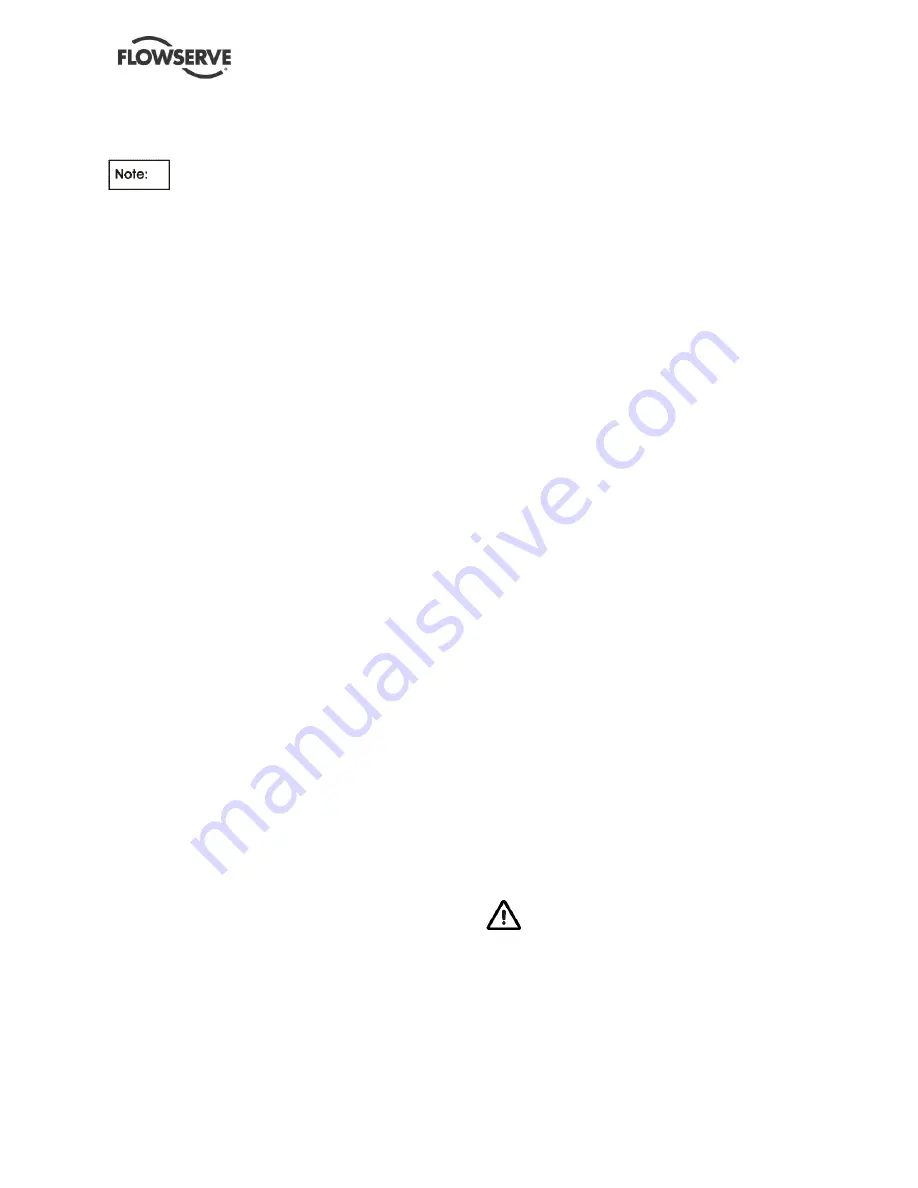
WIK USER INSTRUCTIONS ENGLISH BO2662 5/09
Page 33 of 76
pump; then clean and reinstall filter. Restart
auxiliary lube oil pump and continue flush.
To prevent an accumulation of moisture
from condensation when heated lube oil is used,
allow lube oil to cool gradually during last hour or
two of the cycle.
d) Shut down auxiliary lube oil pump at end of
20-hour cycle
5) Perform final phase of flushing cycle as follows:
a) Clean and reinstall filter
b) Start auxiliary lube oil pump and circulate
lube oil for another 4 hours, all the while
tapping the entire length of piping
c) Shutdown auxiliary lube oil pump and
recheck filter. If filter is even partially
clogged from any matter, clean and reinstall
filter and repeat second bullet point above
d) Repeat steps b and c above until filter is
clear of sludge, scale and the like, then
proceed to step 6
6) Drain lube oil piping reservoir and again clean
reservoir according to step 2 above. To prevent
entry of any dirt or foreign matter in reservoir,
install cover when cleaning is complete.
7) Using petroleum base solvent such as kerosene
or naphtha and clean cloth, swab inside of
lowest piping and piping with low spots.
8) Connect piping at all points.
9) Remove upper halves of bearing housing and
install inboard sleeve bearing, outboard sleeve
bearing, and thrust bearings according to
instructions under section 6.9.5.
10) Fill lube oil system to required level as instructed
in section 5.1.2.4 and/or section 5.1.2.5. Run
auxiliary lube oil pump until lines are full and
recheck reservoir.
5.2.4.2 Flushing lube oil system without using
auxiliary lube oil pump
The following flushing procedure applies where an
auxiliary lube oil pump is not available for use in
flushing the lube oil system. For illustrations of
piping and parts that are referred to in the procedure,
see lube oil piping and assembly drawings in the
back of this manual.
1) See that piping is disconnected from reservoir,
bearing housings, cooler, and filter; then tap
piping until all slag and scale loosens.
2) Using a clean swab soaked in a petroleum base
solvent such as kerosene or naphtha, swab
inside of each piping section; then follow up with
a clean dry swab. Verify that piping is free of
foreign material.
3) Connect piping at all points.
4) Operate pump (see section 5.7 and 5.8) for
approximately 2 hours and during this time,
periodically check differential pressure for an
indication of severe increase in differential
pressure. Should such increase occur,
immediately shut down pump (see section 5.9)
and check filter. If necessary, clean filter and
reinstall it; then complete run.
5) Remove, inspect, and clean inboard sleeve,
outboard sleeve, and thrust bearings (see
section 6.7.5, setion 6.8.1, section 6.8.2.1 and
section 6.8.2.3).
6) Drain, then clean lower halves of bearing
housings with a petroleum base solvent; do not
remove bearing housings.
7) Drain, then clean (or flush) with a petroleum
base solvent all of the following equipment that
is applicable to the lube oil system of your pump:
a) Lube oil cooler,
b) Reservoir,
c) Filter, and
d) Filter housing.
8) Install inboard sleeve, outboard sleeve, and
thrust bearings according to instructions under
section 6.9.5.
9) Operate pump (see section 5.7 and section 5.8)
for approximately 2 hours, and then shut it down
(see section 5.9). Check lube oil filter for sludge
and foreign matter such as scale and slag. If
filter is even partially clogged from any matter,
clean and reinstall filter; then repeat above steps
1 through 8: filter shall be clear of sludge, scale,
and the like before the pump is put on line for
extended operation.
5.3
Impeller clearance
Please refer to specification sheet section 10.3 for
those values.
5.4
Direction of rotation
For the direction of rotation refer to the General
Arrangement drawing
5.5
Guarding
Guarding is supplied and fitted to the pump
set. If this has been removed or disturbed ensure
that all the protective guards around the pump
coupling and exposed parts of the shaft are
securely fixed.