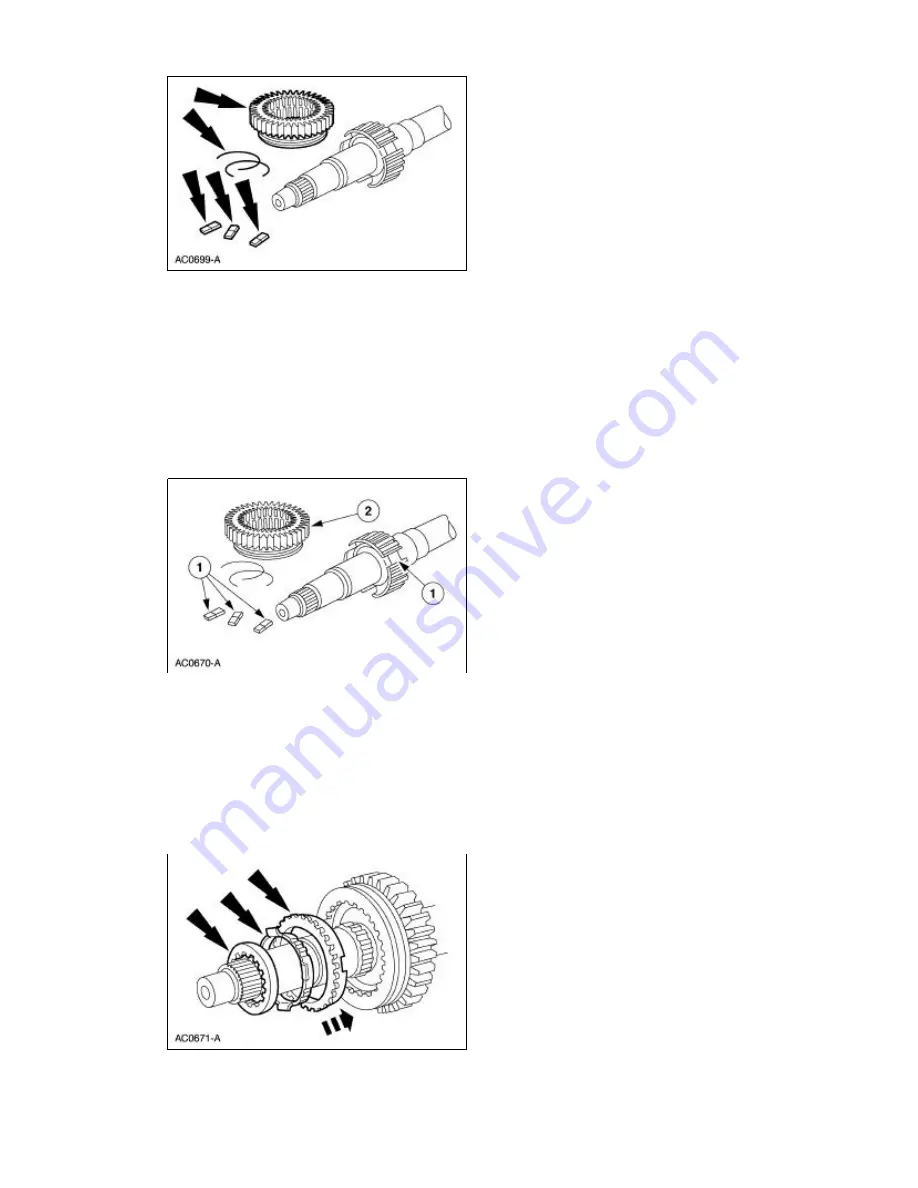
Assembly
1. Soak the blocking rings in transmission fluid for ten minutes.
Use MERCON® Multi-Purpose ATF Transmission Fluid XT-2-QDX or equivalent.
2. Assemble the first and second synchronizer.
1. Install the synchronizer hub insert springs and the synchronizer inserts into the
synchronizer hub.
2. Install the sliding sleeve onto the hub.
3.
NOTE:
If not done so previously, soak the blocking ring in MERCON® Multi-Purpose ATF
Transmission Fluid XT-2-QDX or equivalent for ten minutes.
NOTE:
Align the slots in the synchronizer blocking ring with the tabs in the first and second
speed synchronizer.
Install the second speed synchronizer blocking ring and the inner and outer cones as an
assembly.
4. Install the second speed synchronizer thrust washer.
5. Using the special tool, install the output shaft bearing snap ring.
. 5
10
2003 Mustang Workshop Manual
18.11.2011
file:///C:/Ford/2000-2004/tsocache/SHEF_2308/S3B~us~en~...
Содержание 2003 Mustang
Страница 18: ...To lift the rear or either side of the rear end position the floor jack under the rear lift points ...
Страница 21: ......
Страница 32: ......
Страница 47: ......
Страница 49: ......
Страница 50: ......
Страница 117: ......
Страница 120: ......
Страница 123: ......
Страница 125: ......
Страница 130: ...Rear Ride Height Measurement GT and Base Item Description 1 Ride height B A 2 Measurement A 3 Measurement B ...
Страница 133: ......
Страница 139: ......
Страница 144: ......
Страница 146: ......
Страница 148: ...7 Tighten the nuts 8 Install the clamps 9 Recheck the toe settings Follow the manufacturer s instructions ...
Страница 149: ......
Страница 151: ...4 Recheck the toe settings Follow the manufacturer s instructions ...
Страница 154: ......
Страница 156: ...Installation 1 NOTE Use a new wheel hub retainer and hub cap grease seal To install reverse the removal procedure ...
Страница 161: ......
Страница 163: ......
Страница 166: ......
Страница 170: ...Installation 1 To install reverse the removal procedure ...
Страница 171: ...2 Check wheel alignment Adjust if necessary For additional information refer to Section 204 00 ...
Страница 174: ...14 Remove the sleeve and the bushing Installation 1 To install reverse the removal procedure ...
Страница 175: ......
Страница 176: ......
Страница 184: ......
Страница 186: ...Axle shaft to hub retainer 325 240 Wheel nuts 129 95 ...
Страница 194: ......
Страница 200: ......
Страница 205: ......
Страница 210: ......
Страница 213: ...2 Check wheel alignment Adjust as necessary For additional information refer to Section 204 00 ...
Страница 215: ......
Страница 224: ......
Страница 227: ...2 Check wheel alignment Adjust as necessary For additional information refer to Section 204 00 ...
Страница 228: ......
Страница 233: ...11 Connect the anti lock sensor wire 12 Lower the vehicle ...
Страница 242: ......
Страница 245: ......
Страница 248: ...5 Install the wheel and tire assembly For additional information refer to Section 204 04 6 Lower the vehicle ...
Страница 250: ......
Страница 252: ......
Страница 257: ......
Страница 259: ......
Страница 262: ......
Страница 264: ......
Страница 292: ......
Страница 297: ......
Страница 301: ......
Страница 314: ......
Страница 317: ......
Страница 325: ......
Страница 353: ...24 Lower the vehicle ...
Страница 358: ......
Страница 364: ...10 Install the differential case For additional information refer to Differential Case in this section ...
Страница 373: ......
Страница 376: ......
Страница 379: ......
Страница 394: ......
Страница 407: ...24 Lower the vehicle ...
Страница 413: ......
Страница 419: ...section ...
Страница 437: ......
Страница 458: ......
Страница 493: ......
Страница 509: ......
Страница 552: ......
Страница 556: ...Installation 1 Follow the removal procedure in reverse order ...
Страница 563: ......
Страница 565: ......
Страница 567: ......
Страница 571: ......
Страница 576: ......
Страница 579: ......
Страница 582: ......
Страница 586: ...7 Recheck the master cylinder fluid level ...
Страница 591: ......
Страница 598: ......
Страница 601: ......
Страница 603: ......
Страница 606: ......
Страница 609: ......
Страница 613: ......
Страница 619: ...6 Remove the brake pedal and bracket Installation 1 To install reverse the removal procedure ...
Страница 620: ......
Страница 622: ......
Страница 625: ......
Страница 627: ......
Страница 629: ......
Страница 634: ......
Страница 636: ......
Страница 639: ......
Страница 644: ......
Страница 665: ...3 Install the rear axle shaft bearing refer to Section 205 02A ...
Страница 668: ......
Страница 670: ......
Страница 672: ...Installation 1 To install reverse the removal procedure ...
Страница 673: ......
Страница 697: ......
Страница 700: ...3 Install the rear axle shaft bearing refer to Section 205 02A ...
Страница 703: ......
Страница 705: ......
Страница 707: ...Installation 1 To install reverse the removal procedure ...
Страница 708: ......
Страница 712: ...5 To install reverse the removal procedure ...
Страница 714: ...Relief pressure 8 274 9 510 kPa 1 200 1 380 psi ...
Страница 717: ......
Страница 728: ......
Страница 740: ......
Страница 742: ......
Страница 748: ......
Страница 750: ......
Страница 753: ......
Страница 756: ......
Страница 758: ...2 Install the drive belt For additional information refer to Section 303 05 ...
Страница 760: ...2 Install the drive belt For additional information refer to Section 303 05 3 Lower the vehicle ...
