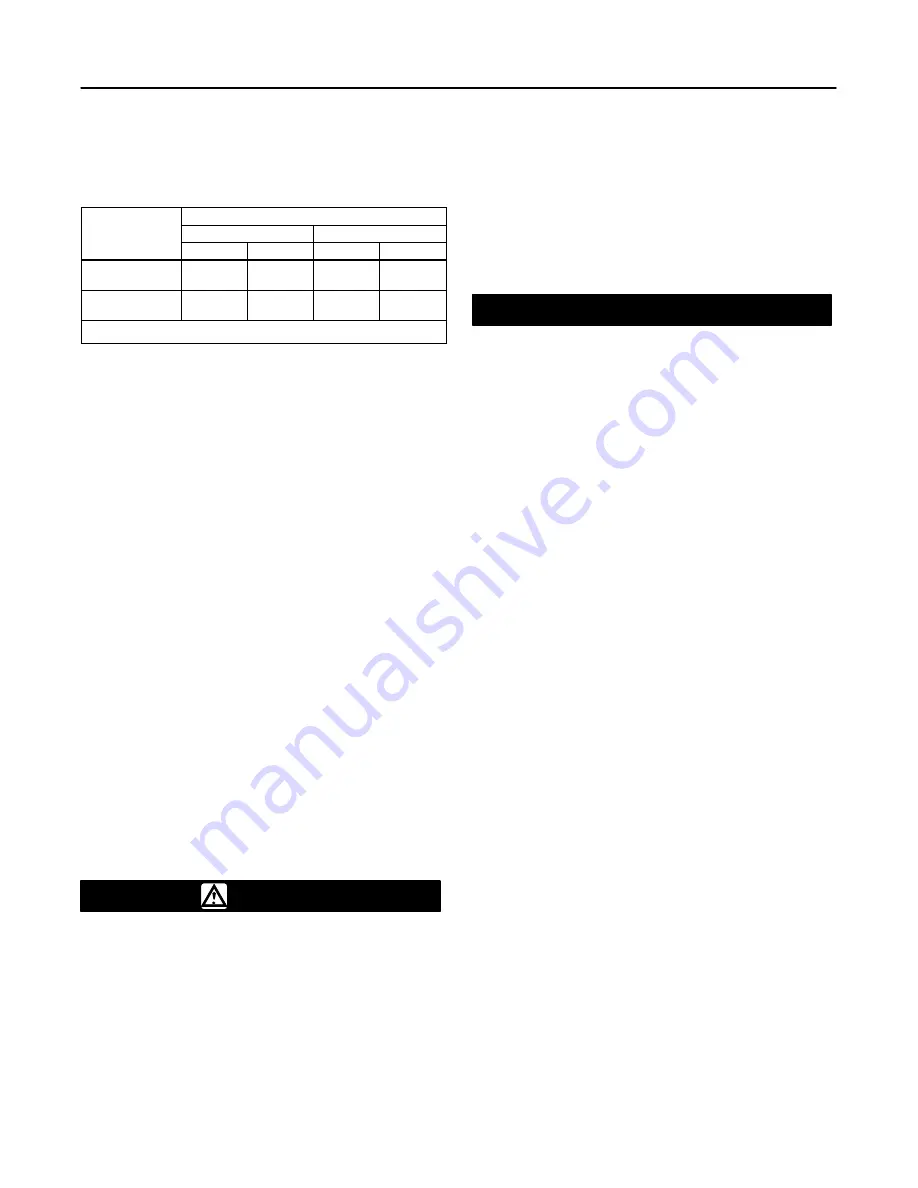
Design CV500
12
feeler gage to measure between the parts as shown in
figures 11 and 12, making certain the necessary
clearance exists. Compare the measured gap to the
clearance in table 5; proceed as follows:
Table 5. Assembly Clearance
PROCESS
SEAT RING AND RETAINER CLEARANCE
PROCESS
TEMPERATURE
mm
Inches
TEMPERATURE
Minimum
Maximum
Minimum
Maximum
To 260
_
C
(500
_
F)
(1)
0.08
0.30
0.003
0.012
Over 260
_
C
(500
_
F)
(2)
0.20
0.30
0.008
0.012
1. Standard Trim
2. Special High Temperature Trim
D
If the measured clearance is within table values,
proceed to the next step.
D
If the measured gap is larger than the maximum,
tighten the retainer—apply more torque than that listed
in figure 7, if necessary, until the clearance is within
maximum and minimum values.
D
If the measured clearance is smaller than the
minimum, remove the retainer, seat ring, and face
seals, clean the parts, and reassemble so as to obtain
the necessary minimum clearance.
10. Perform the Adjusting Actuator Travel procedure
and then install the control valve in the pipeline.
Replacing Ball, Shaft, and Bearings
Perform this procedure to replace the ball (key 2),
expansion pin (key 9), taper pin (key 10), drive shaft
(key 3), follower shaft (key 38), groove pins (key 39),
or bearings (keys 6 and 42). These parts are
independently replaceable; for example, installing a
new ball does not require replacing a reusable valve
shaft or expansion pin assembly. Key numbers refer to
figure 11 for 3 through 8-inch sizes and to figure 12 for
10 and 12-inch sizes unless otherwise indicated.
Disassembly
WARNING
To avoid personal injury resulting from
contact with edges of the V-notch ball
(key 2) and seat ring (key 4) during ball
rotation, stay clear of its edges when
rotating the ball. To avoid damage to
tools, valve parts, or other items
resulting from V-notch ball rotation,
keep tools and other property away from
the edges of the ball.
When the actuator is removed from the
valve, the ball/shaft assembly may
suddenly rotate, resulting in personal
injury or property damage. To avoid
injury or damage, carefully rotate the
ball/shaft assembly to a stable position
in the valve body after the actuator is
disconnected.
CAUTION
To avoid increased leakage, increased
valve component wear or possible
damage to the valve body (key 1), ball
(key 2), drive shaft (key 3), follower shaft
(key 38), and bearings (keys 6 and 42)
resulting from a sharp blow to the
actuator or valve parts, use a wheel
puller to separate the actuator parts
from the valve drive shaft.
Do not drive the actuator parts off the
valve drive shaft since this could move
the valve bearings, shafts, and ball away
from proper alignment, causing
improper seating of the ball. Such
misalignment may result in damage to
valve components if the valve is
returned to service without disassembly
and inspection of the ball alignment.
1. Isolate the control valve from the line pressure,
release pressure from both sides of the valve body,
and drain the process media from both sides of the
valve. If using a power actuator, also shut-off all
pressure lines to the power actuator, release all
pressure from the actuator. Use lock-out procedures to
be sure that the above measures stay in effect while
you work on the equipment.
2. Remove the actuator cover. Note the actuator
orientation with respect to the valve body and the lever
orientation with respect to the valve drive shaft (see
figure 3). Remove the lever but do not loosen the
actuator turnbuckle adjustment. Remove the actuator
mounting screws and nuts, and remove the actuator. If
necessary, refer to the actuator instruction manual for
assistance.
3. With the valve body (key 1) out of the pipeline,
loosen the packing nuts (key 16). If the packing is to
be reused, do not remove it. However, Fisher
recommends that the packing be replaced whenever
the drive shaft is removed.
Содержание Design CV500
Страница 26: ...Design CV500 26...
Страница 27: ...Design CV500 27...