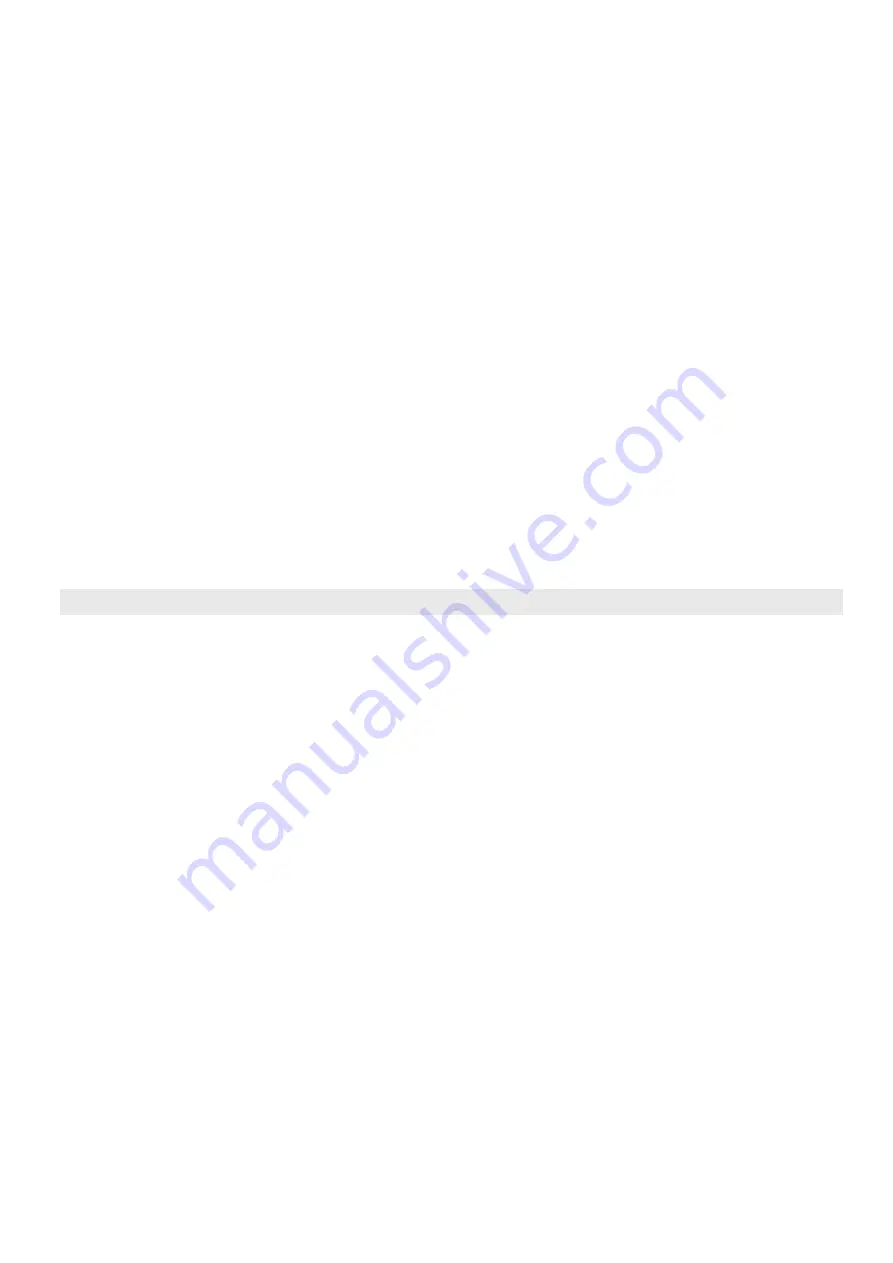
14
3.6 Gas Transformation
Changing a boiler over from natural
gas to LPG and vice versa
is only to
be carried out by qualified personnel.
To check the setting values for the
nozzles and gas supply pressure, use
a pressure gauge connected to the
pressure sockets on the valves.