Страница 762: ......
Страница 764: ...00 ...
Страница 768: ...2 Fill and leak check the power steering system For additional information refer to Section 211 00 ...
Страница 774: ......
Страница 779: ......
Страница 787: ......
Страница 796: ......
Страница 798: ...5 To install reverse the removal procedure ...
Страница 800: ......
Страница 818: ......
Страница 828: ......
Страница 833: ......
Страница 862: ......
Страница 864: ......
Страница 866: ......
Страница 868: ......
Страница 872: ......
Страница 876: ......
Страница 878: ......
Страница 880: ......
Страница 885: ......
Страница 887: ......
Страница 891: ......
Страница 893: ......
Страница 895: ......
Страница 904: ......
Страница 907: ......
Страница 909: ......
Страница 912: ......
Страница 920: ......
Страница 934: ......
Страница 949: ......
Страница 969: ...5 To install reverse the removal procedure ...
Страница 972: ......
Страница 988: ......
Страница 990: ......
Страница 995: ......
Страница 998: ......
Страница 1001: ...5 Install the timing chain For additional information refer to Timing Chain in this section ...
Страница 1006: ......
Страница 1008: ...Installation 1 NOTE Install a new gasket NOTE Tighten the nuts in the sequence shown To install reverse the removal procedure ...
Страница 1009: ......
Страница 1012: ......
Страница 1018: ......
Страница 1025: ......
Страница 1033: ...4 Install the transmission lower bolts 5 Install the oil pan drain plug 6 Raise the front subframe into position ...
Страница 1034: ...7 Tighten the two bolts 8 Install the two bolts 9 Install the four subframe lower bolts 10 Remove the safety stand ...
Страница 1040: ......
Страница 1042: ......
Страница 1046: ...5 Install the flywheel or the flexplate For additional information refer to Flexplate in this section ...
Страница 1052: ...5 Lower the vehicle 6 Lower the engine 7 Raise the vehicle 8 Install the RH engine mount nut 9 Install the LH engine mount nut ...
Страница 1054: ......
Страница 1065: ...46 Mount the engine on a suitable engine stand ...
Страница 1086: ......
Страница 1091: ......
Страница 1106: ...44 Tighten the oil pan bolts in the sequence shown 45 Install the RH valve cover ...
Страница 1119: ......
Страница 1135: ......
Страница 1136: ...DESCRIPTION AND OPERATION Engine SECTION 303 01B Engine 4 6L 2V 2003 Mustang Workshop Manual ...
Страница 1137: ......
Страница 1144: ......
Страница 1157: ...7 Install the generator 8 Connect the electrical connector 9 Connect the battery lead 10 Install the generator support brace ...
Страница 1165: ...40 Refill the engine cooling system For additional information refer to Section 303 03A or Section 303 03B ...
Страница 1168: ......
Страница 1171: ......
Страница 1174: ...4 Lower the vehicle 5 Install the drive belt For additional information refer to Section 303 05 ...
Страница 1177: ......
Страница 1186: ...20 Fill the crankcase with clean engine oil ...
Страница 1189: ...7 Remove the bolts and the LH timing chain tensioner 8 Remove the bolts and the RH timing chain tensioner ...
Страница 1196: ...14 Position the RH timing chain tensioner and install the bolts 15 Position the LH timing chain tensioner and install the bolts ...
Страница 1199: ......
Страница 1205: ......
Страница 1207: ......
Страница 1210: ......
Страница 1213: ...11 To install reverse the removal procedure 1 Tighten the exhaust manifold nuts in the sequence shown ...
Страница 1216: ...Tighten to 14Nm 10 lb ft Tighten an additional 180 ...
Страница 1218: ......
Страница 1227: ...17 Fill the engine crankcase with clean engine oil ...
Страница 1229: ......
Страница 1231: ......
Страница 1234: ...3 Install the flywheel For additional information refer to Flywheel in this section ...
Страница 1237: ......
Страница 1240: ......
Страница 1261: ......
Страница 1266: ...21 Remove the bolt and the body ground 22 Separate the fuse link 23 Disconnect the connector 24 Disconnect the ground connector ...
Страница 1297: ......
Страница 1301: ......
Страница 1304: ......
Страница 1339: ...99 Using the special tools install the crankshaft rear oil slinger 100 Install the separator plate 101 Install the flywheel ...
Страница 1340: ......
Страница 1365: ...74 Install the engine For additional information refer to Engine in the Installation portion of this section ...
Страница 1372: ...25 Connect the connector 26 Install the battery leads 27 Position the access cover 28 Connect the ground connector ...
Страница 1373: ...29 Connect the connector 30 Connect the fuse link 31 Install and tighten the body ground 32 Connect the power steering line ...
Страница 1378: ......
Страница 1384: ......
Страница 1412: ...14 To install reverse the removal procedure Tighten the valve cover bolts in the sequence shown ...
Страница 1413: ......
Страница 1419: ......
Страница 1429: ......
Страница 1444: ......
Страница 1451: ......
Страница 1454: ......
Страница 1463: ......
Страница 1466: ......
Страница 1469: ......
Страница 1471: ......
Страница 1479: ...9 Raise the front sub frame into position 10 Install the two bolts 11 Install the two bolts 12 Install the four bolts ...
Страница 1482: ......
Страница 1486: ...3 Install the flywheel For additional information refer to Flywheel in this section ...
Страница 1489: ......
Страница 1492: ......
Страница 1509: ......
Страница 1530: ...76 Remove and discard the bolts 77 Remove the main bearing caps and the crankshaft lower main bearings from the cylinder block ...
Страница 1531: ...78 Remove the crankshaft the crankshaft thrust washer and the crankshaft upper main bearings from the cylinder block ...
Страница 1532: ......
Страница 1543: ......
Страница 1546: ...4 Install the piston pin retaining clips in the piston ...
Страница 1549: ......
Страница 1584: ...105 Install the flywheel and the bolts Tighten the bolts in the sequence shown ...
Страница 1601: ......
Страница 1654: ......
Страница 1657: ......
Страница 1678: ......
Страница 1685: ......
Страница 1690: ......
Страница 1693: ......
Страница 1702: ......
Страница 1705: ......
Страница 1709: ......
Страница 1717: ...9 Raise the front sub frame into position 10 Install the two bolts 11 Install the two bolts 12 Install the four bolts ...
Страница 1720: ......
Страница 1722: ......
Страница 1755: ......
Страница 1776: ......
Страница 1787: ......
Страница 1790: ...4 Install the piston pin retaining clips in the piston ...
Страница 1820: ......
Страница 1864: ......
Страница 1867: ......
Страница 1869: ...5 To install reverse the removal procedure ...
Страница 1874: ......
Страница 1879: ......
Страница 1886: ......
Страница 1890: ......
Страница 1892: ...7 Remove the fan motor and shroud 8 To install reverse the removal procedure ...
Страница 1895: ......
Страница 1897: ......
Страница 1906: ......
Страница 1910: ......
Страница 1912: ...7 To install reverse the removal procedure ...
Страница 1914: ......
Страница 1916: ......
Страница 1919: ......
Страница 1923: ...5 To install reverse the removal procedure ...
Страница 1925: ......
Страница 1932: ......
Страница 1940: ...Installation 1 To install reverse the removal procedure ...
Страница 1942: ...3 Install the fuel supply manifold ...
Страница 1956: ......
Страница 1964: ...17 Connect the air cleaner outlet tube 18 Connect the battery ground cable ...
Страница 1967: ......
Страница 1970: ...5 NOTE Install a new throttle body gasket To install reverse the removal procedure ...
Страница 1981: ......
Страница 1983: ......
Страница 1990: ...Installation 1 NOTE Install a new throttle body gasket To install reverse the removal procedure ...
Страница 1992: ......
Страница 2006: ......
Страница 2009: ...7 6B209 Drive belt tensioner 8 19A216 Belt idler pulley 9 19A216 Belt idler pulley ...
Страница 2012: ......
Страница 2016: ......
Страница 2021: ......
Страница 2025: ......
Страница 2027: ......
Страница 2031: ......
Страница 2033: ......
Страница 2036: ......
Страница 2047: ......
Страница 2049: ......
Страница 2051: ......
Страница 2053: ...6 Remove the bolts and the starter motor Installation 1 To install reverse the removal procedure ...
Страница 2056: ......
Страница 2059: ......
Страница 2069: ......
Страница 2072: ......
Страница 2075: ......
Страница 2079: ...2 To install reverse the removal procedure ...
Страница 2082: ......
Страница 2088: ...6 To install reverse the removal procedure ...
Страница 2092: ......
Страница 2095: ......
Страница 2101: ......
Страница 2103: ...5 Remove the exhaust manifold to EGR valve tube 6 To install reverse the removal procedure ...
Страница 2106: ...1 To install reverse the removal procedure ...
Страница 2110: ......
Страница 2114: ......
Страница 2118: ......
Страница 2120: ...5 To install reverse the removal procedure ...
Страница 2122: ......
Страница 2124: ...5 To install reverse the removal procedure ...
Страница 2126: ......
Страница 2128: ......
