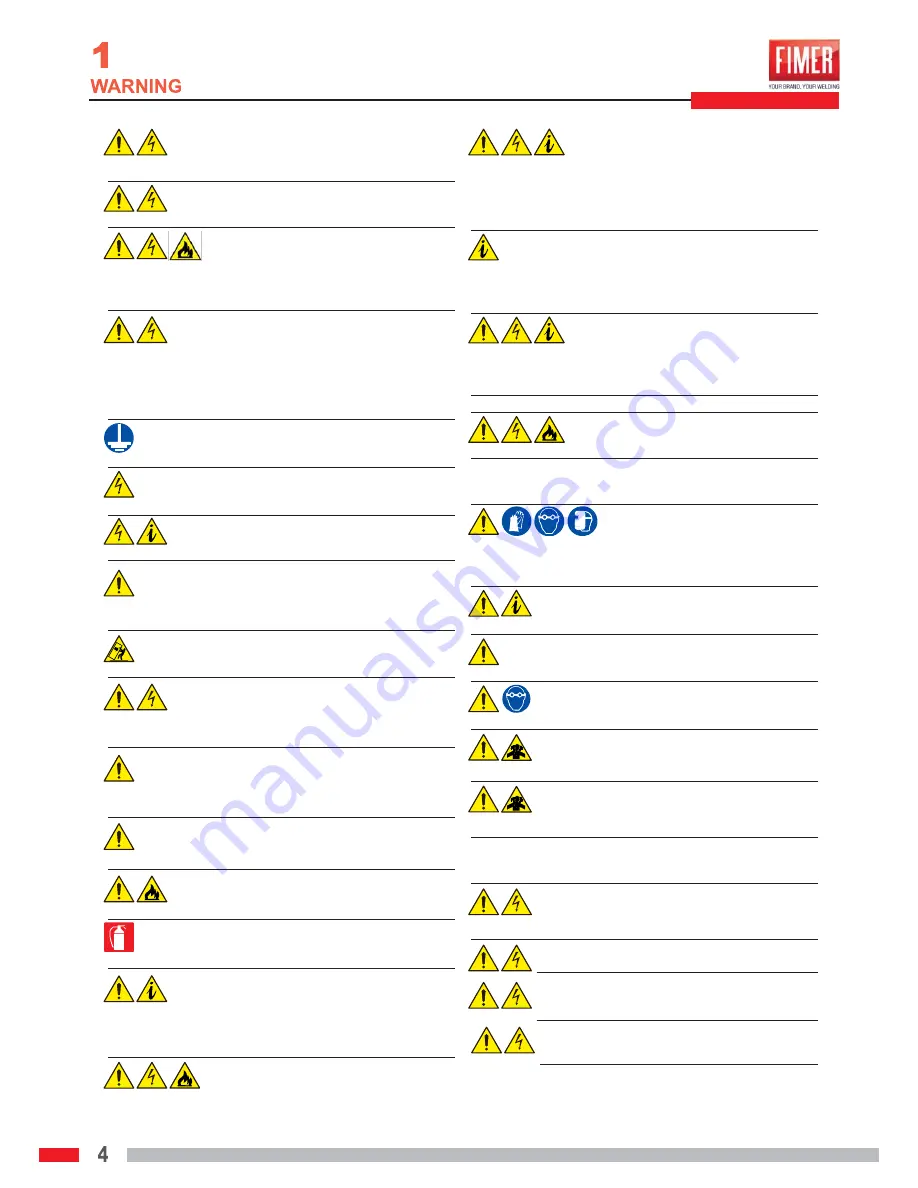
FOREIGN OBJECTS
Never block the air vents with
foreign objects and avoid any contact with liquids.
Clean using just a dry cloth. These safety precautions
apply even when the unit is switched off.
WEIGHT LOADS
The upper part of the Welder was
not designed to withstand heavy loads. Never stand
on the unit.
