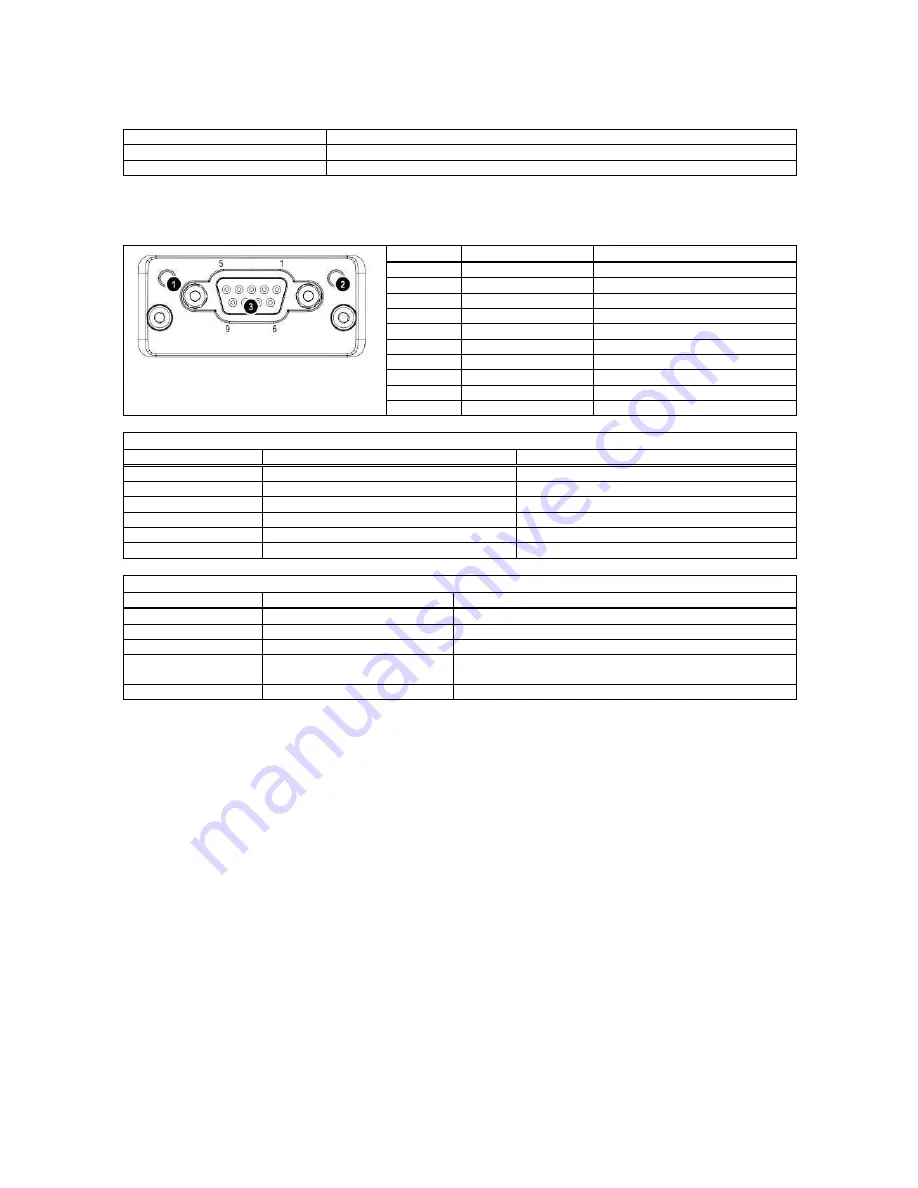
FT-13 Technical Manual, Rev. 1.40 March 2013
Page 42 of 56
8.7 CANopen Option
Indicators which are equipped with the CANopen option can be connected to a PLC bus as described below.
Baud rate
Automatic (10 kbps to 12 Mbps)
Update rate
Weight data will be updated each 40 ms
Response time on entries
5 ms to 25 ms
8.7.1 Electrical Connections
The pin configuration of the male 9-pol D-Sub ProfiNet connector (DB9M) is described in the table below:
1. Run LED
2. Error LED
3. CANopen Connector
Pin no.
Signal
Description
1
2
CAN_L
3
CAN_GROUND
4
5
CAN_SHIELD
6
7
CAN_H
8
9
Housing
Shield
Run LED
State
Indication
Action / Comment
Off
No power or not initialized
No power or cable broken
Green
On-line, data exchange
Green, flashing
On-line, initializing
Green, single flash
Stopped
Check for hardware damages
Green, flickering
Auto baud rate detection in progress
Red
Exception error
Check EDS file
Error LED
State
Indication
Action / Comment
Off
No error
No power or CANopen module is inizializing
Red, single flash
Warning limit reached
Bus error counter reached or exceeded its warning limit
Red, flickering
LSS
LSS services in progress
Red, double flash
Error count event
A guard (NMT slave or master) or heartbeat event has
occured
Red
Bus off (fatal event)
Bus off
8.7.2 Setup
[0--] Interface Block
[03-] CANopen
This sub-block includes the parameters of the CANopen.
[034 X ] Data Format
0 : Signed 32 bit integer
1 : Signed 32 bit floating point
[035 XX] Address
The address of the instrument will be entered via numerical keypad. Value range is 1 to 127. After editing
the address it is required to restart the instrument.
After the setup of these parameters and the hardware connection as described above, the data interface can
be used as described in Appendix 5.
Important hint:
During the setup the CANopen output (weight value and status bits) will not be updated.
8.7.3 Data Structure
See Appendix 5.