Страница 2131: ......
Страница 2133: ......
Страница 2175: ......
Страница 2178: ......
Страница 2187: ...information refer to Evaporative Emission Repair Verification Drive Cycle in this section ...
Страница 2193: ......
Страница 2196: ......
Страница 2198: ......
Страница 2201: ......
Страница 2204: ......
Страница 2211: ......
Страница 2213: ......
Страница 2215: ......
Страница 2217: ......
Страница 2219: ......
Страница 2221: ......
Страница 2223: ......
Страница 2225: ......
Страница 2227: ......
Страница 2229: ......
Страница 2231: ......
Страница 2233: ......
Страница 2235: ...Installation 1 To install reverse the removal procedure ...
Страница 2237: ......
Страница 2240: ......
Страница 2242: ......
Страница 2244: ......
Страница 2246: ...5 To install reverse the removal procedure ...
Страница 2248: ......
Страница 2257: ......
Страница 2263: ...Transmission linkage 23 17 Shift cable bracket 14 10 Transmission test plate bolts 10 89 ...
Страница 2281: ......
Страница 2283: ......
Страница 2285: ...4 Impeller part of 7902 5 Fluid motion 6 Transmission input rotation 7 Input shaft 8 Engine rotation ...
Страница 2296: ......
Страница 2300: ...engine control ...
Страница 2302: ......
Страница 2311: ......
Страница 2315: ......
Страница 2317: ......
Страница 2320: ...Oxygen Sensor Monitor Mode ...
Страница 2329: ......
Страница 2339: ...Resistance Continuity Test Voltage Test PARK NEUTRAL Reversing Lamp and Optional Circuits ...
Страница 2365: ......
Страница 2377: ......
Страница 2379: ......
Страница 2410: ......
Страница 2418: ......
Страница 2425: ......
Страница 2431: ...8 Install the transmission filter and pan For additional information refer to Fluid Pan Gasket and Filter in this section ...
Страница 2432: ......
Страница 2450: ......
Страница 2455: ......
Страница 2459: ...2 Compress the accumulator and install the accumulator piston retaining ring ...
Страница 2461: ...2 Install the main control valve body For additional information refer to Main Control Valve Body in this section ...
Страница 2463: ......
Страница 2468: ...19 Remove the bolts 20 Remove the bolts 21 Remove the bolts 22 Remove the bolt 23 Remove the bolts ...
Страница 2470: ......
Страница 2486: ...51 Inspect and if necessary use the special tools to remove the rear case bushing ...
Страница 2494: ...3 Install the bolt ...
Страница 2501: ...10 Assemble the front pump 1 Position the pump support to the pump body assembly 2 Install the bolts ...
Страница 2503: ......
Страница 2521: ......
Страница 2523: ...3 To assemble reverse the disassembly procedure ...
Страница 2525: ...1 The forward clutch sun gear and reverse sun gear assembly are assembled as part of the transmission assembly procedure ...
Страница 2536: ......
Страница 2539: ......
Страница 2543: ......
Страница 2545: ......
Страница 2549: ...If the torque converter fails the lockup test torque install a new or remanufactured torque converter ...
Страница 2551: ......
Страница 2576: ......
Страница 2578: ...4 Install the bolts 5 Install the bolt 6 Install the bolts 7 Install the bolts ...
Страница 2579: ...8 Install the bolts 9 Reconnect the connectors 10 Connect the transmission fluid cooler tubes 11 Install the shift cable ...
Страница 2586: ......
Страница 2588: ......
Страница 2591: ......
Страница 2599: ......
Страница 2601: ......
Страница 2606: ......
Страница 2609: ......
Страница 2613: ......
Страница 2616: ...Installation 1 To install reverse the removal procedure ...
Страница 2619: ......
Страница 2621: ......
Страница 2624: ...Installation 1 To install reverse the removal procedure ...
Страница 2644: ...No INSPECT the crankshaft end play REFER to Section 303 01A or Section 303 01B ...
Страница 2647: ......
Страница 2649: ......
Страница 2655: ......
Страница 2657: ......
Страница 2659: ...DIAGNOSIS AND TESTING Clutch Refer to Section 308 00 SECTION 308 01 Clutch 2003 Mustang Workshop Manual ...
Страница 2662: ......
Страница 2666: ......
Страница 2668: ......
Страница 2670: ......
Страница 2672: ......
Страница 2675: ...DIAGNOSIS AND TESTING Clutch Controls Refer to Section 308 00 SECTION 308 02 Clutch Controls 2003 Mustang Workshop Manual ...
Страница 2680: ......
Страница 2681: ......
Страница 2685: ......
Страница 2686: ......
Страница 2699: ......
Страница 2701: ......
Страница 2706: ...22 Remove the bolts 23 Lower the transmission and remove the five bolts ...
Страница 2707: ......
Страница 2718: ......
Страница 2722: ...NOTE The flat on the main shift control shaft must face upward Install the pin ...
Страница 2725: ......
Страница 2735: ......
Страница 2754: ......
Страница 2757: ...Crossmember to transmission support bolt 58 43 Driveshaft flange to pinion flange bolt 112 83 ...
Страница 2768: ......
Страница 2773: ......
Страница 2775: ......
Страница 2780: ...21 Lower the transmission and remove the five bolts ...
Страница 2794: ...45 Remove the rear countershaft bearing 46 Remove the rear countershaft bearing cup and the rear output shaft bearing cup ...
Страница 2795: ......
Страница 2798: ......
Страница 2812: ...25 Install the third gear bearing Apply petroleum jelly to the bearing 26 Install third gear ...
Страница 2814: ...29 Install a new retaining ring ...
Страница 2815: ......
Страница 2817: ......
Страница 2819: ......
Страница 2821: ......
Страница 2823: ......
Страница 2830: ...19 Remove the countershaft 20 Remove the mainshaft ...
Страница 2834: ...30 Install the lock pins 31 Install the lock plate ...
Страница 2850: ...5 Install the filler plug ...
Страница 2868: ......
Страница 2872: ......
Страница 2880: ...5 Install a new snap ring 6 Install the second gear needle bearing Apply petroleum jelly to the bearing 7 Install second gear ...
Страница 2884: ......
Страница 2892: ......
Страница 2894: ......
Страница 2897: ......
Страница 2907: ......
Страница 2912: ...11 Remove the bolts and the transmission case 12 Remove the countershaft ...
Страница 2913: ...13 Remove the mainshaft 14 Remove the input shaft ...
Страница 2925: ......
Страница 2930: ...18 Install the gearshift lever knob ...
Страница 2934: ......
Страница 2936: ......
Страница 2939: ......
Страница 2950: ......
Страница 2954: ......
Страница 2960: ......
Страница 2962: ...5 Attach the Fuel Storage Tanker to the hose and remove the fuel 6 Remove the hose and the hose guide ...
Страница 2968: ......
Страница 2971: ...4 Pull on the connection to make sure it is fully engaged ...
Страница 2973: ......
Страница 2980: ...To install reverse the removal procedure ...
Страница 2981: ......
Страница 2983: ......
Страница 2985: ......
Страница 2988: ......
Страница 2991: ......
Страница 2995: ......
Страница 2997: ......
Страница 2999: ...5 To install reverse the removal procedure ...
Страница 3001: ...5 Remove the bolts and the accelerator cable 6 To install reverse the removal procedure ...
Страница 3003: ......
Страница 3005: ...6 To install reverse the removal procedure ...
Страница 3007: ......
Страница 3031: ......
Страница 3033: ......
Страница 3036: ......
Страница 3049: ...9 18591 Heater blower motor resistor ...
Страница 3090: ......
Страница 3098: ......
Страница 3104: ......
Страница 3112: ......
Страница 3114: ......
Страница 3116: ......
Страница 3119: ......
Страница 3122: ......
Страница 3126: ......
Страница 3128: ......
Страница 3130: ......
Страница 3132: ......
Страница 3134: ......
Страница 3138: ...9 19893 A C evaporator register LH ...
Страница 3141: ...5 Remove the register Installation 1 To install reverse the removal procedure ...
Страница 3142: ......
Страница 3149: ......
Страница 3151: ...8 Remove the screw 9 Remove the screws and remove the plenum chamber Installation 1 To install reverse the removal procedure ...
Страница 3152: ......
Страница 3154: ......
Страница 3161: ......
Страница 3165: ......
Страница 3167: ......
Страница 3171: ...Assembly 1 To assemble reverse the disassembly procedure ...
Страница 3173: ......
Страница 3184: ...DIAGNOSIS AND TESTING Air Conditioning Refer to Section 412 00 SECTION 412 03 Air Conditioning 2003 Mustang Workshop Manual ...
Страница 3188: ......
Страница 3191: ......
Страница 3204: ......
Страница 3212: ......
Страница 3221: ......
Страница 3224: ......
Страница 3229: ......
Страница 3232: ......
Страница 3236: ...Shaft fully retracted with vacuum applied to both ports ...
Страница 3237: ...DIAGNOSIS AND TESTING Control Components Refer to Section 412 00 SECTION 412 04 Control Components 2003 Mustang Workshop Manual ...