3.6.1 Change over from natural gas
to LPG
Proceed as follows:
• Remove the natural gas nozzle from
the pilot burner after having unscrewed
the nut that holds the olive and vent the
gas supply pipe to the pilot burner.
• Position the LPG nozzle checking
that it is as indicated in the technical
data table, and after repositioning the
gas supply pipe tighten the nut that
secures the olive.
• Remove the natural gas nozzle on
the main burner and fit the LPG nozz-
le, checking that this is as indicated in
the technical data table.
• Unscrew the pressure regulating cap
on the gas valve and tighten the pres-
sure regulating screw all the way.
• Screw the pressure regulating cap
back on and seal it (using paint or a
self-adhesive label, for example).
• Check the gas circuit for leaks, espe-
cially the points that were disconnected.
• Affix the self-adhesive label provided
that indicates the type of gas and pres-
sure for which the equipment is set.
3.6.2 Change over from LPG to
natural gas
Proceed as follows:
• Remove the LPG nozzle from the
pilot burner after having unscrewed the
nut that holds the olive and vent the
gas supply pipe to the pilot burner.
• Position the natural gas nozzle chec-
king that it is as indicated in the techni-
cal data table, and after repositioning
the gas supply pipe tighten the nut that
secures the olive.
• Remove the LPG nozzle on the main
burner and fit the natural gas nozzle,
checking that this is as indicated in the
technical data table.
• Unscrew the pressure regulating cap
on the gas valve and unscrew the
pressure regulating screws so that the
pressure at the outlet is as specified in
the technical data table.
• Screw the pressure regulating cap
back on and seal it (using paint or a
self-adhesive label, for example).
• Check the gas circuit for leaks,
especially the points that were dis-
connected.
• Affix the self-adhesive label provided
that indicates the type of gas and pres-
sure for which the equipment is set.
4. MAINTENANCE
In order to ensure that the equip-
ment is efficient and that it functions
correctly, maintenance must be car-
ried out annually, based on the pro-
gramme laid out below:
It is obligatory for all maintenance
(and repair) operations to be car-
ried out by qualified personnel.
Before starting any maintenance
work that involves replacing com-
ponents and/or cleaning the insi-
de of the boiler, disconnect the
equipment from the electrical
power supply
.
Maintenance programme
Routine maintenance must include
the following checks:
- Check of the general integrity of
the boiler.
- Checking the gas supply to the
boiler for leaks.
- Checking ignition of the boiler.
- Checking the boiler’s combustion
parameters by analysing the smoke
(this check is done every two years
if the boiler is installed on its own.
Where the boiler is installed in a
cascading system, this check is run
annually).
- Checking the integrity, good state
of preservation, and leak test on the
smoke flue.
- Checking the integrity of safety
devices on the boiler in general.
- Checking for water leaks and
rusting on the boiler’s couplings.
- Checking the efficiency of the
system’s safety valve.
The following cleaning is to be
done (with the boiler cold):
- General internal cleanliness of the
boiler.
- Cleanliness of the burner and
resetting of the same as necessary.
- Cleanliness of the smoke side of
the heat exchanger.
This can be
done using swabs and vacuum clea-
ners to remove soot deposits on the
sides and fins used for exchanging
heat.
Alternatively specific chemical pro-
ducts can be used in compliance
with the instructions for use of the
same.
Do not use inflammable products
such as petrol, solvents or any
other such material to clean the
heat exchanger.
When working on the boiler for
the first time, check.
The declaration of conformity for the
plant.
- The plant handbook.
Also check:
- The suitability of the boiler room.
- The ventilation openings in the
room.
- The smoke evacuation flues, and
the diameters and lengths of these.
- That the boiler has been correctly
installed as per the instructions in
this booklet.
If the equipment is not able to
work correctly, or where it poses
any danger to people, animals or
property,
inform the person
responsible for the plant and
draw up a statement in this
regard.