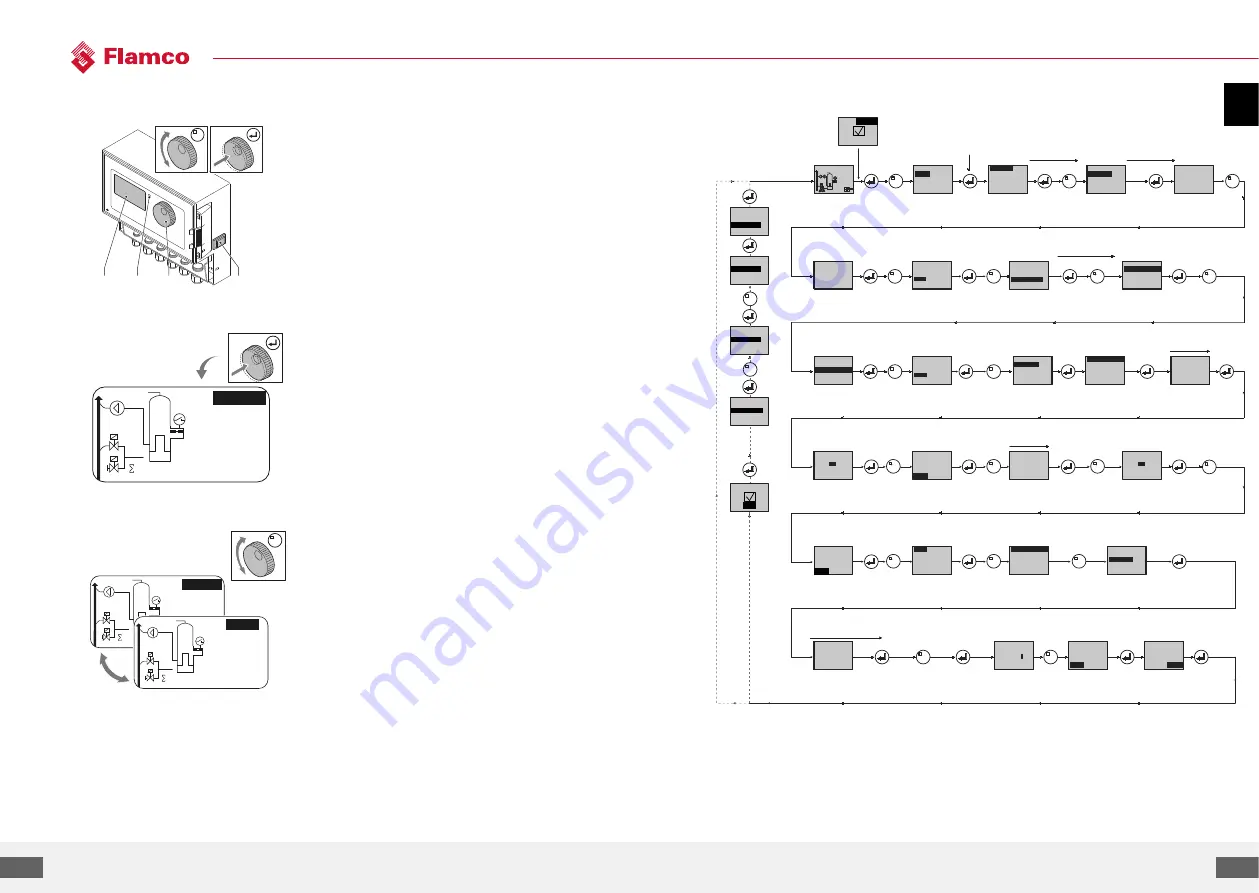
We reserve the right to change designs and technical specifications of our products.
Manual ENA 7-30
17
16
ENG
6.3 Working principle controller
A
B
C
D
-h Turbo
--- bar
P
------
---
--:--
2 sec...
System
Start
Liter
-h Turbo
--- bar
p
------
---
--:--
-h Turbo
--- bar
P
------
---
--:--
System
Start
Fehler
Start
Liter
Start up
• Switch off an installed refill equipment.
Close the inflow valves.
• Switch on the controller (D).
A Display
B Error LED
C Navigation wheel
D ON/OFF switch controller
Use the navigation wheel (C) to navigate
through the menus an to confirm the input.
The display (A) shows the menus. In case of
errors the error LED (B) is on.
• Hold down the navigation wheel for two
seconds to
go to the process display, whatever the cursor
position.
* Turbo = Fast
• In case of errors the process display switches
from [SYSTEM] to [ERROR] and the LED is on.
• The error messages, minimum water level,
minimum pressure alarm are consistent by the
first start of opertion.
• It is possible to turn the wheel to switch
between [SYSTEM] and [ERROR].
• When [ERROR] is displayed press the wheel
to go to the error list. In case of more than one
error, scroll through the errors. All errors are
shown in accordance of appearance.
• When [SYSTEM] is displayed, press the wheel
to go to the option menu.
* Turbo = Fast
6.4. Controller inputs
B
2
System
G5 3
D
1
Hardware
Parameter
Service
Back
F5
5
Back
G
2
ID number
Language
Litres counter
V iew
Back
Water treatment
Level controlled
Back
G2
1
Deutch
Nederlands
English
Français
F
5
System pressure
Special syst.press
Litre/pulse
Water treatment
G 2
19
Dansk
Suomi
Maggar
Back
G2
7
Polski
Dansk
Suomi
Maggar
F
10
Water treatment
Filling quantity
Time, date
Other
G
5
Language
Liters counter
Water treatment
Control mode
F5
Fillcommand on
D
2
Hardware
Parameter
Service
Back
X,x bar
Fillcommand on
Save Back
X,x
bar
X,x
X,x
Save
19.05.07
10:15:28
Save Back
30.07.07
13:36:0
0
Save Back
30.07.07
13:36:00
Back
Back
30.07.07
13:36:00
Save
1
Start
Back
Press. controlled
Level controlled
G5 4
2
X,x bar
Fillcommand o ff
F5
X,x
X,x
bar
X,x
Fillcommand on
X,x
X,x
bar
Save Back
Fillcommand o ff
Fillcommand o ff
Save
Back
X,x bar
X,x
X,x
Water treatment
Litre/pulse
Special syst. press
F
5
Maintenance
Software version
Projekt no.
E
3
G
10
Sensor
Motor prot.
Common failure
Back
Press . c ontrolled
Start
System
D
3
Hardwaremenu
Parametermenu
Back
Servicemenu
Back
Start
Date Time
Ku1
E3 2
E3 1
Ku1
Date Time
Back
Start
Save
Back
X,x
Enter
System
Start
System pressure
(3 sec.)
Code
"000001"
Sprachein-
stellung
Sprache
Steuerungsart
Einschaltdruck
Nachspeisung
Abschaltdruck
Nachspeisung
Menü
(nur beim
ersten Mal)
Zeit und Datum
(3 sec.)
•
When entering the program mode, the control for pressure maintenance is active.
•
The code will be active 5 minutes after latest input.
•
Remove all unpermitted loads, supported objects or lateral loads from the basic automat.
•
When the programming procedure is completed, the electrical parts of the ENA are ready for
operation.