Страница 3241: ...8 Install the control head 9 Install the center instrument panel register For additional information refer to Section 412 01 ...
Страница 3243: ...1 To install reverse the removal procedure ...
Страница 3246: ......
Страница 3248: ......
Страница 3306: ......
Страница 3317: ......
Страница 3340: ......
Страница 3343: ......
Страница 3361: ......
Страница 3363: ......
Страница 3365: ......
Страница 3367: ...No Does the meter read REPLACE BATTERY INSTALL a new battery Does the meter read BAD CELL REPLACE INSTALL a new battery ...
Страница 3369: ......
Страница 3372: ......
Страница 3374: ......
Страница 3380: ......
Страница 3382: ......
Страница 3384: ...DIAGNOSIS AND TESTING Generator Refer to Section 414 00 SECTION 414 02 Generator and Regulator 2003 Mustang Workshop Manual ...
Страница 3386: ......
Страница 3388: ...6 To install reverse the removal procedure ...
Страница 3390: ......
Страница 3417: ...DIAGNOSIS AND TESTING Audio System Refer to Section 415 00 SECTION 415 01 Audio Unit 2003 Mustang Workshop Manual ...
Страница 3420: ......
Страница 3423: ......
Страница 3426: ...DIAGNOSIS AND TESTING Antenna Refer to Section 415 00 SECTION 415 02 Antenna 2003 Mustang Workshop Manual ...
Страница 3428: ......
Страница 3430: ......
Страница 3433: ...DIAGNOSIS AND TESTING Speakers Refer to Section 415 00 SECTION 415 03 Speakers 2003 Mustang Workshop Manual ...
Страница 3435: ......
Страница 3439: ......
Страница 3441: ......
Страница 3452: ......
Страница 3457: ......
Страница 3470: ......
Страница 3478: ......
Страница 3480: ......
Страница 3482: ......
Страница 3484: ......
Страница 3487: ......
Страница 3491: ......
Страница 3508: ......
Страница 3510: ......
Страница 3520: ......
Страница 3523: ......
Страница 3544: ...Is the resistance less than 5 ohms ...
Страница 3547: ......
Страница 3550: ...Programmable Parameters Index System Programmable Parameter Items Warnings Chimes Belt Minder ...
Страница 3571: ......
Страница 3573: ......
Страница 3577: ......
Страница 3579: ......
Страница 3581: ......
Страница 3585: ......
Страница 3590: ......
Страница 3595: ......
Страница 3602: ...Check the fender alignment and adjust as needed ...
Страница 3605: ......
Страница 3609: ......
Страница 3611: ......
Страница 3613: ......
Страница 3615: ......
Страница 3617: ...Installation 1 NOTE If removed apply new sealer To install reverse the removal procedure ...
Страница 3618: ......
Страница 3625: ...7 Remove the lower quarter trim panel 8 To install reverse the removal procedure ...
Страница 3628: ......
Страница 3631: ......
Страница 3634: ......
Страница 3643: ...8 To install reverse the removal procedure ...
Страница 3645: ...Installation 1 To install reverse the removal procedure ...
Страница 3647: ...5 To install reverse the removal procedure Inspect the pin type retainer seals Install new pin type retainer seals if damaged ...
Страница 3660: ...To install reverse the removal procedure ...
Страница 3662: ......
Страница 3666: ......
Страница 3683: ......
Страница 3686: ......
Страница 3688: ...All vehicles 6 To install reverse the removal procedure ...
Страница 3691: ...All vehicles 10 To install reverse the removal procedure ...
Страница 3693: ...8 Disconnect the power seat electrical connector 9 Remove the power seat 10 To install reverse the removal procedure ...
Страница 3695: ......
Страница 3701: ......
Страница 3709: ...All vehicles 13 To assemble reverse the disassembly procedure ...
Страница 3711: ......
Страница 3745: ......
Страница 3748: ......
Страница 3751: ......
Страница 3753: ......
Страница 3755: ......
Страница 3758: ......
Страница 3767: ......
Страница 3769: ...6 Remove the watershield 7 Remove the interior weatherstrip 8 Remove the bolt 9 Remove the bolts and the glass ...
Страница 3770: ...Installation 1 To install reverse the removal procedure ...
Страница 3772: ......
Страница 3774: ......
Страница 3776: ......
Страница 3778: ......
Страница 3788: ......
Страница 3809: ......
Страница 3811: ...9 Remove the screws and the floor console 10 To install reverse the removal procedure ...
Страница 3813: ......
Страница 3815: ......
Страница 3819: ......
Страница 3821: ......
Страница 3823: ......
Страница 3825: ...Installation 1 To install reverse the removal procedure ...
Страница 3827: ......
Страница 3832: ...Installation 1 To install reverse the removal procedure ...
Страница 3834: ......
Страница 3837: ......
Страница 3840: ......
Страница 3887: ......
Страница 3889: ......
Страница 3893: ...5 Install the cowl top vent panels Adjust wiper pivot arms as necessary Refer to Wiper Blade and Pivot Arm Adjustment ...
Страница 3896: ......
Страница 3898: ......
Страница 3904: ......
Страница 3906: ......
Страница 3916: ......
Страница 3925: ......
Страница 3937: ...24 Install the side quarter trim panel For additional information refer to Section 501 05 ...
Страница 3943: ...13 If necessary connect the rear defroster connectors ...
Страница 3956: ...27 Install the clips 28 Install the exterior mouldings ...
Страница 3959: ......
Страница 3973: ...6 To install reverse the removal procedure ...
Страница 3975: ...6 To install reverse the removal procedure ...
Страница 3977: ...6 To install reverse the removal procedure ...
Страница 3992: ......
Страница 3996: ......
Страница 4006: ......
Страница 4008: ...2 Check the restraint system for correct operation ...
Страница 4010: ......
Страница 4016: ......
Страница 4022: ......
Страница 4027: ...restraints control module Data Link Connector DLC RCM Circuitry Test P ...
Страница 4073: ......
Страница 4075: ......
Страница 4078: ......
Страница 4081: ......
Страница 4084: ......
Страница 4091: ......
Страница 4093: ......
Страница 4097: ......
Страница 4101: ...Restraint System SRS in the Diagnosis and Testing portion of this section ...
Страница 4122: ......
Страница 4128: ......
Страница 4133: ......
Страница 4137: ...Lower and remove the front subframe ...
Страница 4141: ...Lower and remove the front subframe 17 To install reverse the removal procedure ...
Страница 4143: ......
Страница 4145: ......
Страница 4156: ...Fig 1 3 8L Air Conditioning Circuit 4 6L 2003 Ford Mustang 2003 SYSTEM WIRING DIAGRAMS Ford Mustang ...
Страница 4157: ...Fig 2 4 6L Air Conditioning Circuit ANTI LOCK BRAKES 2003 Ford Mustang 2003 SYSTEM WIRING DIAGRAMS Ford Mustang ...
Страница 4158: ...Fig 3 Anti lock Brakes Circuit ANTI THEFT 2003 Ford Mustang 2003 SYSTEM WIRING DIAGRAMS Ford Mustang ...
Страница 4159: ...Fig 4 Passive Anti theft Circuit BODY CONTROL MODULES 2003 Ford Mustang 2003 SYSTEM WIRING DIAGRAMS Ford Mustang ...
Страница 4160: ...Fig 5 Body Control Modules Circuit COMPUTER DATA LINES 2003 Ford Mustang 2003 SYSTEM WIRING DIAGRAMS Ford Mustang ...
Страница 4161: ...Fig 6 Computer Data Lines Circuit COOLING FAN 2003 Ford Mustang 2003 SYSTEM WIRING DIAGRAMS Ford Mustang ...
Страница 4162: ...3 8L Fig 7 3 8L Cooling Fan Circuit 2003 Ford Mustang 2003 SYSTEM WIRING DIAGRAMS Ford Mustang ...
Страница 4163: ...4 6L Fig 8 4 6L Cooling Fan Circuit 2003 Ford Mustang 2003 SYSTEM WIRING DIAGRAMS Ford Mustang ...
Страница 4164: ...CRUISE CONTROL Fig 9 Cruise Control Circuit 2003 Ford Mustang 2003 SYSTEM WIRING DIAGRAMS Ford Mustang ...
Страница 4165: ...DEFOGGERS Fig 10 Defoggers Circuit 2003 Ford Mustang 2003 SYSTEM WIRING DIAGRAMS Ford Mustang ...
Страница 4166: ...ENGINE PERFORMANCE 3 8L 2003 Ford Mustang 2003 SYSTEM WIRING DIAGRAMS Ford Mustang ...
Страница 4168: ...Fig 13 3 8L Engine Performance Circuit 3 of 3 4 6L DOHC 2003 Ford Mustang 2003 SYSTEM WIRING DIAGRAMS Ford Mustang ...
Страница 4169: ...Fig 14 4 6L DOHC Engine Performance Circuit 1 of 3 2003 Ford Mustang 2003 SYSTEM WIRING DIAGRAMS Ford Mustang ...
