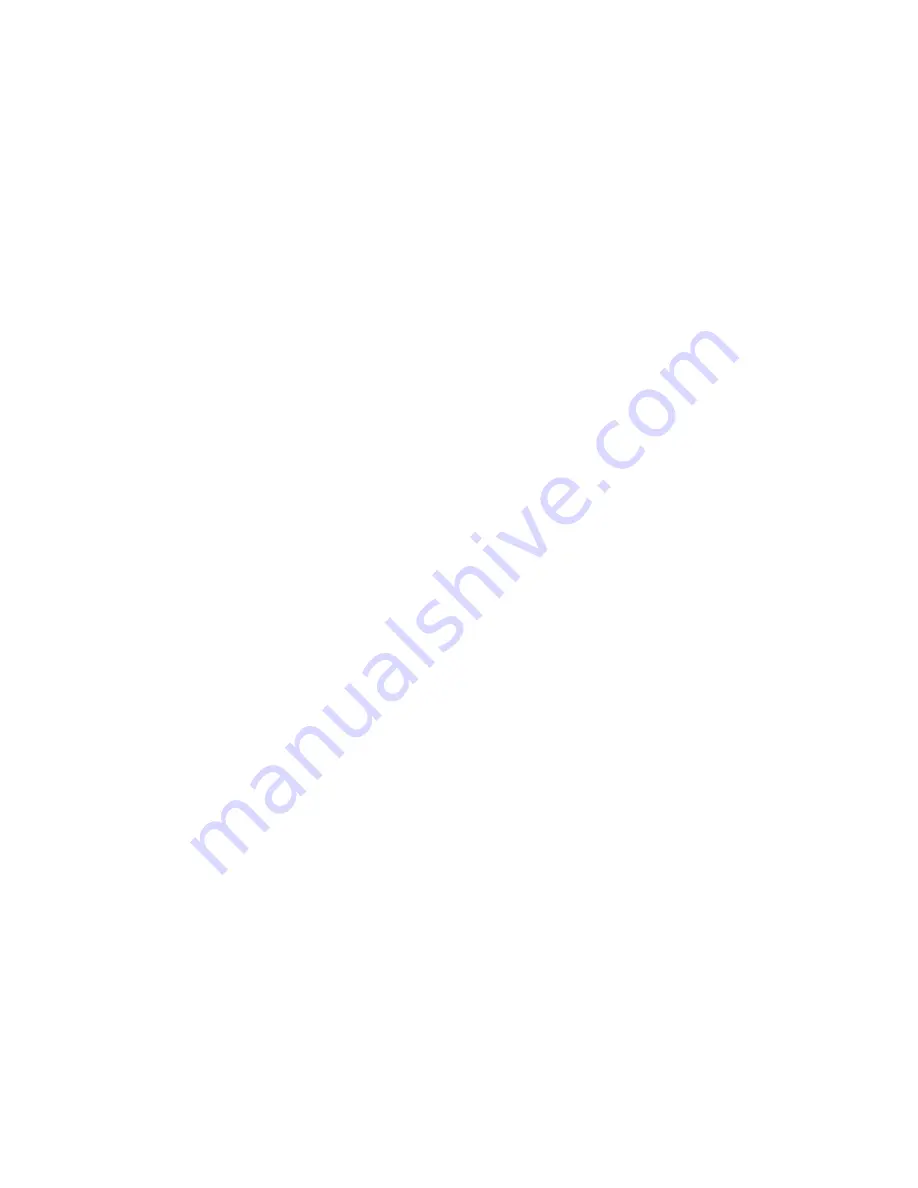
12-3
8. Remove the bonnet flange, then carefully slide the
plug/bellows assembly out of the bonnet without
stretching the bellows. Be careful not to lose the anti-
rotation pin from the plug/bellows assembly. The
packing, packing spacer and stem guides can now
be removed for inspection or replacement.
