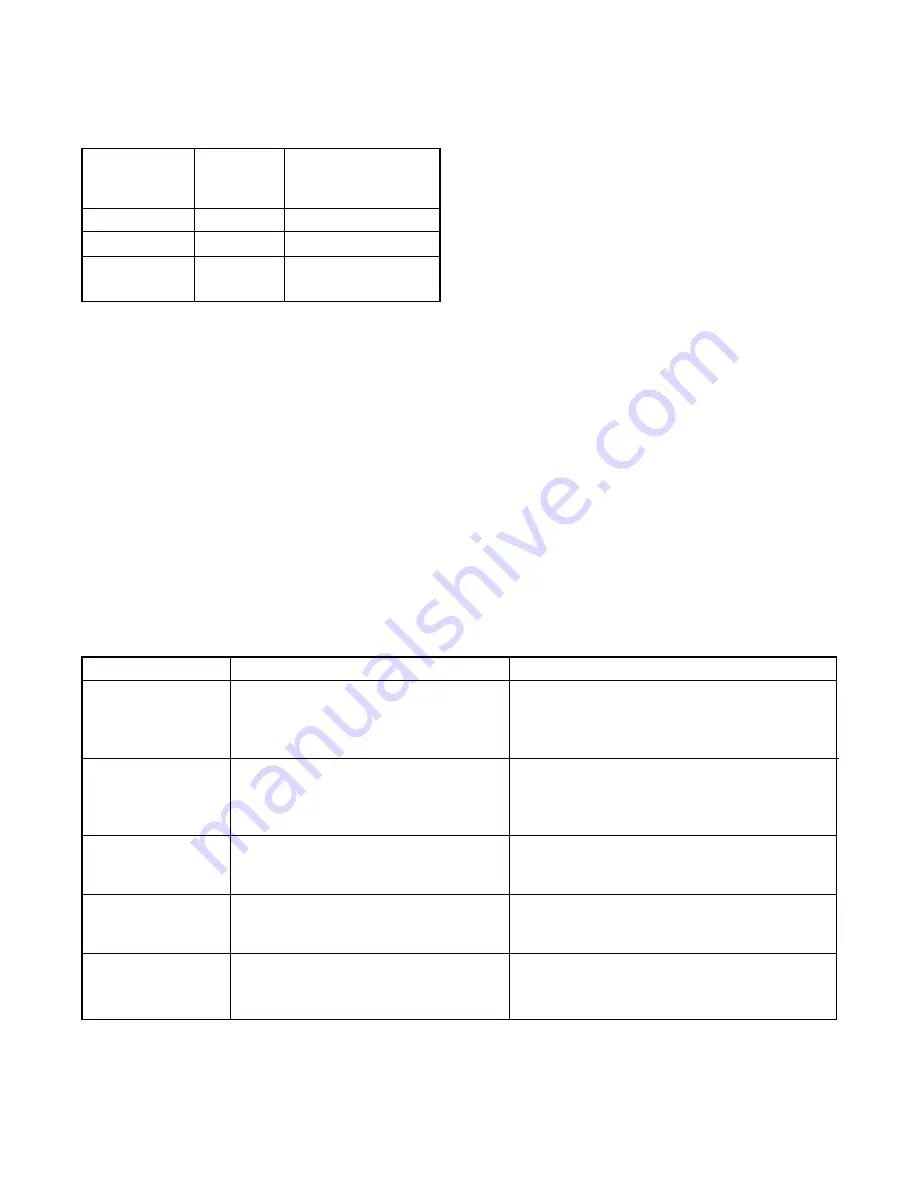
12-11
Table II:
Extended Plug to Bonnet Dimensions
(refer to Figure 5)
Valve Size
Stroke
Distance Between
(inches)
(inches)
Extended Plug
and Bonnet
1
/
2
,
3
/
4
, 1
1.00
1.03
1
1
/
2
, 2
1.50
1.56
3, 4, 6
2.50
2.56
(class 150)
19. Install the entire actuator/bellows seal subassem-
bly into the valve body. Tighten the bonnet flange
bolting finger-tight.
20. Apply air pressure over the piston while exhausting
the other side to seat the valve. Tighten two
opposing bonnet flange bolts or nuts
1
/
6
- turn (one
flat). Tighten each bonnet bolt in this manner until
the bonnet bottoms metal-to-metal in the body.
This can easily be felt through the wrench.
21. Release the air in the cylinder. Firmly tighten the
upper and lower housing clamps or flanges by
tightening two opposing bolts, so that even pres-
sure on the gasket and proper alignment of the
housing and body bonnet are maintained.
22. Adjust the stem clamp to the correct position ac-
cording to the air action (air-to-open valves should
be adjusted so that the stem clamp points to
“closed” on the stroke indicator plate; air-to-close
valves should point to “open”).
23. Attach the packing box bolting and tighten the
packing box nuts to slightly over finger-tight.
CAUTION: Do not overtighten packing. This
can cause excessive packing wear and stem
friction which may impede stem movement.
24. Stroke the valve and check for smooth operation.
Troubleshooting Formed Metal Bellows Seals
Failure
Probable Cause
Corrective Action
Leakage through
1. Insufficient compression of housing
1. Tighten flanges or clamps until leakage
lower housing
gasket
stops
clamps or flanges
2. Worn or defective lower housing
2. Disassemble and replace lower housing
gasket
gasket
Leakage through
1. Insufficient compression of seal ring
1. Tighten flanges or clamps until leakage
upper housing
gaskets
stops
clamps or flanges
2. Worn or defective upper seal ring
2. Disassemble and replace upper seal
gaskets
ring gaskets
Leakage through
1. Insufficient compression of bonnet
1. Tighten bonnet flange bolting until
bonnet gasket
gasket
leakage stops
2. Worn or defective bonnet gasket
2. Disassemble and replace bonnet gasket
Leakage through
1. Failure of metal bellows seal
1. Disassemble and replace metal bellows
packing box or
assembly
seal assembly and all gaskets
“tell-tale” tap
Valve does not
1. Loose stem locknut on plug stem
1. Disassemble, tighten stem locknut
seat or seats
2. Improper actuator stem
2. Correct stem engagement (refer to steps
too early
engagement
15 and 16 in the “Reassembly” section)
16. For correct stem engagement on air-to-close valves,
a check valve must be used to lock air into the top
of the actuator. This puts the actuator stem in the
extended position. Turn the actuator stem onto the
bellows seal stem until about
1
/
16
-inch of space is
left between the bottom of the yoke and the shoul-
der of the bellows seal bonnet. Carefully exhaust
the check valve and the yoke will come into contact
with the bonnet. This will provide the proper clear-
ance between the piston and the top of the yoke.
17. Attach the yoke clamps.
18. Using new seat and bonnet gaskets, replace the
seat ring and seat retainer in the body.