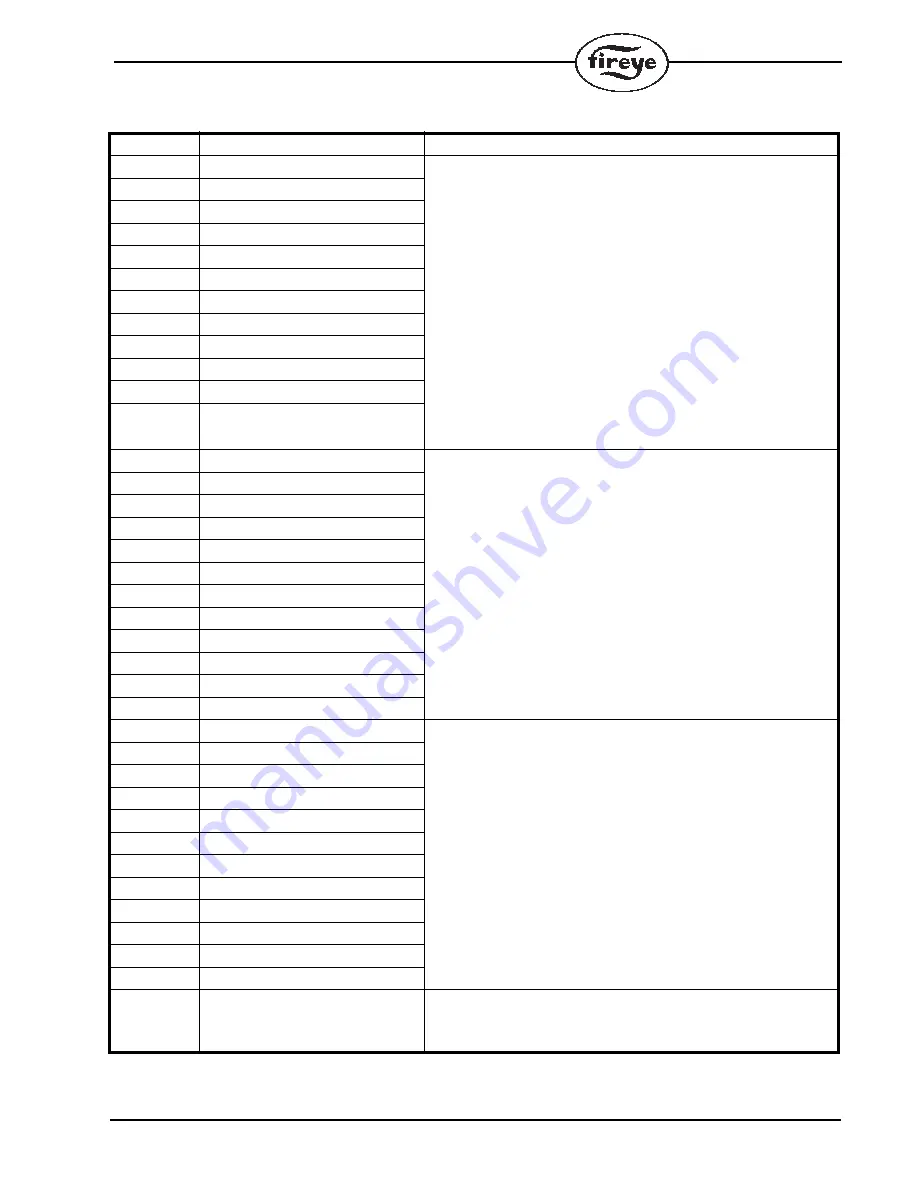
75
®
Fault Listing
NUMBER
NAME
DESCRIPTION
F1
Fuel 1 incorrect position
A drive positioning fault has occurred, which will cause a safety shutdown of the
burner. This fault has occurred for one of the following reasons:
• During close position prove, when a drive stops at a position which is outside the
close set position by more than five degrees.
• During purge position prove, when a drive stops at a position which is outside the
purge set position by more than five degrees.
• During pre-purge, ignition or post-purge, when a drive moves from its setpoint.
• During modulation, when a drive is not at its correct setpoint as defined by the com-
missioned fuel/air ratio for the selected profile.
A drive is defined as having moved from its setpoint if its positional error is more
than 1º for 15s, or more than 5º for 1s. For positional errors between 1º and 5º, the
detection time is variable between 15s and 1s.
Inverters have a different error tolerance during modulation. See option parameter
22.2 for details.
Frequent positioning faults are usually caused by one of the following problems:
• Worn, dirty or unsuitable (e.g. wire-wound) potentiometers used for servomotors
feedback.
• Unsuitable lead drive selection - two adjacent profile points having a small change in
lead drive position, and a large change by a non-lead drive.
Subset: burner status
F2
Fuel 2 incorrect position
F3
Fuel 3 incorrect position
F4
Option 1 drive incorrect position
F5
Option 2 drive incorrect position
F6
Option 3 drive incorrect position
F7
Air damper 1 incorrect position
F8
Air damper 2 incorrect position
F9
Air damper 3 incorrect position
F10
Air damper 4 incorrect position
F11
Option 4 drive incorrect position
F12
Option 5 drive incorrect position
F13
Fuel 1 feedback failed
A drive feedback fault has occurred, which will cause a safety shutdown of the burner.
This fault has occurred for one of the following reasons:
• A potentiometric feedback signal from a servomotor is outside the range of 0-5v.
• A 4-20mA feedback signal from a inverter drive is below 3.5mA, above 21.0mA or
has an incorrect polarity.
Subset: 1 – current below 3.5mA, 2 – current above 21mA or voltage above 5.3v
F14
Fuel 2 feedback failed
F15
Fuel 3 feedback failed
F16
Option 1 drive feedback failed
F17
Option 2 drive feedback failed
F18
Option 3 drive feedback failed
F19
Air damper 1 feedback failed
F20
Air damper 2 feedback failed
F21
Air damper 3 feedback failed
F22
Air damper 4 feedback failed
F23
Option 4 drive feedback failed
F24
Option 5 drive feedback failed
F25
Fuel 1 illegal speed
The specified drive is outside the allowable speed range of 10s/90º to 60s/90º.
If the drive is an inverter, adjust the acceleration and deceleration times accordingly.
Before the pre-purge starts, all required drives are moved from their lowest positions
(closed set points) to their highest positions (purge set points).
During this time, a speed measurement, which is required for the modulation control
algorithm, is made for each drive.
If any drive is found to be outside the allowable speed range for reliable control, an
incorrect speed fault occurs and the unit will be forced into a safety shutdown state.
• Is the wiring correct?
• Has the triac output failed?
• Is the +5v / +15v potentiometer supply voltage selected correctly?
Subset: 1 – Too fast, 2 – Too slow
F26
Fuel 2 illegal speed
F27
Fuel 3 illegal speed
F28
Option 1 drive illegal speed
F29
Option 2 drive illegal speed
F30
Option 3 drive illegal speed
F31
Air damper 1 illegal speed
F32
Air damper 2 illegal speed
F33
Air damper 3 illegal speed
F34
Air damper 4 illegal speed
F35
Option drive 4 illegal speed
F36
Option drive 5 illegal speed
F39
PSU board voltage reference fault
The PSU board has an incorrect on-board voltage reference level.
• Is the PSU board installed correctly?
• Are any inputs to the PSU board outside their specified limits? For example, is the
modulation input (PA17) at more than 5V or less than 0V?