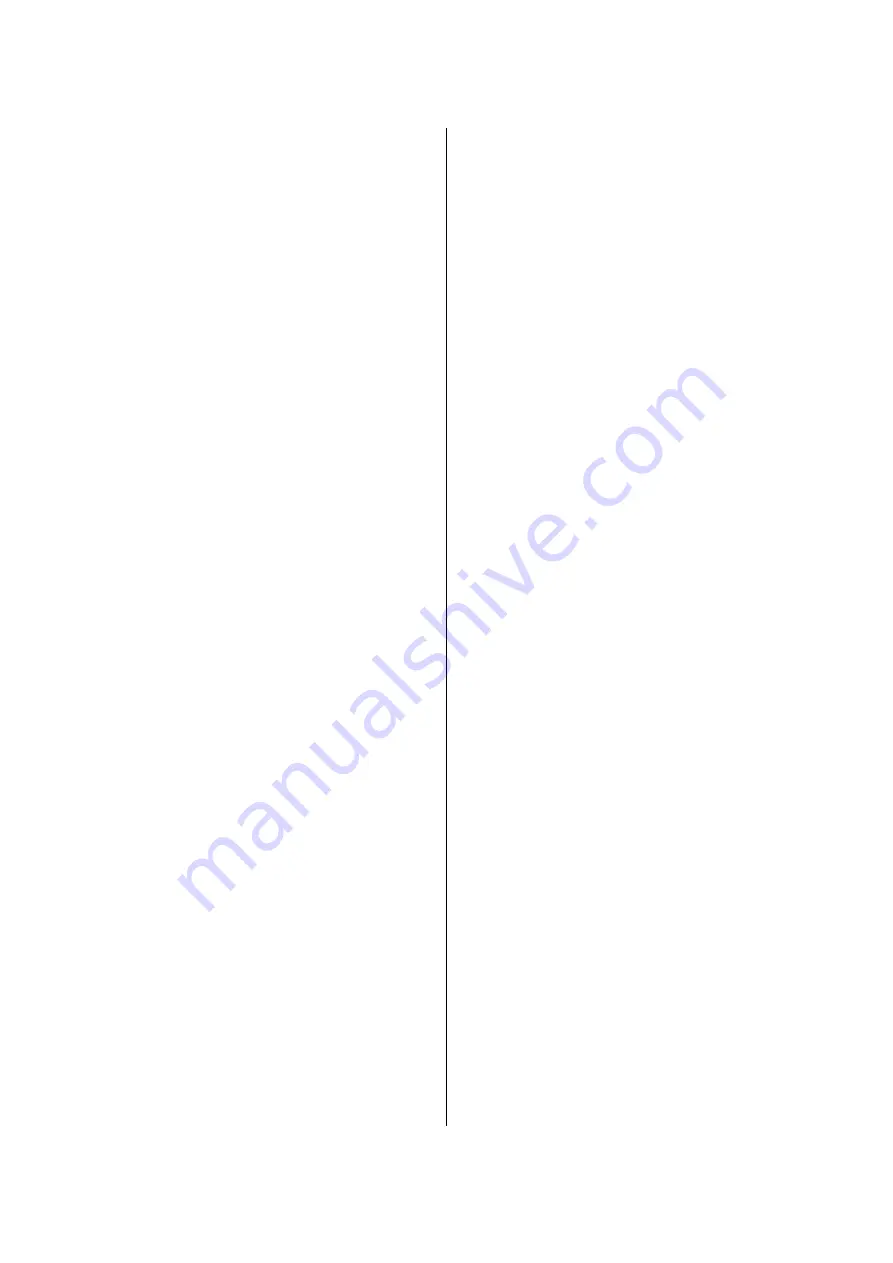
FL
AIR
MO ApS
–
Lundeborgvej 3
–
DK-9220 Aalborg
–
Denmark
Phone: +45 53717220 Web: www.flairmo.dk - E-mail: [email protected]
the fan may rotate in the wrong direction and the motor will
not be cooled. Consequently, the fan will not cool the motor
efficiently, causing a shorter lifetime of the compressor, and
invalidating warranty.
• A DC motor may be coupled directly on to the "+" and "-" poles
without thermal protection. In case of high temperatures and
leaks, we recommend the use of an external relay. This relay
will switch off the motor if the motor is thermally overloaded
(see electrical diagram for DC motors, page 7).
Operation (motor only)
• If the temperature of the motor is extremely low (for instance
after transportation or stocking), allow motor to get to room
temperature before switching on the motor.
• Do not use motor for compression of liquids and dangerous
gasses, such as petrol vapour and solvents.
Important!
The compressor/vacuum pump is only suitable for
atmospheric air.
• Do not remove protection covers during operation as it may
cause electric shock or risk of other personal injury
• Ensure that motor is correct for the required air supply/vacuum flow
• If supplied with a receiver, open the outlet cock on the
receiver and connect equipment.
Preparing the motor (motor only)
• Mount the vibration dampers
• Fasten the motor to the desired place
Adjustment of pressure switch (comp.)
Warning!
If maximum pressure is exceeded, it may result in reduced lifetime.
Contact the distributor for information on operation at higher
pressure.
