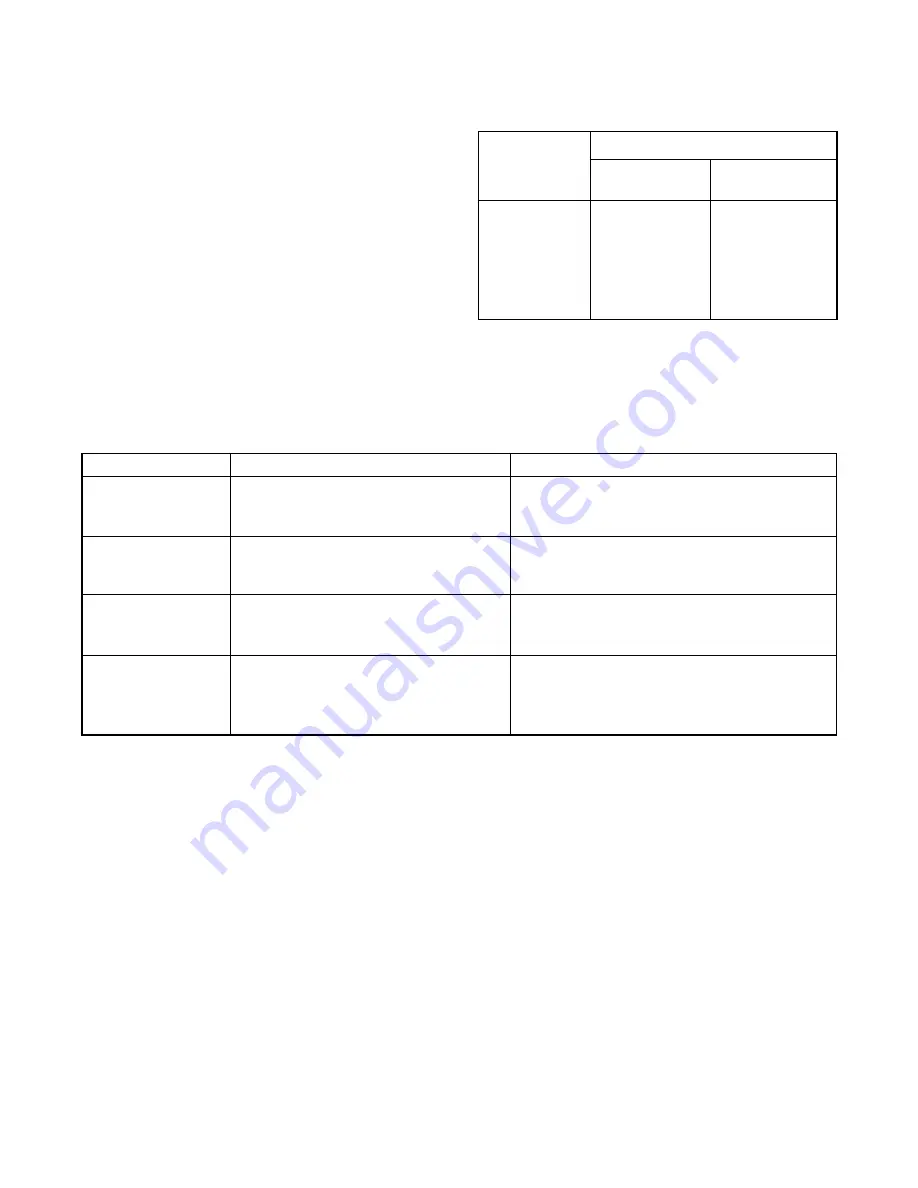
12-7
Troubleshooting Guardian II Metal Bellows Seals
Failure
Probable Cause
Corrective Action
Leakage through
1. Insufficient compression of bonnet
1. Tighten bonnet flange bolting until
bellows assembly
gasket
leakage stops
gasket
2. Worn or defective bonnet gasket
2. Disassemble and replace bonnet gasket
Leakage through
1. Failure of metal bellows seal
1. Disassemble and replace metal bellows
packing box or
assembly
seal assembly and all gaskets
“tell-tale” tap
Valve does not
1. Loose stem locknut on bellows stem
1. Disassemble, tighten stem locknut
seat or seats
2. Improper actuator stem
2. Correct stem engagement (refer to steps
too early
engagement
9 thru 12 in the “Reassembly” section)
Leakage through
1. Insufficient compression of gaskets
1. Tighten bonnet flange bolting until
bellows assembly
leakage stops
gasket
2. Worn or defective housing, bellows
2. Disassemble and replace all gaskets,
assembly or seat ring gasket
including seat ring gasket
then tighten the bolt directly opposite
1
/
6
-turn and
so on around the flange. Firmly tighten all bolts
evenly and completely to compress the bonnet
gasket and to seat the bonnet. Torque the bonnet
bolts to the suggested torque values in Table I.
14. Apply air over the piston to seat the plug. For all
throttling valves, adjust the stem clamp so that with
full instrument signal to the positioner the full signal
scribe line on the positioner cam points to the
center of the cam roller bearing.
Tighten the stem clamp bolting. Proper tightness is
important since this adjustment secures the actuator
stem to the bellows stem. Adjust the stroke plate so
that the stem clamp points to the “closed” position.
15. If the valve has been taken out of the line, make
sure the flow arrow indicates proper flow direction
upon reinstallation.
Table I: Suggested Bonnet Bolting
Torque Values (ft-lbs, +10 percent)
Bolt/Stud Material
Bolt
Size
Carbon
Stainless
(inches)
Steel
Steel
5
/
8
80
50
3
/
4
140
90
1
350
220
1
1
/
8
510
330
1
1
/
4
730
460
1
3
/
8
990
630
3. Loosen the actuator stem clamp.
4. Remove the packing box bolting.
5. Remove the yoke clamps.
6. Remove the actuator by turning it completely off
the bellows seal bonnet and bellows seal stem.
CAUTION: Although the valve incorporates an
anti-rotation pin, care should be taken not to
put excessive torque on the plug stem/bellows
assembly. Excessive torque can damage bel-
lows and/or shear the anti-rotation pin.
7. Remove the bolting from the upper housing clamps
or flanges.
WARNING: If there has been a bellows failure,
process fluid may be trapped in the bellows
seal bonnet; therefore, be extremely cautious
when removing the upper housing bolting.
FORMED METAL BELLOWS SEAL
Disassembling Formed Metal Bellows Seal
To disassemble the formed metal bellows seal, refer to
Figures 4 and 5 and proceed as follows:
WARNING: Depressurize line to atmospheric pres-
sure, drain all process fluids and decontaminate
the valve (if toxic or hazardous materials are
present). Failure to do so can cause serious injury.
1. Remove the bonnet flange bolts or nuts.
2. Remove the entire actuator/bellows seal assem-
bly, plus the bonnet and plug, by lifting them
straight out of the body.
CAUTION: Heavy assemblies may require a
hoist. A lifting ring is provided on most actua-
tors for this purpose; otherwise, lift by the yoke
legs using lifting straps and the hoist.