CABLE GAUGES
Check that all cables are
appropriately gauged for the input power required
by your specific Welder. This precaution applies
also to extension cables, if used. All extension cables must be
straight. Coiled cables can overheat, becoming dangerous. Twisted
or coiled cables can also cause Welder malfunction.
OVERLOAD PROTECTION
Check that the power
source supplying the Welder carries the correct voltage
and is safety-protected. The power switch must open
all the power supply circuits. (If a single-phase connection is used,
both the live and the neutral poles must be open. If a three-wire
connection is used , all three poles must be open. Four-wire circuits
require all poles and neutral open). Time-delayed fuses or K-
standard circuit breakers should be used.
EARTHING
If the Welder was not already supplied with a
plug, connect the earth wire first. When removing the plug,
disconnect the earth wire last.
PLUG AND POWER SUPPLY
If the Welder already has a plug
attached, check that it is appropriate for the wall-socket you
intend using. Never tamper with the power cable.
CABLE COLOURS
The green-yellow wire is for earthing.
(Don’t use it for anything else !)
RELOCATION 1
Some Welders are extremely heavy therefore
care should be taken when relocating the unit. Check the floor
or platform weight load limitations before relocating the unit if
the Welder is to be used, even only temporarily, in a non-industrial
environment
RELOCATION 2
Never store or move the Welder in an inclined
position or on its side.
INSTALLATION ENVIRONMENT
The equipment is not
suitable for use in washrooms, shower cubicles, pool
areas or similar environments. If you are obliged to use
the unit in such areas, turn off all water supplies and check the area
has been evacuated.
OPERATING AND/OR INSTALLATION ENVIRONMENT 1
The
Welder was not designed for installation or use in areas where it could
be subject to blows or vibration, such as road-vehicles, railway carriages,
cable-cars, aircraft, ships or boats or similar environments (including cranes,
conveyor-carriers or any other mobile equipment prone to vibration)
OPERATING AND/OR INSTALLATION ENVIRONMENT 2
The Welder should never be used or stored in the rain or in
snow.
OPERATING AND/OR INSTALLATION ENVIRONMENT
3
Never use the Welder in an explosive, corrosive,
abrasive or saline environment.
EXTINGUISHER
Always place an approved fire extinguisher in the
immediate vicinity of the work area. Fire extinguishers should be
checked regularly.
LOCATION
Place the Welder well away from heat sources.
Place the Welder in a well-ventilated environment. Place
the Welder in a safe, protected area. It must not be installed
outdoors. Do not install the Welder in dusty environments. Dust can get
into the inner parts of the unit and inhibit cooling. The Welder must be
positioned on a flat, stable surface that extends further than the units own
dimensions in all directions.
CLEAN LOCATIONS
The installation area must
be kept clean and dry to be sure the Welder fans
do not draw in small objects or liquids. Not only
could the equipment malfunction but a serious risk of fire outbreak could
be created.
REPAIRS
Never attempt to repair the Welder
yourself. Always refer to the manufacturer or an
authorized repairer. All warranty provisions will
immediately become null and void if any repair, or attempt to repair,
not specifically authorized in writing or handled by the constructor is
carried out. Furthermore, the constructor will accept no responsibility
for any malfunction or damage resulting as a consequence of such
unauthorized action.
TECHNICAL ASSISTANCE
The Welder must be taken to an
authorized Technical Assistance Centre if the equipment has
been damaged in any way or if any one of the following events
occurs : liquid infiltration; damage caused by falling objects; exposure
to rain or humidity (exceeding the specified limits); malfunction; per-
formance failure or if the equipment has been dropped.
SPARE PARTS
Use only manufacturer-recom-
mended spare parts. Other spare parts could
cause equipment malfunction. The use of non-
original spare parts will also result in the warranty provisions becoming
null and void, releasing the manufacturer from any responsibility for
malfunction or damage resulting as a consequence of such action.
WELDING OPERATION SAFETY INSTRUCTIONS
WELDING OPERATION SAFETY INSTRUCTIONS
CAUTION !