• All AC and DC motors may run at 100% continuous operation, but
50% operation is recommendable to prolong lifetime.
• Do not lubricate the oil-less motor with oil, as this will destroy
important components.
• Start the compressor using the 0/1 switch on the pressure
switch. The compressor will automatically switch off at the preset
pressure. If the motor does not start it may be due to pressure in the
receiver, and the motor will then start automatically when the pressure
reduces to approx. 6 bar/87 psi.
• Adjustment of pressure (fig. 1):
A: Max. pressure adjustment (cut-out)
B: Differential adjustment (cut-in)
The cut-in pressure (normally 6 bar) is set by adjustment of differential
screw B. Turn clockwise to reduce cut-in pressure. The cut-out pressure
is set by even adjustment of the two screws A. (Cut-in pr
differential = cut-out pressure). Turn clockwise to increase cut-out
pressure. The switch is normally factory set for operation at 6-8 bar
(approx. 90-120 psi).
Adjustment of vacuum switch (vacuum)
Note!
Vacuum switch is only mounted on units with receiver.
Before adjusting the vacuum switch, adjust the left screw, see (fig.11)
(turn clockwise), so that the indicator on the left scale is all
the way to the top and adjust the right screw, so that the indicator
on the right scale is all the way at the bottom as shown.
This base adjustment results in continuous operation and a
minimum differential pressure of the vacuum switch, e.g. approx.
150 mbar.
Subsequently, the exact adjustment may take place.
Adjustment of maximum vacuum (left screw)
Stop vacuum is the vacuum level in the receiver, that defines when the
vacuum pump should stop.
Start vacuum - Differential vacuum = stop vacuum
The procedure below is based on the base adjustment described
above.
1. In practice, the vacuum pump is to operate until the vacuum
required is reached (see vacuum gauge).
2. Switch off the vacuum pump by turning the left screw
counter clockwise.
3. Open the air inlet on the receiver in order to ensure
automatic start of the vacuum pump.
4. Close the air inlet in order to ensure automatic stop of the
vacuum pump at vacuum required.
5. Continue the process above (1-4) until the vacuum pump
stops at vacuum required.
Example:
If the vacuum required is e.g. 300 mbar, the vacuum pump will
not start operating until the vacuum is approx. 450* mbar. (The
difference of 150 mbar corresponds to the adjustment on the
differential scale).
Fault finding and repair (all)
Important!
Switch off and isolate from electrical supply before
removing any parts from the pump. Empty air receiver
of air before dismantling parts of compressor unit's
pressure system.
1. Compressor does not start:
a) No power from mains. Check fuses and plug.
b) Breakage or loose joints in electrical connections.
c) Defective capacitor.
d) The thermal protection has switched off the pump due
to overheating. When cooled the pump will automatically
turn on at a suitable operation temperature. Go through
the points in section 6.
e) The compressor has not been unloaded and there
is back pressure on the piston. Make sure that the
compressor is unloaded each time it stops.
f) The pump is locked..
g) Pressure in the air receiver is too high for activation
of the pressure switch. The pressure switch makes
circuit only when pressure has dropped to preset start
pressure. Empty receiver.
If the vacuum pump is fitted with receiver and vacuum switch:
h) Vacuum in the receiver. Vacuum pump will switch on when vacuum
reaches the minimum vacuum preset on the vacuum switch.
Open the inlet cock on the receiver.
2. Compressor does not start, makes a buzzing sound
followed by a clicking noise (cannot start against high
pressure):
a) Leaky non-return valve. Remove the flexible pressure
pipe and clean to find out whether air leaks from the valve.
If so, clean or replace.
3. Vacuum pump operates, but does not evacuate
sufficiently:
a) Check the piston gaskets. Replace, if necessary.
b) Defective valve plate. Contact your FLAIRMO distributor.
c) Inlet cock defective. Replace.
If the vacuum pump is fitted with receiver, vacuum filter
or vacuum gauge:
d) Vacuum filter is clogged. Clean or replace filter element.
e) Leaks in fittings, hoses or equipment. May be located by closing
inlet cock.
f) Vacuum gauge defective. Replace.
4. Compressor works, but pressure does not increase:
a) Intake filter clogged. Replace.
b) Leaks in fittings, tubes or pneumatic equipment. Check
with soapy water or by letting unit stay overnight with
disconnected mains. Pressure drop is not to exceed 1 bar.
c) Check the piston gaskets. Replace, if necessary.
d) Defective valve plate. Contact your local distributor.
e) Failure in non-return valve which is creating a flow restriction.
f)
Leaks in fittings, tubes or pneumatic equipment. Check unit by letting
unit stay overnight with disconnected mains. Vacuum switch is not to
drop to 0 bar.
5. Loud noise from compressor:
a) Dirt or failure in non-return valve. Clean or replace..
6. Motor gets very hot:
a) Leaks. See point 4b.
b) Clogged vacuum filter. See point 4a.
c) Too high ambient temperature. Ensure adequate
ventilation if the vacuum pump is installed in a cabinet.
d) Overloaded. Ensure compressor is correct model for work load.
7. Compressor starts when no air is being tapped:
a) Leaks. See point 4b.
8. Vacuum pump starts when no vacuum is being used:
a) Leaks. See point 4f.