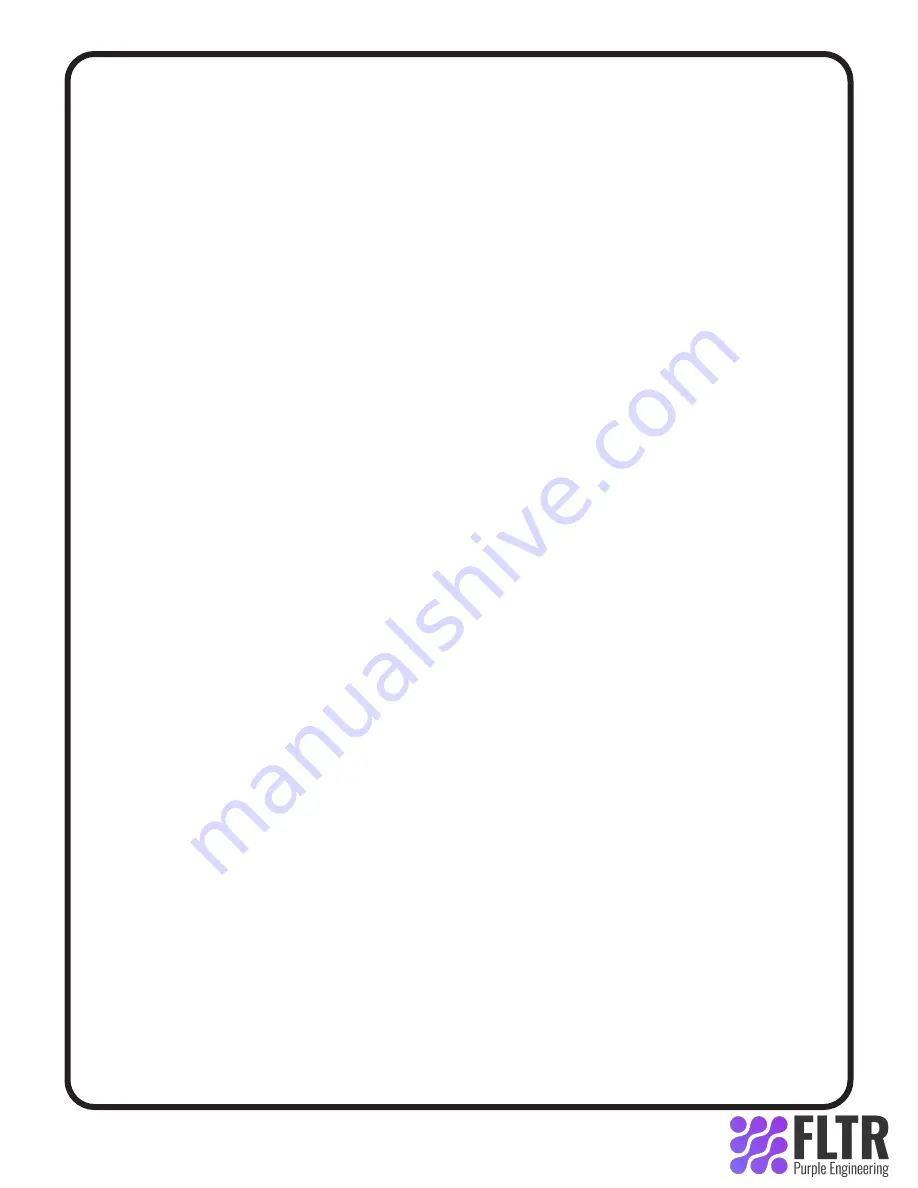
Using 1/8 - 1/4 inch diameter tubing:
1. Attach tubing to Port #1 on solenoid valve port and attach other end to
fitting on the bottom of flushing valve bonnet.
2. Attach tubing to Port #2 on solenoid valve port and attach other end to
an air or water supply source.
3. Attach tubing to fitting on clean water outlet and attach other end to fitting
on rinse controller marked “low pressure”.
4. Attach tubing to fitting on rinse controller marked “high pressure” and
attach other end to fitting on dirty water inlet.
Important Note: Do not run tubing more than three feet in length (preferably
two feet or less). Due to the pressure drop across the tubing, the
electronic rinse controller may not operate properly if tubing is too
long.
SECTION III
OPERATION AND ADJUSTMENTS
3.1 Start-Up
During the initial filling of the main pipeline, there may not be enough back
pressure downstream from filter to allow the cleaning cycle to function
properly. Therefore, it is necessary to install a valve on the outlet line to be
partially closed (e.g. gate valve, ball valve or butterfly valve).
If a downstream main line valve is partially closed, enough to provide 35 psi
on filter pressure gauges, the self-cycle will operate properly. Once the total
system is fully charged, the downstream valve can be adjusted as the system
requires, as long as 35 psi is maintained at the filter.
If systems are to come on automatically, it is advisable to install a flow control
or pressure sustaining valve downstream from the filters to create back
pressure on the filters in order to enable proper flushing while pipe lines are
being filled.
For more information:
WEB: FLTR.com.au PHONE: (+61) 1300 62 4020 EMAIL: [email protected] SKYPE: Purple.Engineering
Содержание OBF
Страница 1: ...OBF USERS MANUAL...
Страница 14: ...For more information WEB FLTR com au PHONE 61 1300 62 4020 EMAIL info FLTR com au SKYPE Purple Engineering...
Страница 15: ...For more information WEB FLTR com au PHONE 61 1300 62 4020 EMAIL info FLTR com au SKYPE Purple Engineering...
Страница 16: ...For more information WEB FLTR com au PHONE 61 1300 62 4020 EMAIL info FLTR com au SKYPE Purple Engineering...
Страница 17: ...For more information WEB FLTR com au PHONE 61 1300 62 4020 EMAIL info FLTR com au SKYPE Purple Engineering...
Страница 18: ...For more information WEB FLTR com au PHONE 61 1300 62 4020 EMAIL info FLTR com au SKYPE Purple Engineering...
Страница 19: ...For more information WEB FLTR com au PHONE 61 1300 62 4020 EMAIL info FLTR com au SKYPE Purple Engineering...
Страница 20: ...For more information WEB FLTR com au PHONE 61 1300 62 4020 EMAIL info FLTR com au SKYPE Purple Engineering...
Страница 21: ...For more information WEB FLTR com au PHONE 61 1300 62 4020 EMAIL info FLTR com au SKYPE Purple Engineering...
Страница 22: ...For more information WEB FLTR com au PHONE 61 1300 62 4020 EMAIL info FLTR com au SKYPE Purple Engineering...
Страница 23: ...For more information WEB FLTR com au PHONE 61 1300 62 4020 EMAIL info FLTR com au SKYPE Purple Engineering...