Welding processes can be dangerous
for the operator and bystanders if the safety
warnings and instructions are not heeded.
PERSONNEL PROTECTION
PERSONNEL PROTECTION
Together with the previous instructions, the following precautions
should be strictly observed
PROTECTION MASK
Wear a protective
non-flammable welding mask to protect
your neck, your face and the sides of
your head. Keep the front lens clean and replace it if it is broken
or cracked. Place a transparent protection glass between the
mask and the welding area.
CLOTHING
Wear close-fitting, closed, non-flammable,
pocketless clothing.
VENTILATION
Weld in a well-ventilated environment that
does not have direct access to other work areas.
EYE PROTECTION
NEVER look at the arc without
appropriate eye protection.
FUMES AND GASES 1
Clean away paint, rust or any
other dirt from the item to be cut to avoid the creation
of dangerous fumes.
FUMES AND GASES 2
NEVER cut on metals containing
zinc, mercury, chromium, graphite, heavy metals,
cadmium or beryllium unless the operator and the bystan-
ders use appropriate air-supplied respirators.
HIGH VOLTAGE PROTECTION
HIGH VOLTAGE PROTECTION
Together with the previous instructions, the following precautions
should be strictly observed
CONFINED SPACES
When welding in small environ-
ments, leave the power source outside the area where
welding will take place and attach the grounding clamp
to the part to be welded.
HUMIDITY
Never weld in wet or humid environ-
ments.
DAMAGED CABLES
Never use damaged cables.
(This applies to both the power and the welding
cables.)
DAMAGED CABLES
Never remove the unit side panels.
If the side panels can be opened, always checked they
are closed tightly before starting any work.
FIRE PREVENTION
FIRE PREVENTION
Together with the previous instructions, the following precautions
should be strictly observed. Welding operations require high
temperatures therefore the risk of fire is great.
Содержание 5T5.555.452
Страница 1: ...910 100 539GB REV01 Ed 2016_05_03 KRONOS 500 dual pulse INSTRUCTION MANUAL ...
Страница 5: ...ENGLISH ...
Страница 6: ...KRONOS 500 dual pulse 5T5 555 452 ...
Страница 10: ...1 2 5 8 7 6 10 11 13 15 17 18 3 9 12 16 14 4 ...
Страница 11: ...ENGLISH 25 26 27 30 19 21 20 22 23 24 28 29 ...
Страница 12: ...1 2 3 4 5 6 7 8 9 10 20 19 18 17 16 15 14 13 12 SD 11 a b a b b a b b a b ...
Страница 13: ...ENGLISH DSF DUAL PULSE PULSE a b c d a b d c b a d b a 2a function ...
Страница 14: ...a b b a a b c ...
Страница 15: ...ENGLISH ...
Страница 16: ......
Страница 17: ...ENGLISH A B C D E F G H ...
Страница 19: ...ENGLISH ...
Страница 20: ......
Страница 21: ...ENGLISH ...
Страница 22: ......
Страница 23: ...ENGLISH ...
Страница 24: ...Torch Trigger Torch Trigger T T a b DSF ...
Страница 25: ...ENGLISH ...
Страница 26: ...DSF b b ...
Страница 27: ...ENGLISH ...
Страница 28: ......
Страница 29: ...ENGLISH ...
Страница 30: ......
Страница 31: ...ENGLISH Torch Trigger Torch Trigger a b Torch Trigger T T T T Torch Trigger a b ...
Страница 32: ......
Страница 34: ......
Страница 35: ...ENGLISH ...
Страница 36: ......
Страница 37: ...ENGLISH ...
Страница 39: ...ENGLISH ...
Страница 40: ......
Страница 41: ...ENGLISH ...
Страница 42: ......
Страница 43: ...ENGLISH ...
Страница 44: ......
Страница 45: ...ENGLISH ...
Страница 46: ......
Страница 47: ...ENGLISH ...
Страница 48: ......
Страница 51: ...ENGLISH ...