Страница 4170: ...Fig 15 4 6L DOHC Engine Performance Circuit 2 of 3 2003 Ford Mustang 2003 SYSTEM WIRING DIAGRAMS Ford Mustang ...
Страница 4171: ...Fig 16 4 6L DOHC Engine Performance Circuit 3 of 3 4 6L SC 2003 Ford Mustang 2003 SYSTEM WIRING DIAGRAMS Ford Mustang ...
Страница 4172: ...Fig 17 4 6L SC Engine Performance Circuit 1 of 3 2003 Ford Mustang 2003 SYSTEM WIRING DIAGRAMS Ford Mustang ...
Страница 4173: ...Fig 18 4 6L SC Engine Performance Circuit 2 of 3 2003 Ford Mustang 2003 SYSTEM WIRING DIAGRAMS Ford Mustang ...
Страница 4174: ...Fig 19 4 6L SC Engine Performance Circuit 3 of 3 4 6L SOHC 2003 Ford Mustang 2003 SYSTEM WIRING DIAGRAMS Ford Mustang ...
Страница 4175: ...Fig 20 4 6L SOHC Engine Performance Circuit 1 of 3 2003 Ford Mustang 2003 SYSTEM WIRING DIAGRAMS Ford Mustang ...
Страница 4176: ...Fig 21 4 6L SOHC Engine Performance Circuit 2 of 3 2003 Ford Mustang 2003 SYSTEM WIRING DIAGRAMS Ford Mustang ...
Страница 4177: ...Fig 22 4 6L SOHC Engine Performance Circuit 3 of 3 EXTERIOR LIGHTS 2003 Ford Mustang 2003 SYSTEM WIRING DIAGRAMS Ford Mustang ...
Страница 4178: ...Fig 23 Back up Lamps Circuit 2003 Ford Mustang 2003 SYSTEM WIRING DIAGRAMS Ford Mustang ...
Страница 4179: ...Fig 24 Exterior Lamps Circuit GROUND DISTRIBUTION 2003 Ford Mustang 2003 SYSTEM WIRING DIAGRAMS Ford Mustang ...
Страница 4180: ...Fig 25 Ground Distribution Circuit 1 of 2 2003 Ford Mustang 2003 SYSTEM WIRING DIAGRAMS Ford Mustang ...
Страница 4181: ...Fig 26 Ground Distribution Circuit 2 of 2 HEADLIGHTS 2003 Ford Mustang 2003 SYSTEM WIRING DIAGRAMS Ford Mustang ...
Страница 4182: ...Fig 27 Headlights Circuit HORN 2003 Ford Mustang 2003 SYSTEM WIRING DIAGRAMS Ford Mustang ...
Страница 4183: ...Fig 28 Horn Circuit INSTRUMENT CLUSTER 2003 Ford Mustang 2003 SYSTEM WIRING DIAGRAMS Ford Mustang ...
Страница 4184: ...Fig 29 Instrument Cluster Circuit INTERIOR LIGHTS 2003 Ford Mustang 2003 SYSTEM WIRING DIAGRAMS Ford Mustang ...
Страница 4185: ...Fig 30 Courtesy Lamps Circuit 2003 Ford Mustang 2003 SYSTEM WIRING DIAGRAMS Ford Mustang ...
Страница 4186: ...Fig 31 Instrument Illumination Circuit POWER DISTRIBUTION 2003 Ford Mustang 2003 SYSTEM WIRING DIAGRAMS Ford Mustang ...
Страница 4187: ...Fig 32 Power Distribution Circuit 1 of 3 2003 Ford Mustang 2003 SYSTEM WIRING DIAGRAMS Ford Mustang ...
Страница 4188: ...Fig 33 Power Distribution Circuit 2 of 3 2003 Ford Mustang 2003 SYSTEM WIRING DIAGRAMS Ford Mustang ...
Страница 4189: ...Fig 34 Power Distribution Circuit 3 of 3 POWER DOOR LOCKS 2003 Ford Mustang 2003 SYSTEM WIRING DIAGRAMS Ford Mustang ...
Страница 4190: ...Fig 35 Power Door Locks Circuit POWER MIRRORS 2003 Ford Mustang 2003 SYSTEM WIRING DIAGRAMS Ford Mustang ...
Страница 4191: ...Fig 36 Power Mirrors Circuit POWER SEATS 2003 Ford Mustang 2003 SYSTEM WIRING DIAGRAMS Ford Mustang ...
Страница 4192: ...Fig 37 Lumbar Circuit 2003 Ford Mustang 2003 SYSTEM WIRING DIAGRAMS Ford Mustang ...
Страница 4193: ...Fig 38 Power Seat Circuit POWER TOP SUNROOF 2003 Ford Mustang 2003 SYSTEM WIRING DIAGRAMS Ford Mustang ...
Страница 4194: ...Fig 39 Power Top Sunroof Circuit POWER WINDOWS 2003 Ford Mustang 2003 SYSTEM WIRING DIAGRAMS Ford Mustang ...
Страница 4195: ...Fig 40 Power Windows Circuit Convertible 2003 Ford Mustang 2003 SYSTEM WIRING DIAGRAMS Ford Mustang ...
Страница 4196: ...Fig 41 Power Windows Circuit Coupe RADIO 2003 Ford Mustang 2003 SYSTEM WIRING DIAGRAMS Ford Mustang ...
Страница 4197: ...Fig 42 Base Radio Circuit 2003 Ford Mustang 2003 SYSTEM WIRING DIAGRAMS Ford Mustang ...
Страница 4203: ...Fig 48 Shift Interlock Circuit STARTING CHARGING 2003 Ford Mustang 2003 SYSTEM WIRING DIAGRAMS Ford Mustang ...
Страница 4204: ...Fig 49 Charging Circuit 2003 Ford Mustang 2003 SYSTEM WIRING DIAGRAMS Ford Mustang ...
Страница 4205: ...Fig 50 Starting Circuit SUPPLEMENTAL RESTRAINTS 2003 Ford Mustang 2003 SYSTEM WIRING DIAGRAMS Ford Mustang ...
Страница 4206: ...Fig 51 Supplemental Restraints Circuit TRANSMISSION 2003 Ford Mustang 2003 SYSTEM WIRING DIAGRAMS Ford Mustang ...
Страница 4207: ...Fig 52 A T Circuit TRUNK TAILGATE FUEL DOOR 2003 Ford Mustang 2003 SYSTEM WIRING DIAGRAMS Ford Mustang ...
Страница 4208: ...Fig 53 Trunk Tailgate Fuel Door Circuit WARNING SYSTEMS 2003 Ford Mustang 2003 SYSTEM WIRING DIAGRAMS Ford Mustang ...
Страница 4209: ...Fig 54 Warning Systems Circuit WIPER WASHER 2003 Ford Mustang 2003 SYSTEM WIRING DIAGRAMS Ford Mustang ...
Страница 4210: ...Fig 55 Wiper Washer Circuit 2003 Ford Mustang 2003 SYSTEM WIRING DIAGRAMS Ford Mustang ...
Страница 4212: ...Fig 1 3 8L Air Conditioning Circuit 4 6L 2003 Ford Mustang GT 2003 SYSTEM WIRING DIAGRAMS Ford Mustang ...
Страница 4213: ...Fig 2 4 6L Air Conditioning Circuit ANTI LOCK BRAKES 2003 Ford Mustang GT 2003 SYSTEM WIRING DIAGRAMS Ford Mustang ...
Страница 4214: ...Fig 3 Anti lock Brakes Circuit ANTI THEFT 2003 Ford Mustang GT 2003 SYSTEM WIRING DIAGRAMS Ford Mustang ...
Страница 4215: ...Fig 4 Passive Anti theft Circuit BODY CONTROL MODULES 2003 Ford Mustang GT 2003 SYSTEM WIRING DIAGRAMS Ford Mustang ...
Страница 4216: ...Fig 5 Body Control Modules Circuit COMPUTER DATA LINES 2003 Ford Mustang GT 2003 SYSTEM WIRING DIAGRAMS Ford Mustang ...
Страница 4217: ...Fig 6 Computer Data Lines Circuit COOLING FAN 2003 Ford Mustang GT 2003 SYSTEM WIRING DIAGRAMS Ford Mustang ...
Страница 4218: ...3 8L Fig 7 3 8L Cooling Fan Circuit 2003 Ford Mustang GT 2003 SYSTEM WIRING DIAGRAMS Ford Mustang ...
Страница 4219: ...4 6L Fig 8 4 6L Cooling Fan Circuit 2003 Ford Mustang GT 2003 SYSTEM WIRING DIAGRAMS Ford Mustang ...
Страница 4220: ...CRUISE CONTROL Fig 9 Cruise Control Circuit 2003 Ford Mustang GT 2003 SYSTEM WIRING DIAGRAMS Ford Mustang ...
Страница 4221: ...DEFOGGERS Fig 10 Defoggers Circuit 2003 Ford Mustang GT 2003 SYSTEM WIRING DIAGRAMS Ford Mustang ...
Страница 4222: ...ENGINE PERFORMANCE 3 8L 2003 Ford Mustang GT 2003 SYSTEM WIRING DIAGRAMS Ford Mustang ...