Reassembling Guardian Metal Bellows Seal
To reassemble the Guardian metal bellows seal, refer
to Figure 1 and proceed as follows:
1. Check metal bellows for signs of wear or damage.
If the bellows shows signs of fatigue or cracking,
obtain a replacement before reassembling and
operating the valve. Make sure all gasket surfaces
are clean and free of damage.
2. If the packing has been removed, replace packing,
packing spacer and stem guides (refer to Figure 1).
3. Insert the plug stem into the bonnet.
4. Place the bonnet flange on the bonnet.
5. Place the gland flange over the plug stem and the
stem clamp on the actuator stem and reinstall the
actuator assembly by screwing it onto the plug
stem. Three or four plug stem threads should be
exposed below the actuator stem to ensure proper
seating.
CAUTION: Although the valve incorporates an
anti-rotation pin, care should be taken not to put
excessive torque on the plug stem/bellows as-
sembly. Excessive torque can damage bellows
and/or shear the anti-rotation pin.
6. Insert the seat gasket, seat ring and seat retainer
into the body; then install the sleeve gasket and
metal bellows sleeve.
7. Install the seal ring gasket and the bonnet gasket.
8. Retract the plug and carefully lower the bellows/
bon-net assembly into the sleeve. Make certain the
anti-rotation pin is in place before installing the
bellows.
WARNING: Care should be taken not to damage
the bellows or plug and seat ring seating sur-
faces when installing the bellows. Damage to
the bellows may cause faulty operation and/or
injury to personnel.
9. On air-to-close valves, leave three or four threads
exposed. For correct plug engagement on air-to-
open valves, make certain the plug does not rotate
in the body/bonnet assembly and screw the actua-
tor assembly onto the plug as far as possible.
WARNING: Rotation of the plug while clamped
in the body/bonnet assembly will damage the
bellows seal, which could cause personal
injury.
10. Apply air pressure above the piston to drive it to the
bottom of the actuator cylinder. Without rotating the
plug, back the actuator assembly off of the plug
stem until there is
1
/
32
- inch gap between the bottom
of the yoke and bonnet. Then back the actuator
assembly off of the plug stem exactly one complete
turn. This provides the correct seating force.
11. Apply air below the actuator piston, retracting the
plug. Install the yoke clamp.
12. To properly align the seat ring and plug, first bring
the bonnet bolting to finger tightness. Apply air
above the piston to seat the plug in the seat ring.
NOTE: Step 12 applies only to valves with pneu-
matic actuators. If an hydraulic or mechanical
actuator is used, return the plug to the midstroke
position and proceed to tighten.
WARNING: Failure to return the plug to the
midstroke position (mechanical or hydraulic
actuators only) will cause damage to the actua-
tor and/or the valve during the bonnet tighten-
ing sequence. This is due to the inability of
most mechanical/hydraulic actuators to ac-
commodate the
1
/
16
- inch back driving during
the tightening sequence.
13. With the plug in the extended (or closed) position,
tighten two opposing bonnet flange bolts or nuts
1
/
6
- turn (one flat). Tighten each bonnet bolt in this
manner until the bonnet, seat, sleeve and seal ring
gaskets are compressed and the bonnet, sleeve
and body are seated metal-to-metal.
CAUTION: Undertightening may not fully com-
press the gaskets, which may cause leakage.
Overtightening may damage interior parts.
Tighten only to the point that metal-to-metal
seating occurs.
14. Remove air from the actuator. Adjust the positioner
cam and stem clamp according to instructions con-
tained in the appropriate positioner maintenance
bulletin. Then adjust the stroke plate to indicate
proper air-action (air-to-open valves should be ad-
justed so the stem clamp points to “closed” on the
stroke plate; air-to-close valves should point to
“open”).
15. Install the packing box bolting. Packing box bolting
should be slightly more than fingertight when Teflon
packing is used.
CAUTION: Do not overtighten packing. Over-
tightened packing can cause high stem friction
and excessive packing wear, which may im-
pede stem movement.
16. Stroke the valve and check for smooth, trouble-free
operation.