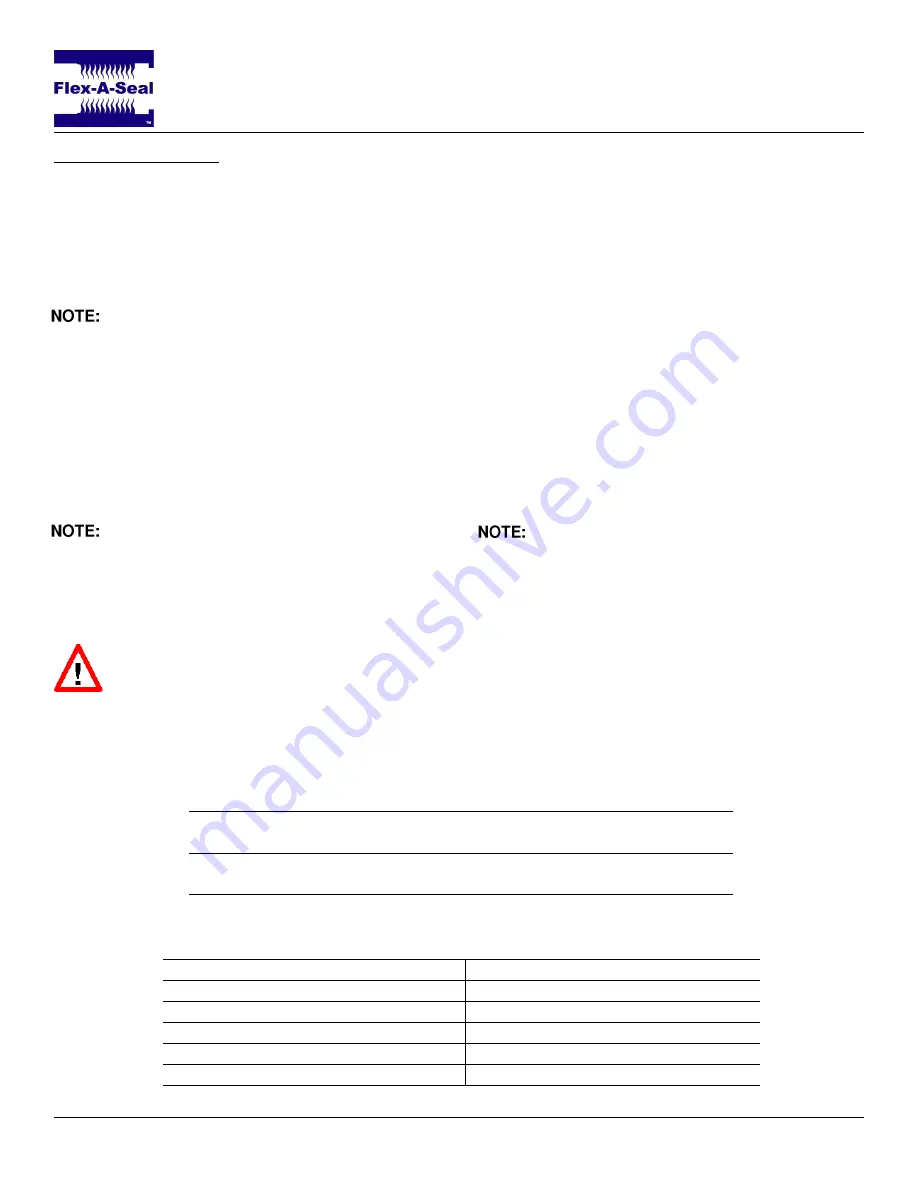
Installation, Operation & Maintenance Guide
Style 79
SEAL INSTALLATION
Style 79 double cartridge seals entail the same
simple installation procedure as other Flex-A-Seal
cartridge seals. Ensure alignment verification of
equipment has been completed prior to starting the
installation procedure. Reveiw engineering prints for
special notes and/or instructions.
•
It is essential to use a suitable lubricant
when installing a seal, as different
lubricants will work better with different
elastomers.
1
. Disassemble the pump until the seal chamber
and shaft are accessible.
2
. Remove the seal from its packaging and
inspect for damage to any components and
seal faces.
Cartridge seals are shipped from
Flex-A-Seal fully assembled and should not
be disassembled without cause. If a seal
appears damaged prior to installation,
contact a Flex-A-Seal representative.
Grease, scratches, or nicks on the seal
faces may cause leakage.
3
. Ensure the shaft and seal housing have been
properly cleaned as described in the
preparation section.
4
. Lightly lubricate the seal sleeve O-ring with a
suitable and compatible lubricant.
5
. Gently slide the seal on the shaft with the gland
gasket facing, but clear of the seal chamber.
6
. Reassemble the pump as described by the
pump OEM.
7
. If the gland is equipped with a gland gasket,
lubricate gland bolts and bolt the gland to the
seal chamber using the Legacy Method (Star
Pattern) according to torque values specified in
the table below. Be sure not to overtighten the
gland bolts as this may distort the gland and
internal components resulting in seal leakage.
For mechanical seals with a register fit or a
metal-to-metal mate with the seal chamber,
standard torque-tension specifications for
bolts and studs is sufficient.
8
. Alternately tighten the provided set screws to
the specified torque value according to the
table below.
9
. Remove the setting clips from the seal. Save
these for future use in seal removal or impeller
adjustment.
Torque Rating for Cartridge Seal Gland Bolts (Flat Gasketed Gland)
Shaft Size
1.000–2.000 in.
24–50 mm
2.125–3.250 in.
53–80 mm
3.375–4.000 in.
85–100 mm
Recommended
Torque
20 ft-lbs.
27 N-m
25 ft-lbs.
34 N-m
30 ft-lbs.
41 N-m
Cup Point Set Screw Torque Specifications
Screw Size
Alloy Steel
Stainless
Screw Size
Alloy Steel
Stainless
#10
36 in.-lbs.
26 in.-lbs.
M4
2.0 N-m
1.5 N-m
1/4
87 in.-lbs.
70 in.-lbs.
M6
7.9 N-m
6.1 N-m
5/16
165 in.-lbs.
130 in.-lbs.
M8
19.6 N-m
15.4 N-m
3/8
290 in.-lbs.
230 in.-lbs.
M10
37.0 N-m
29.5 N-m
1/2
620 in.-lbs.
500 in.-lbs.
M12
60.3 N-m
48.3 N-m
Page 4 of 7