Страница 4224: ...Fig 13 3 8L Engine Performance Circuit 3 of 3 4 6L DOHC 2003 Ford Mustang GT 2003 SYSTEM WIRING DIAGRAMS Ford Mustang ...
Страница 4225: ...Fig 14 4 6L DOHC Engine Performance Circuit 1 of 3 2003 Ford Mustang GT 2003 SYSTEM WIRING DIAGRAMS Ford Mustang ...
Страница 4226: ...Fig 15 4 6L DOHC Engine Performance Circuit 2 of 3 2003 Ford Mustang GT 2003 SYSTEM WIRING DIAGRAMS Ford Mustang ...
Страница 4227: ...Fig 16 4 6L DOHC Engine Performance Circuit 3 of 3 4 6L SC 2003 Ford Mustang GT 2003 SYSTEM WIRING DIAGRAMS Ford Mustang ...
Страница 4228: ...Fig 17 4 6L SC Engine Performance Circuit 1 of 3 2003 Ford Mustang GT 2003 SYSTEM WIRING DIAGRAMS Ford Mustang ...
Страница 4229: ...Fig 18 4 6L SC Engine Performance Circuit 2 of 3 2003 Ford Mustang GT 2003 SYSTEM WIRING DIAGRAMS Ford Mustang ...
Страница 4230: ...Fig 19 4 6L SC Engine Performance Circuit 3 of 3 4 6L SOHC 2003 Ford Mustang GT 2003 SYSTEM WIRING DIAGRAMS Ford Mustang ...
Страница 4231: ...Fig 20 4 6L SOHC Engine Performance Circuit 1 of 3 2003 Ford Mustang GT 2003 SYSTEM WIRING DIAGRAMS Ford Mustang ...
Страница 4232: ...Fig 21 4 6L SOHC Engine Performance Circuit 2 of 3 2003 Ford Mustang GT 2003 SYSTEM WIRING DIAGRAMS Ford Mustang ...
Страница 4233: ...Fig 22 4 6L SOHC Engine Performance Circuit 3 of 3 EXTERIOR LIGHTS 2003 Ford Mustang GT 2003 SYSTEM WIRING DIAGRAMS Ford Mustang ...
Страница 4234: ...Fig 23 Back up Lamps Circuit 2003 Ford Mustang GT 2003 SYSTEM WIRING DIAGRAMS Ford Mustang ...
Страница 4235: ...Fig 24 Exterior Lamps Circuit GROUND DISTRIBUTION 2003 Ford Mustang GT 2003 SYSTEM WIRING DIAGRAMS Ford Mustang ...
Страница 4236: ...Fig 25 Ground Distribution Circuit 1 of 2 2003 Ford Mustang GT 2003 SYSTEM WIRING DIAGRAMS Ford Mustang ...
Страница 4237: ...Fig 26 Ground Distribution Circuit 2 of 2 HEADLIGHTS 2003 Ford Mustang GT 2003 SYSTEM WIRING DIAGRAMS Ford Mustang ...
Страница 4238: ...Fig 27 Headlights Circuit HORN 2003 Ford Mustang GT 2003 SYSTEM WIRING DIAGRAMS Ford Mustang ...
Страница 4239: ...Fig 28 Horn Circuit INSTRUMENT CLUSTER 2003 Ford Mustang GT 2003 SYSTEM WIRING DIAGRAMS Ford Mustang ...
Страница 4240: ...Fig 29 Instrument Cluster Circuit INTERIOR LIGHTS 2003 Ford Mustang GT 2003 SYSTEM WIRING DIAGRAMS Ford Mustang ...
Страница 4241: ...Fig 30 Courtesy Lamps Circuit 2003 Ford Mustang GT 2003 SYSTEM WIRING DIAGRAMS Ford Mustang ...
Страница 4242: ...Fig 31 Instrument Illumination Circuit POWER DISTRIBUTION 2003 Ford Mustang GT 2003 SYSTEM WIRING DIAGRAMS Ford Mustang ...
Страница 4243: ...Fig 32 Power Distribution Circuit 1 of 3 2003 Ford Mustang GT 2003 SYSTEM WIRING DIAGRAMS Ford Mustang ...
Страница 4244: ...Fig 33 Power Distribution Circuit 2 of 3 2003 Ford Mustang GT 2003 SYSTEM WIRING DIAGRAMS Ford Mustang ...
Страница 4245: ...Fig 34 Power Distribution Circuit 3 of 3 POWER DOOR LOCKS 2003 Ford Mustang GT 2003 SYSTEM WIRING DIAGRAMS Ford Mustang ...
Страница 4246: ...Fig 35 Power Door Locks Circuit POWER MIRRORS 2003 Ford Mustang GT 2003 SYSTEM WIRING DIAGRAMS Ford Mustang ...
Страница 4247: ...Fig 36 Power Mirrors Circuit POWER SEATS 2003 Ford Mustang GT 2003 SYSTEM WIRING DIAGRAMS Ford Mustang ...
Страница 4248: ...Fig 37 Lumbar Circuit 2003 Ford Mustang GT 2003 SYSTEM WIRING DIAGRAMS Ford Mustang ...
Страница 4249: ...Fig 38 Power Seat Circuit POWER TOP SUNROOF 2003 Ford Mustang GT 2003 SYSTEM WIRING DIAGRAMS Ford Mustang ...
Страница 4250: ...Fig 39 Power Top Sunroof Circuit POWER WINDOWS 2003 Ford Mustang GT 2003 SYSTEM WIRING DIAGRAMS Ford Mustang ...
Страница 4251: ...Fig 40 Power Windows Circuit Convertible 2003 Ford Mustang GT 2003 SYSTEM WIRING DIAGRAMS Ford Mustang ...
Страница 4252: ...Fig 41 Power Windows Circuit Coupe RADIO 2003 Ford Mustang GT 2003 SYSTEM WIRING DIAGRAMS Ford Mustang ...
Страница 4253: ...Fig 42 Base Radio Circuit 2003 Ford Mustang GT 2003 SYSTEM WIRING DIAGRAMS Ford Mustang ...
Страница 4259: ...Fig 48 Shift Interlock Circuit STARTING CHARGING 2003 Ford Mustang GT 2003 SYSTEM WIRING DIAGRAMS Ford Mustang ...
Страница 4260: ...Fig 49 Charging Circuit 2003 Ford Mustang GT 2003 SYSTEM WIRING DIAGRAMS Ford Mustang ...
Страница 4261: ...Fig 50 Starting Circuit SUPPLEMENTAL RESTRAINTS 2003 Ford Mustang GT 2003 SYSTEM WIRING DIAGRAMS Ford Mustang ...
Страница 4262: ...Fig 51 Supplemental Restraints Circuit TRANSMISSION 2003 Ford Mustang GT 2003 SYSTEM WIRING DIAGRAMS Ford Mustang ...
Страница 4263: ...Fig 52 A T Circuit TRUNK TAILGATE FUEL DOOR 2003 Ford Mustang GT 2003 SYSTEM WIRING DIAGRAMS Ford Mustang ...
Страница 4264: ...Fig 53 Trunk Tailgate Fuel Door Circuit WARNING SYSTEMS 2003 Ford Mustang GT 2003 SYSTEM WIRING DIAGRAMS Ford Mustang ...
Страница 4265: ...Fig 54 Warning Systems Circuit WIPER WASHER 2003 Ford Mustang GT 2003 SYSTEM WIRING DIAGRAMS Ford Mustang ...
Страница 4266: ...Fig 55 Wiper Washer Circuit 2003 Ford Mustang GT 2003 SYSTEM WIRING DIAGRAMS Ford Mustang ...
Страница 4268: ...Fig 1 3 8L Air Conditioning Circuit 4 6L 2003 Ford Mustang Cobra 2003 SYSTEM WIRING DIAGRAMS Ford Mustang ...
Страница 4269: ...Fig 2 4 6L Air Conditioning Circuit ANTI LOCK BRAKES 2003 Ford Mustang Cobra 2003 SYSTEM WIRING DIAGRAMS Ford Mustang ...
Страница 4270: ...Fig 3 Anti lock Brakes Circuit ANTI THEFT 2003 Ford Mustang Cobra 2003 SYSTEM WIRING DIAGRAMS Ford Mustang ...
Страница 4271: ...Fig 4 Passive Anti theft Circuit BODY CONTROL MODULES 2003 Ford Mustang Cobra 2003 SYSTEM WIRING DIAGRAMS Ford Mustang ...
Страница 4272: ...Fig 5 Body Control Modules Circuit COMPUTER DATA LINES 2003 Ford Mustang Cobra 2003 SYSTEM WIRING DIAGRAMS Ford Mustang ...
Страница 4273: ...Fig 6 Computer Data Lines Circuit COOLING FAN 2003 Ford Mustang Cobra 2003 SYSTEM WIRING DIAGRAMS Ford Mustang ...
Страница 4274: ...3 8L Fig 7 3 8L Cooling Fan Circuit 2003 Ford Mustang Cobra 2003 SYSTEM WIRING DIAGRAMS Ford Mustang ...
