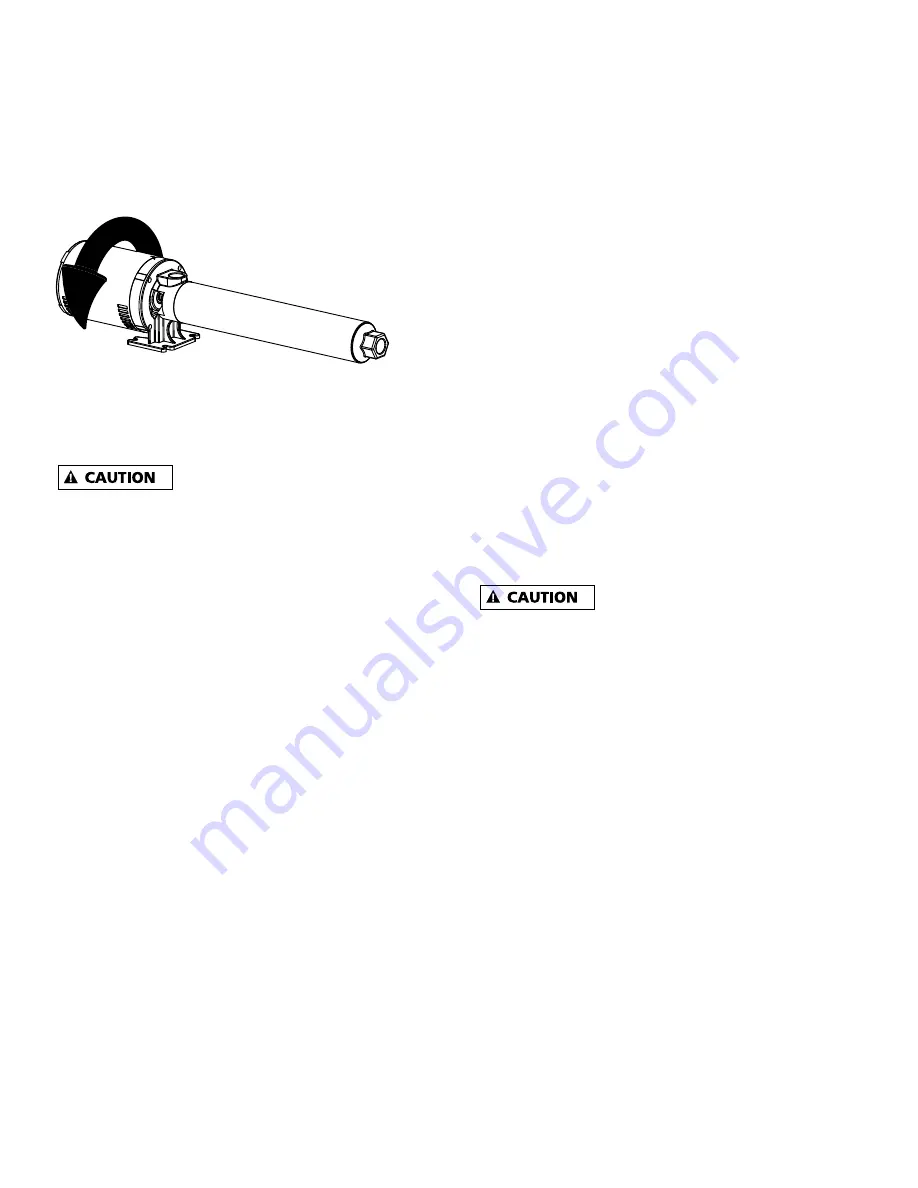
10
© 2020 FLINT & WALLING, INC. • 95 North Oak St. • Kendallville, IN 46755
flintandwalling.com
Operation (Continued)
START - UP PROCEDURE
Once the preceding instructions have been completed, the
pump can be started.
1. During the first few hours of operation, inspect the pump,
piping and any auxiliary equipment used in connection with
the unit.
2. Check for leaks, excessive vibration or unusual noises.
Figure 15 - Correct Motor/Pump Rotation (all units)
NOTE:
See rotation arrow on inlet casting.
IL1825
Maintenance
Disconnect power supply and depressurize
system before servicing pump or removing
any component.
ROUTINE
Pump should be checked routinely for proper operation.
Replace or clean all filters and line strainers on a regular basis.
DRAINING
This pump cannot be completely drained because of internal
design. Most of the liquid can be drained by tilting the discharge
forward after removing discharge casting; or, the liquid can be
drained through the inlet port. Store in heated areas.
CLEANING
If used for spraying insecticides, pump should be thoroughly
flushed with clean water after using.
LUBRICATION
The motor has prelubricated bearings. No lubrication is
required.
SERVICING THREE-PHASE UNITS
Loctite (thread sealer) is used on the threads between the motor
shaft and the pump shaft coupling. When reassembling, reapply
thread sealer.
PUMP DISASSEMBLY
To disassemble the pump, refer to the exploded parts view and
Figures 16, 17 & 18
Tools Required:
• Block of wood (2” x 4” x 12”)
• Piece of 3/4” pipe (12” to 24” long)
• Pipe wrench
• Strap wrench
• 1/4” Dowel rod (about 24” long)
• 9/16” Open end wrench
• 3/8” Open end wrench
1. To stabilize pump during disassembly, place block of wood
underneath pump barrel.
2. Thread pipe into pump inlet port. This acts as a handle.
3. Using the pipe wrench, remove the discharge head, turning
CCW (counter clockwise).
4. With the strap wrench, loosen the barrel, turning CCW
(counter clockwise). DO NOT use pipe wrench on pump
barrel.
5. Holding the impeller stack in place, position pump in upright
position, standing unit on the motor end cover.
6. Use the 1/4” dowel rod to hold the stages down and in
place on the pump shaft. Remove pump barrel.
7. Slide the stages off the pump shaft onto the 1/4” dowel rod.
Leave stages on rod and carefully set aside.
NOTE:
There may be some small .010” shim washers located
next to the pump shaft coupling. Keep these shims for
re-assembly.
8. Through the side opening of the mounting frame, hold
the motor shaft with 9/16” wrench. Remove the shaft and
coupling from the motor using the 3/8” wrench on the hex
shaped pump shaft.
NOTE
: If the hex shaft comes free, leaving the coupling
attached to the motor, use vise grips to free the coupling.
MECHANICAL SEAL REPLACEMENT
1. Follow instructions under “Pump Disassembly”.
2. Remove the mechanical seal assembly.
a. The rotary portion of the seal assembly (carbon ring,
Buna-N gasket and spring will slide easily off the end of
shaft).
b. Using two (2) screwdrivers, pry the ceramic seal and rubber
gasket from the recess of the mounting ring
(See Figure 16).
The precision lapped faces of the
mechanical seal are easily damaged. Handle
the replacement seal carefully. Short seal life will result if seal
faces (ceramic & carbon) are nicked, scratched or dirty.
3. Clean the seal cavity of the mounting ring and the motor
thoroughly.
4. Wet outer edge of rubber cup on ceramic seat with liquid
soap solution. Use sparingly (one drop only).
NOTE:
Liquid soap solution - one drop of liquid soap combined
with one teaspoonful of water.
5. With thumb pressure, press ceramic seal half firmly and
squarely into seal cavity. Polished face of ceramic seat
is up. If seal will not seat correctly, remove, placing seal
face up on bench. Reclean cavity. Seal should now seat
correctly (See Figure 17).
6. If seal does not seat correctly after recleaning cavity, place
a cardboard washer over polished seal face and carefully
press into place using a piece of standard clean 3/4” pipe
as a press (See Figure 18).