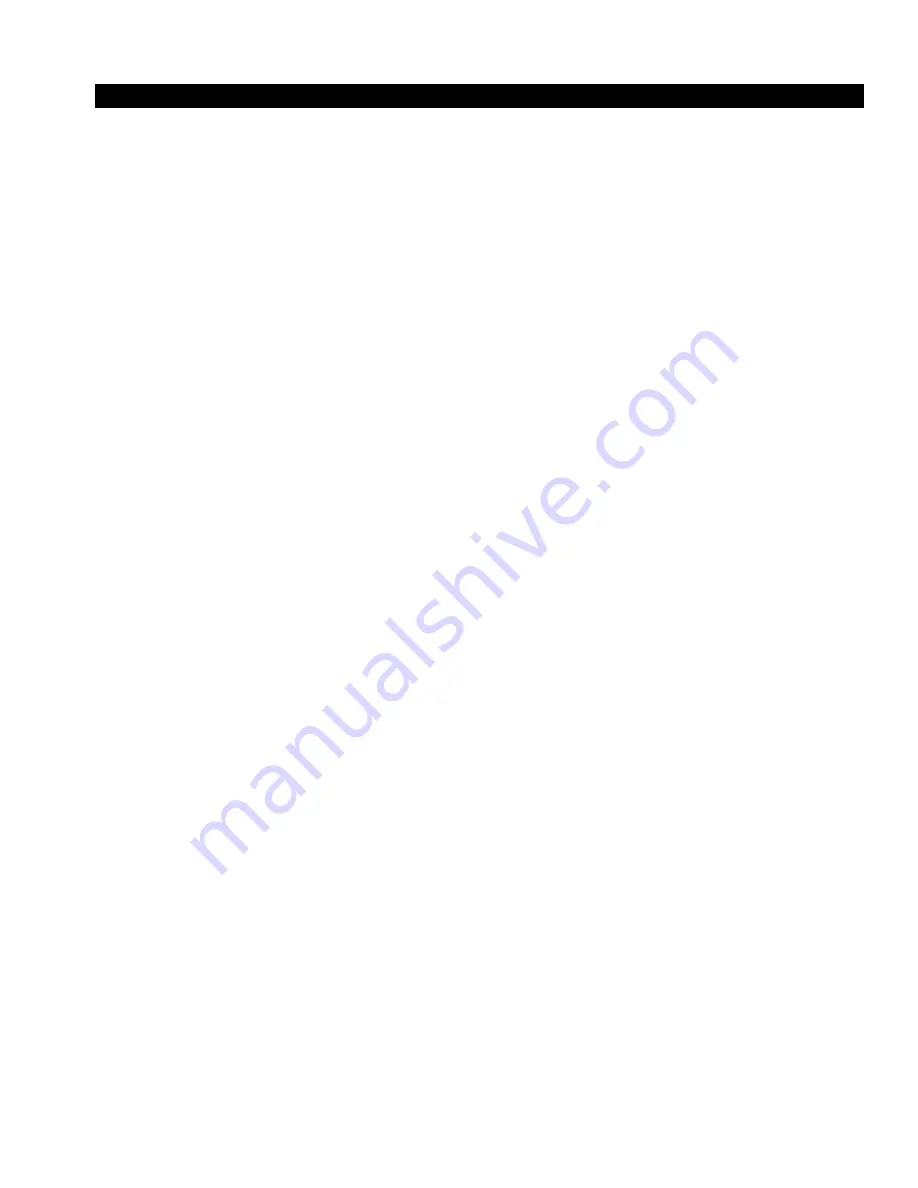
Turbo Stream
9
Installation and Operation Manual
CAUTION: All DOT, SAE or other applicable
standards must be followed when installing the
hydraulic system. Pay close attention to engine
and transmission manufacturer’s drive limitations.
Hydraulic Pump Drive Selection
The foam pump for the FoamPro Hydraulic Turbo
Stream system is powered by hydraulics. Power for
the system comes from hydraulic oil supplied by a
hydraulic pump attached to the apparatus engine. To
obtain optimum performance from the hydraulic motor-
driven foam pump, FoamPro has designed the Turbo
Stream system to use a constant volume hydraulic
motor. The customer-provided pump must provide the
proper hydraulic fluid flow with reduced heat load, torque
and horsepower requirements.
Oil Reservoir
A hydraulic reservoir will be required to be installed in
the apparatus. The recommended minimum reservoir
capacity is 8 gallons. A larger reservoir may be installed
and is recommended if the apparatus is to run at
maximum capacity for an extended period of time and to
allow air to settle out of the oil. The reservoir must have
a diffuser on the inlet to prevent entrapment of air into
the system. A particle screen, of 100 mesh, on the oil
inlet is recommended to help keep dirt out of the system.
A replaceable-type oil filter is recommended with at least
a 10 micron absolute rating. A baffle to separate the inlet
and outlet sections should be installed in the reservoir.
A vented, filtered breather of sufficient size to allow
filling of oil is required, and an oil drain is recommended.
A sight gauge, with thermometer, is also recommended
for easy checking of the oil level and to monitor oil
temperature. The oil reservoir should be mounted away
from heat sources, such as exhaust systems, and be a
location that allows easy access for checking and filling
the oil.
Oil Cooler
An oil cooler, capable of maintaining the temperature
of the hydraulic oil at 140° to 180°F (60° to 82°C),
is required. Use of an air-to-oil radiator-type heat
exchanger mounted on the apparatus should provide
adequate cooling for the hydraulic system oil. An electric
fan attached to the oil cooler permits mounting of the
oil cooler anywhere fresh air circulation is available.
A thermostat is required to be included for quick
warm-up of the oil in cold climates. The installer is
responsible to properly size the cooler. The required
cooling will be approximately 150 BTU/min. at 8 GPM.
Hydraulic Oil
Ratings and data for the FoamPro Hydraulic Turbo
Stream system are based on operating with premium
hydraulic fluids containing oxidation, rust and foam
inhibitors. These premium fluids include premium
turbine oils, API CD engine oils per SAE J183, M2C33F
or G automatic transmission fluids (ATF), Dexron (ATF)
meeting Allison C-3 or Caterpillar TO-2 requirements.
The recommended hydraulic fluid operating
viscosities are typically 70 to 278 SUS
(12 to 60 cSt) for optimum performance.
Hydraulic Hoses and Fittings
High pressure hydraulic hoses and fittings are to
be rated at 3000 PSI (207 BAR) minimum working
pressure. To reduce the potential for leaks at the
hydraulic fittings, use SAE 37° flare JIC-type fittings
or SAE straight thread o-ring fittings. On the Hydraulic
Turbo Stream, the motor inlet port is 7/8-14 UN-2B SAE
(J5145) o-ring straight thread. The outlet port is 1-1/6-12
UN-2B SAE (J5145) o-ring straight thread. Return line
pressure should not exceed 25 PSI.
9
Making Sure Everything is Working Right
SYSTEM CHECK
Check fuel level and oil level per engine manual prior
to running system. Check pump and gear case oil level
prior to running system. Pump and gear case should be
filled with oil per manual instructions.
Check the function of all components before using the
system. Also check that all plumbing and components
are tight and functional.
Check to see that water supply lines, strainers and foam
tank lines are free of debris and plumbed correctly. Any
leaks in the system will cause poor system performance
and operation.