Страница 4275: ...4 6L Fig 8 4 6L Cooling Fan Circuit 2003 Ford Mustang Cobra 2003 SYSTEM WIRING DIAGRAMS Ford Mustang ...
Страница 4276: ...CRUISE CONTROL Fig 9 Cruise Control Circuit 2003 Ford Mustang Cobra 2003 SYSTEM WIRING DIAGRAMS Ford Mustang ...
Страница 4277: ...DEFOGGERS Fig 10 Defoggers Circuit 2003 Ford Mustang Cobra 2003 SYSTEM WIRING DIAGRAMS Ford Mustang ...
Страница 4278: ...ENGINE PERFORMANCE 3 8L 2003 Ford Mustang Cobra 2003 SYSTEM WIRING DIAGRAMS Ford Mustang ...
Страница 4280: ...Fig 13 3 8L Engine Performance Circuit 3 of 3 4 6L DOHC 2003 Ford Mustang Cobra 2003 SYSTEM WIRING DIAGRAMS Ford Mustang ...
Страница 4281: ...Fig 14 4 6L DOHC Engine Performance Circuit 1 of 3 2003 Ford Mustang Cobra 2003 SYSTEM WIRING DIAGRAMS Ford Mustang ...
Страница 4282: ...Fig 15 4 6L DOHC Engine Performance Circuit 2 of 3 2003 Ford Mustang Cobra 2003 SYSTEM WIRING DIAGRAMS Ford Mustang ...
Страница 4283: ...Fig 16 4 6L DOHC Engine Performance Circuit 3 of 3 4 6L SC 2003 Ford Mustang Cobra 2003 SYSTEM WIRING DIAGRAMS Ford Mustang ...
Страница 4284: ...Fig 17 4 6L SC Engine Performance Circuit 1 of 3 2003 Ford Mustang Cobra 2003 SYSTEM WIRING DIAGRAMS Ford Mustang ...
Страница 4285: ...Fig 18 4 6L SC Engine Performance Circuit 2 of 3 2003 Ford Mustang Cobra 2003 SYSTEM WIRING DIAGRAMS Ford Mustang ...
Страница 4286: ...Fig 19 4 6L SC Engine Performance Circuit 3 of 3 4 6L SOHC 2003 Ford Mustang Cobra 2003 SYSTEM WIRING DIAGRAMS Ford Mustang ...
Страница 4287: ...Fig 20 4 6L SOHC Engine Performance Circuit 1 of 3 2003 Ford Mustang Cobra 2003 SYSTEM WIRING DIAGRAMS Ford Mustang ...
Страница 4288: ...Fig 21 4 6L SOHC Engine Performance Circuit 2 of 3 2003 Ford Mustang Cobra 2003 SYSTEM WIRING DIAGRAMS Ford Mustang ...
Страница 4290: ...Fig 23 Back up Lamps Circuit 2003 Ford Mustang Cobra 2003 SYSTEM WIRING DIAGRAMS Ford Mustang ...
Страница 4291: ...Fig 24 Exterior Lamps Circuit GROUND DISTRIBUTION 2003 Ford Mustang Cobra 2003 SYSTEM WIRING DIAGRAMS Ford Mustang ...
Страница 4292: ...Fig 25 Ground Distribution Circuit 1 of 2 2003 Ford Mustang Cobra 2003 SYSTEM WIRING DIAGRAMS Ford Mustang ...
Страница 4293: ...Fig 26 Ground Distribution Circuit 2 of 2 HEADLIGHTS 2003 Ford Mustang Cobra 2003 SYSTEM WIRING DIAGRAMS Ford Mustang ...
Страница 4294: ...Fig 27 Headlights Circuit HORN 2003 Ford Mustang Cobra 2003 SYSTEM WIRING DIAGRAMS Ford Mustang ...
Страница 4295: ...Fig 28 Horn Circuit INSTRUMENT CLUSTER 2003 Ford Mustang Cobra 2003 SYSTEM WIRING DIAGRAMS Ford Mustang ...
Страница 4296: ...Fig 29 Instrument Cluster Circuit INTERIOR LIGHTS 2003 Ford Mustang Cobra 2003 SYSTEM WIRING DIAGRAMS Ford Mustang ...
Страница 4297: ...Fig 30 Courtesy Lamps Circuit 2003 Ford Mustang Cobra 2003 SYSTEM WIRING DIAGRAMS Ford Mustang ...
Страница 4298: ...Fig 31 Instrument Illumination Circuit POWER DISTRIBUTION 2003 Ford Mustang Cobra 2003 SYSTEM WIRING DIAGRAMS Ford Mustang ...
Страница 4299: ...Fig 32 Power Distribution Circuit 1 of 3 2003 Ford Mustang Cobra 2003 SYSTEM WIRING DIAGRAMS Ford Mustang ...
Страница 4300: ...Fig 33 Power Distribution Circuit 2 of 3 2003 Ford Mustang Cobra 2003 SYSTEM WIRING DIAGRAMS Ford Mustang ...
Страница 4301: ...Fig 34 Power Distribution Circuit 3 of 3 POWER DOOR LOCKS 2003 Ford Mustang Cobra 2003 SYSTEM WIRING DIAGRAMS Ford Mustang ...
Страница 4302: ...Fig 35 Power Door Locks Circuit POWER MIRRORS 2003 Ford Mustang Cobra 2003 SYSTEM WIRING DIAGRAMS Ford Mustang ...
Страница 4303: ...Fig 36 Power Mirrors Circuit POWER SEATS 2003 Ford Mustang Cobra 2003 SYSTEM WIRING DIAGRAMS Ford Mustang ...
Страница 4304: ...Fig 37 Lumbar Circuit 2003 Ford Mustang Cobra 2003 SYSTEM WIRING DIAGRAMS Ford Mustang ...
Страница 4305: ...Fig 38 Power Seat Circuit POWER TOP SUNROOF 2003 Ford Mustang Cobra 2003 SYSTEM WIRING DIAGRAMS Ford Mustang ...
Страница 4306: ...Fig 39 Power Top Sunroof Circuit POWER WINDOWS 2003 Ford Mustang Cobra 2003 SYSTEM WIRING DIAGRAMS Ford Mustang ...
Страница 4307: ...Fig 40 Power Windows Circuit Convertible 2003 Ford Mustang Cobra 2003 SYSTEM WIRING DIAGRAMS Ford Mustang ...
Страница 4308: ...Fig 41 Power Windows Circuit Coupe RADIO 2003 Ford Mustang Cobra 2003 SYSTEM WIRING DIAGRAMS Ford Mustang ...
Страница 4309: ...Fig 42 Base Radio Circuit 2003 Ford Mustang Cobra 2003 SYSTEM WIRING DIAGRAMS Ford Mustang ...
Страница 4315: ...Fig 48 Shift Interlock Circuit STARTING CHARGING 2003 Ford Mustang Cobra 2003 SYSTEM WIRING DIAGRAMS Ford Mustang ...
Страница 4316: ...Fig 49 Charging Circuit 2003 Ford Mustang Cobra 2003 SYSTEM WIRING DIAGRAMS Ford Mustang ...
Страница 4317: ...Fig 50 Starting Circuit SUPPLEMENTAL RESTRAINTS 2003 Ford Mustang Cobra 2003 SYSTEM WIRING DIAGRAMS Ford Mustang ...
Страница 4318: ...Fig 51 Supplemental Restraints Circuit TRANSMISSION 2003 Ford Mustang Cobra 2003 SYSTEM WIRING DIAGRAMS Ford Mustang ...
Страница 4319: ...Fig 52 A T Circuit TRUNK TAILGATE FUEL DOOR 2003 Ford Mustang Cobra 2003 SYSTEM WIRING DIAGRAMS Ford Mustang ...
Страница 4320: ...Fig 53 Trunk Tailgate Fuel Door Circuit WARNING SYSTEMS 2003 Ford Mustang Cobra 2003 SYSTEM WIRING DIAGRAMS Ford Mustang ...
Страница 4321: ...Fig 54 Warning Systems Circuit WIPER WASHER 2003 Ford Mustang Cobra 2003 SYSTEM WIRING DIAGRAMS Ford Mustang ...
Страница 4322: ...Fig 55 Wiper Washer Circuit 2003 Ford Mustang Cobra 2003 SYSTEM WIRING DIAGRAMS Ford Mustang ...
Страница 4324: ...Fig 1 3 8L Air Conditioning Circuit 4 6L 2003 Ford Mustang Mach 1 2003 SYSTEM WIRING DIAGRAMS Ford Mustang ...
Страница 4325: ...Fig 2 4 6L Air Conditioning Circuit ANTI LOCK BRAKES 2003 Ford Mustang Mach 1 2003 SYSTEM WIRING DIAGRAMS Ford Mustang ...
Страница 4326: ...Fig 3 Anti lock Brakes Circuit ANTI THEFT 2003 Ford Mustang Mach 1 2003 SYSTEM WIRING DIAGRAMS Ford Mustang ...
Страница 4327: ...Fig 4 Passive Anti theft Circuit BODY CONTROL MODULES 2003 Ford Mustang Mach 1 2003 SYSTEM WIRING DIAGRAMS Ford Mustang ...
