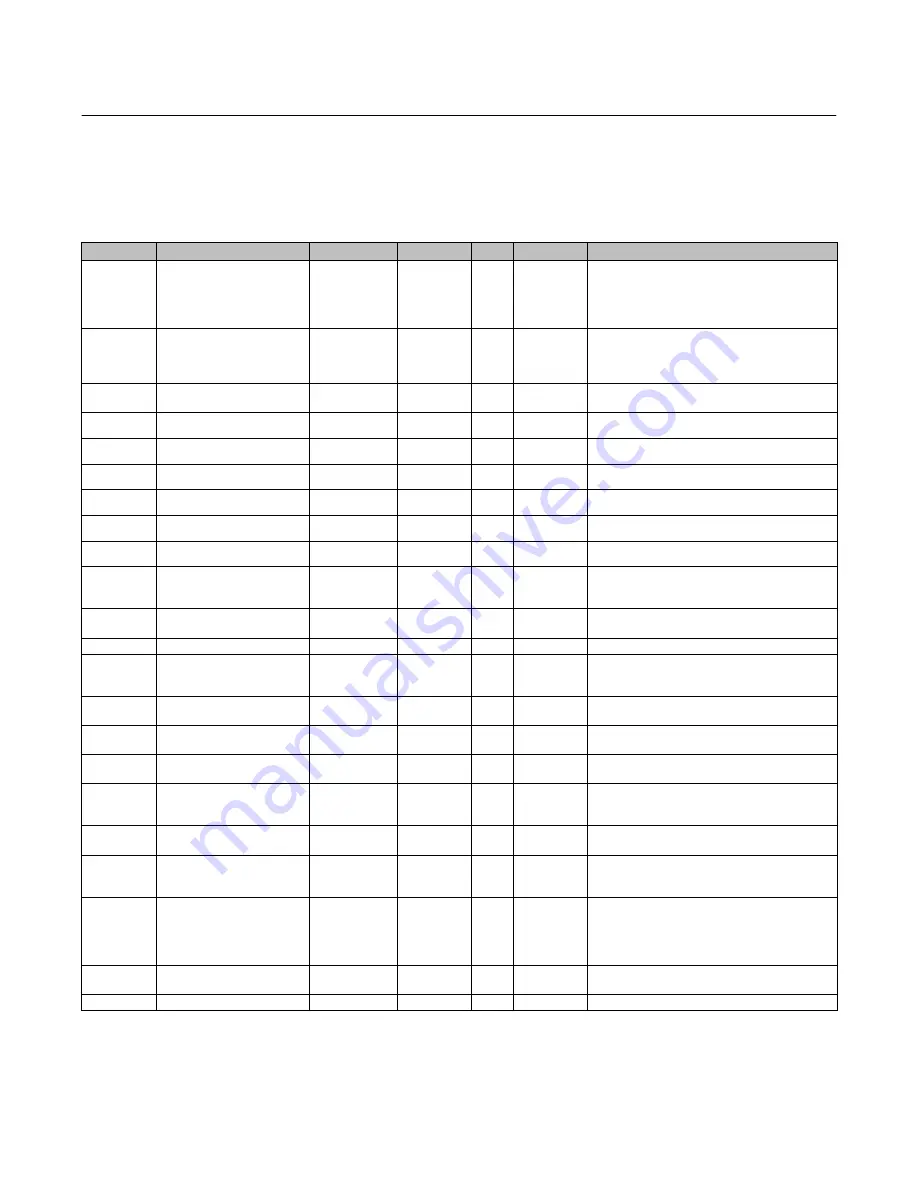
Instruction Manual
D104331X012
easy-Drive 200L
December 2018
23
Appendix A - Modbus
A.1 Register Summary
Table 3. easy-Drive 200L Modbus Map
Type
Name
MB Register
Default
R/W
Values
Notes
unit16
Modbus position command
(100=10.0%)
40001
0
R/W
0-1000
Modbus command value with one implied decimal
place (1000=100.0%). R/W at all times but only used in
Modbus control mode. In on/off mode 0-499 will
result in a move to 0% and 500-1000 will result in a
move to 100%.
unit16
Digital output
40002
0
R/W
0,1
0=no voltage supplied to terminals,
1=voltage supplied to terminals
(Only used when output setup is set for Remote
controlled)
unit16
Reset error codes
40003
0
R/W
0,1
Value of 1 will clear faults.
Will automatically set back to 0.
unit16
RESERVED
40004
unit16
RESERVED
40005
unit16
RESERVED
40006
unit16
RESERVED
40007
unit16
RESERVED
40008
unit16
RESERVED
40009
unit16
Actual position
(100=10.0%)
40010
0
R
0-1000
Present position of the actuator relative to span with 1
implied decimal place (1000=100.0%). Valid for all
control modes.
unit16
Commanded position
(100=10.0%)
40011
0
R
0-1000
Present position command of the actuator relative to
span (1000=100.0%). Valid for all control modes.
unit16
Diagnostic Flags
40012
0
R
0-65535
Bit flags - see chart
unit6
Digital status
40013
0
R
0 - 1
0=no connection between terminals,
1=connection between terminals (Status of digital
input or output)
unit32
Total Running Time (min)
40014, 40015
0
R
4294967296
Total number of minutes the actuator has been
powered on since time has been reset
unit32
Total Open Time (min)
40016, 40017
0
R
4294967296
Total number of minutes the actuator has been at
100% of travel since time has been reset
unit32
Total Closed Time (min)
40018, 40019
0
R
4294967296
Total number of minutes the actuator has been at 0%
of travel since time has been reset
unit32
Number of Closed (cycle count)
40020, 40021
0
R
4294967296
Total number of close cycles the actuator has
performed since reset.
One open/close cycle counts as 1.
unit32
Number of Power Cycles
40022, 40023
0
R
4294967296
Total number of times the actuator
has been powered on.
unit32
Number of Movements
40024, 40025
0
R
4294967296
Total number of movements the actuator has
performed. Move must be at least 5% of rated travel
for cycle to increment.
unit16
Analog input control value
40026
0
R
0-2400
Value of the analog signal in mA with 2 implied
decimals. In analog control mode, this is the
command value and is subject to the analog settings in
registers 40046 to 40059. Always active but a slower
refresh rate when unit is not in analog control mode.
unit16
Incoming voltage
40027
0
R
0-350
Diagnostic register - value of incoming voltage with 1
implied decimal.
unit16
Latch Open State
40028
0
R
0 - 1
Normally open latch state
-continued-