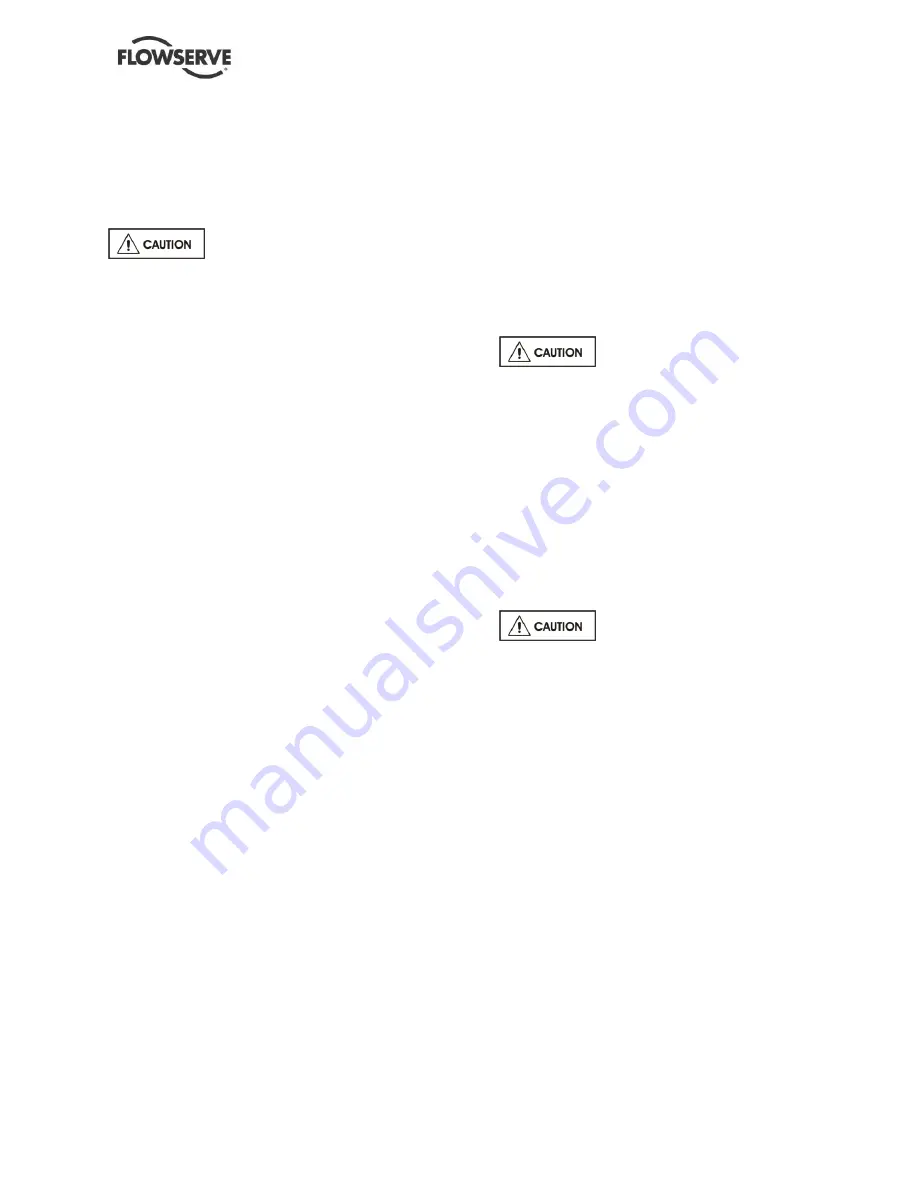
WIK USER INSTRUCTIONS ENGLISH BO2662 5/09
Page 58 of 76
3) See that requirements under visual inspection
(section 6.8.2.7.1) above which apply to wear
rings [1500] are in compliance with for new
ring.
4) See that temperature of parent part is above
21°C (70°F).
Do not bind or otherwise cause
undue stress on wearing ring [1500].
5) Sub-cool new wearing ring [1500] in dry ice to
shrink it; then, bottom ring squarely in bore of
parent part by using aluminum drift and mallet
to strike evenly around circumference of
wearing ring.
6) Determine that wearing ring [1500] and parent
part have warmed to ambient temperature by
feeling with hand.
7) If the replacement wearing ring [1500] has not
been furnished with finish stock left on the
running surface, then verify trueness of
wearing-ring-to-part fit as outlined below or by
an equivalent technique:
a) Set part face down on table of vertical
lathe and parallel with face of table.
b) Align centerline of part with centerline of
table using register face of part as true
side of dial indicator; alignment shall be
within limit given in section 10.3.
c) Clamp around part to hold it in centered
and parallel position.
d) Set up dial indicator to run on the inside
diameter of wearing ring [1500] and rotate
table; total runout shall not exceed
maximum given in section 10.3.
8) Install new wear ring locking keys [6700.3] and
tack weld them to metal of parent part using
gas-tungsten arc and appropriate wire. Note:
some installations use interference fit only to
secure ring. Then repeat step 7.
9) If the replacement wearing ring [1500] has
been furnished with finish stock left on the
running surface, true cut the wearing ring
[1500] using the following procedure, or an
equivalent:
a) Center the parent part on a vertical lathe
by following steps 7a through 7c above.
b) Machine the finish stock from the inside
diameter of the wearing ring [1500] to
meet the clearances specified in section
10.3.
10) Verify trueness of wearing-ring-to-part fit as
outlined in step 7 above.
11) See that there is no damage to the wearing
surface.
6.8.2.7.8
Replacing Bushings
These instructions apply to the replacement of
bushings [1610] in intermediate covers [1460] or
volutes. Unless the impeller [2200] hub wearing
surface has been, or is to be, ground down see
renewing impeller wearing surface (section
6.8.2.7.6) above, the standard size bushing [1610]
should be used for replacement. A bushing [1610],
whether standard or undersize, is manufactured to
be pressed into the parent part. The following
procedure will guide you in replacing a bushing
[1610].
Striking or cutting into metal of
parent part will make replacement necessary.
1) Machine off, or using rotary file grind off, welds
that wear ring locking keys [6700.3] to metal of
parent part or that retain bushing [1610]
directly to parent part.
2) Press out or using aluminum drift (or
equivalent), knock out bushing [1610].
3) See that requirements under visual inspection
(section 6.8.2.7.1) above which apply to
bushings [1610] are complied with.
4) See that temperature of parent part is above
21°C (70°F).
Do not bind or otherwise cause
undue stress on bushing [1610].
5) Sub-cool bushing [1610] in dry ice to shrink it;
then, bottom bushing,[1610] squarely in bore
of parent part by using aluminum drift and
mallet to strike evenly around circumference of
bushing [1610].
6) Determine that bushing [1610] and parent part
have warmed to ambient temperature by
feeling with hand.
7) If the replacement bushing [1610] has not
been furnished with finish stock left on the
running surface, then verify trueness of
wearing-ring-to-part fit as outlined below or by
an equivalent technique:
a) Set part face down on table of vertical
lathe and parallel with face of table.
b) Align centerline of part with centerline of
table using register face of part as true
side of dial indicator; alignment shall be
within limit given in section 10.3.
c) Clamp around part to hold it in centered
and parallel position.
d) Set up dial indicator to run on inside
diameter of bushing [1610] and rotate