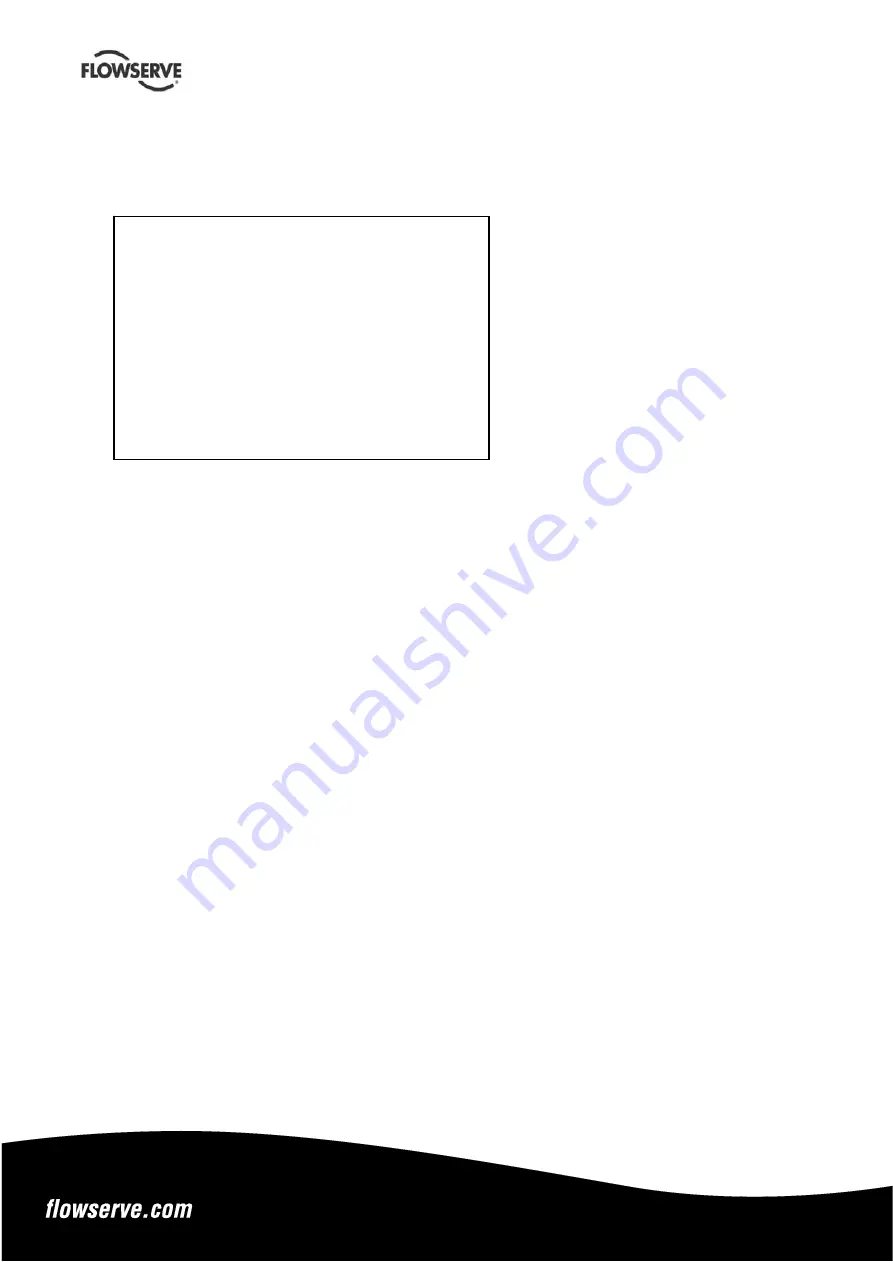
ERPN-M USER INSTRUCTIONS ENGLISH 02-08
Page 37 of
Your Flowserve factory contacts:
Flowserve (Austria) GmbH
Industriestraße B6
2345 Brunn am Gebirge
Austria
Telefon: +43
2236
31530
Fax:
+43 2236 377 540
Service & Repair Fax:
+43 2236 31582
E.mail:
FLOWSERVE REGIONAL
SALES OFFICES:
USA and Canada
Flowserve Corporation
5215 North O’Connor Blvd.,
Suite 2300
Irving, Texas 75039-5421 USA
Telephone 1 972 443 6500
Fax 1 972 443 6800
Europe, Middle East, Africa
Worthing S.P.A.
Flowserve Corporation
Via Rossini 90/92
20033 Desio (Milan) Italy
Telephone 39 0362 6121
Fax 39 0362 303396
Latin America and Caribbean
Flowserve Corporation
6840 Wynnwood Lane
Houston, Texas 77008 USA
Telephone 1 713 803 4434
Fax 1 713 803 4497
Asia Pacific
Flowserve Pte. Ltd
200 Pandan Loop #06-03/04
Pantech 21
Singapore 128388
Telephone 65 6775 3003
Fax 65 6779 4607