Страница 4328: ...Fig 5 Body Control Modules Circuit COMPUTER DATA LINES 2003 Ford Mustang Mach 1 2003 SYSTEM WIRING DIAGRAMS Ford Mustang ...
Страница 4329: ...Fig 6 Computer Data Lines Circuit COOLING FAN 2003 Ford Mustang Mach 1 2003 SYSTEM WIRING DIAGRAMS Ford Mustang ...
Страница 4330: ...3 8L Fig 7 3 8L Cooling Fan Circuit 2003 Ford Mustang Mach 1 2003 SYSTEM WIRING DIAGRAMS Ford Mustang ...
Страница 4331: ...4 6L Fig 8 4 6L Cooling Fan Circuit 2003 Ford Mustang Mach 1 2003 SYSTEM WIRING DIAGRAMS Ford Mustang ...
Страница 4332: ...CRUISE CONTROL Fig 9 Cruise Control Circuit 2003 Ford Mustang Mach 1 2003 SYSTEM WIRING DIAGRAMS Ford Mustang ...
Страница 4333: ...DEFOGGERS Fig 10 Defoggers Circuit 2003 Ford Mustang Mach 1 2003 SYSTEM WIRING DIAGRAMS Ford Mustang ...
Страница 4334: ...ENGINE PERFORMANCE 3 8L 2003 Ford Mustang Mach 1 2003 SYSTEM WIRING DIAGRAMS Ford Mustang ...
Страница 4336: ...Fig 13 3 8L Engine Performance Circuit 3 of 3 4 6L DOHC 2003 Ford Mustang Mach 1 2003 SYSTEM WIRING DIAGRAMS Ford Mustang ...
Страница 4337: ...Fig 14 4 6L DOHC Engine Performance Circuit 1 of 3 2003 Ford Mustang Mach 1 2003 SYSTEM WIRING DIAGRAMS Ford Mustang ...
Страница 4338: ...Fig 15 4 6L DOHC Engine Performance Circuit 2 of 3 2003 Ford Mustang Mach 1 2003 SYSTEM WIRING DIAGRAMS Ford Mustang ...
Страница 4339: ...Fig 16 4 6L DOHC Engine Performance Circuit 3 of 3 4 6L SC 2003 Ford Mustang Mach 1 2003 SYSTEM WIRING DIAGRAMS Ford Mustang ...
Страница 4340: ...Fig 17 4 6L SC Engine Performance Circuit 1 of 3 2003 Ford Mustang Mach 1 2003 SYSTEM WIRING DIAGRAMS Ford Mustang ...
Страница 4341: ...Fig 18 4 6L SC Engine Performance Circuit 2 of 3 2003 Ford Mustang Mach 1 2003 SYSTEM WIRING DIAGRAMS Ford Mustang ...
Страница 4342: ...Fig 19 4 6L SC Engine Performance Circuit 3 of 3 4 6L SOHC 2003 Ford Mustang Mach 1 2003 SYSTEM WIRING DIAGRAMS Ford Mustang ...
Страница 4343: ...Fig 20 4 6L SOHC Engine Performance Circuit 1 of 3 2003 Ford Mustang Mach 1 2003 SYSTEM WIRING DIAGRAMS Ford Mustang ...
Страница 4344: ...Fig 21 4 6L SOHC Engine Performance Circuit 2 of 3 2003 Ford Mustang Mach 1 2003 SYSTEM WIRING DIAGRAMS Ford Mustang ...
Страница 4346: ...Fig 23 Back up Lamps Circuit 2003 Ford Mustang Mach 1 2003 SYSTEM WIRING DIAGRAMS Ford Mustang ...
Страница 4347: ...Fig 24 Exterior Lamps Circuit GROUND DISTRIBUTION 2003 Ford Mustang Mach 1 2003 SYSTEM WIRING DIAGRAMS Ford Mustang ...
Страница 4348: ...Fig 25 Ground Distribution Circuit 1 of 2 2003 Ford Mustang Mach 1 2003 SYSTEM WIRING DIAGRAMS Ford Mustang ...
Страница 4349: ...Fig 26 Ground Distribution Circuit 2 of 2 HEADLIGHTS 2003 Ford Mustang Mach 1 2003 SYSTEM WIRING DIAGRAMS Ford Mustang ...
Страница 4350: ...Fig 27 Headlights Circuit HORN 2003 Ford Mustang Mach 1 2003 SYSTEM WIRING DIAGRAMS Ford Mustang ...
Страница 4351: ...Fig 28 Horn Circuit INSTRUMENT CLUSTER 2003 Ford Mustang Mach 1 2003 SYSTEM WIRING DIAGRAMS Ford Mustang ...
Страница 4352: ...Fig 29 Instrument Cluster Circuit INTERIOR LIGHTS 2003 Ford Mustang Mach 1 2003 SYSTEM WIRING DIAGRAMS Ford Mustang ...
Страница 4353: ...Fig 30 Courtesy Lamps Circuit 2003 Ford Mustang Mach 1 2003 SYSTEM WIRING DIAGRAMS Ford Mustang ...
Страница 4354: ...Fig 31 Instrument Illumination Circuit POWER DISTRIBUTION 2003 Ford Mustang Mach 1 2003 SYSTEM WIRING DIAGRAMS Ford Mustang ...
Страница 4355: ...Fig 32 Power Distribution Circuit 1 of 3 2003 Ford Mustang Mach 1 2003 SYSTEM WIRING DIAGRAMS Ford Mustang ...
Страница 4356: ...Fig 33 Power Distribution Circuit 2 of 3 2003 Ford Mustang Mach 1 2003 SYSTEM WIRING DIAGRAMS Ford Mustang ...
Страница 4357: ...Fig 34 Power Distribution Circuit 3 of 3 POWER DOOR LOCKS 2003 Ford Mustang Mach 1 2003 SYSTEM WIRING DIAGRAMS Ford Mustang ...
Страница 4358: ...Fig 35 Power Door Locks Circuit POWER MIRRORS 2003 Ford Mustang Mach 1 2003 SYSTEM WIRING DIAGRAMS Ford Mustang ...
Страница 4359: ...Fig 36 Power Mirrors Circuit POWER SEATS 2003 Ford Mustang Mach 1 2003 SYSTEM WIRING DIAGRAMS Ford Mustang ...
Страница 4360: ...Fig 37 Lumbar Circuit 2003 Ford Mustang Mach 1 2003 SYSTEM WIRING DIAGRAMS Ford Mustang ...
Страница 4361: ...Fig 38 Power Seat Circuit POWER TOP SUNROOF 2003 Ford Mustang Mach 1 2003 SYSTEM WIRING DIAGRAMS Ford Mustang ...
Страница 4362: ...Fig 39 Power Top Sunroof Circuit POWER WINDOWS 2003 Ford Mustang Mach 1 2003 SYSTEM WIRING DIAGRAMS Ford Mustang ...
Страница 4363: ...Fig 40 Power Windows Circuit Convertible 2003 Ford Mustang Mach 1 2003 SYSTEM WIRING DIAGRAMS Ford Mustang ...
Страница 4364: ...Fig 41 Power Windows Circuit Coupe RADIO 2003 Ford Mustang Mach 1 2003 SYSTEM WIRING DIAGRAMS Ford Mustang ...
Страница 4365: ...Fig 42 Base Radio Circuit 2003 Ford Mustang Mach 1 2003 SYSTEM WIRING DIAGRAMS Ford Mustang ...
Страница 4371: ...Fig 48 Shift Interlock Circuit STARTING CHARGING 2003 Ford Mustang Mach 1 2003 SYSTEM WIRING DIAGRAMS Ford Mustang ...
Страница 4372: ...Fig 49 Charging Circuit 2003 Ford Mustang Mach 1 2003 SYSTEM WIRING DIAGRAMS Ford Mustang ...
Страница 4373: ...Fig 50 Starting Circuit SUPPLEMENTAL RESTRAINTS 2003 Ford Mustang Mach 1 2003 SYSTEM WIRING DIAGRAMS Ford Mustang ...
Страница 4374: ...Fig 51 Supplemental Restraints Circuit TRANSMISSION 2003 Ford Mustang Mach 1 2003 SYSTEM WIRING DIAGRAMS Ford Mustang ...
Страница 4375: ...Fig 52 A T Circuit TRUNK TAILGATE FUEL DOOR 2003 Ford Mustang Mach 1 2003 SYSTEM WIRING DIAGRAMS Ford Mustang ...
Страница 4376: ...Fig 53 Trunk Tailgate Fuel Door Circuit WARNING SYSTEMS 2003 Ford Mustang Mach 1 2003 SYSTEM WIRING DIAGRAMS Ford Mustang ...
Страница 4377: ...Fig 54 Warning Systems Circuit WIPER WASHER 2003 Ford Mustang Mach 1 2003 SYSTEM WIRING DIAGRAMS Ford Mustang ...
Страница 4378: ...Fig 55 Wiper Washer Circuit 2003 Ford Mustang Mach 1 2003 SYSTEM WIRING DIAGRAMS Ford Mustang ...