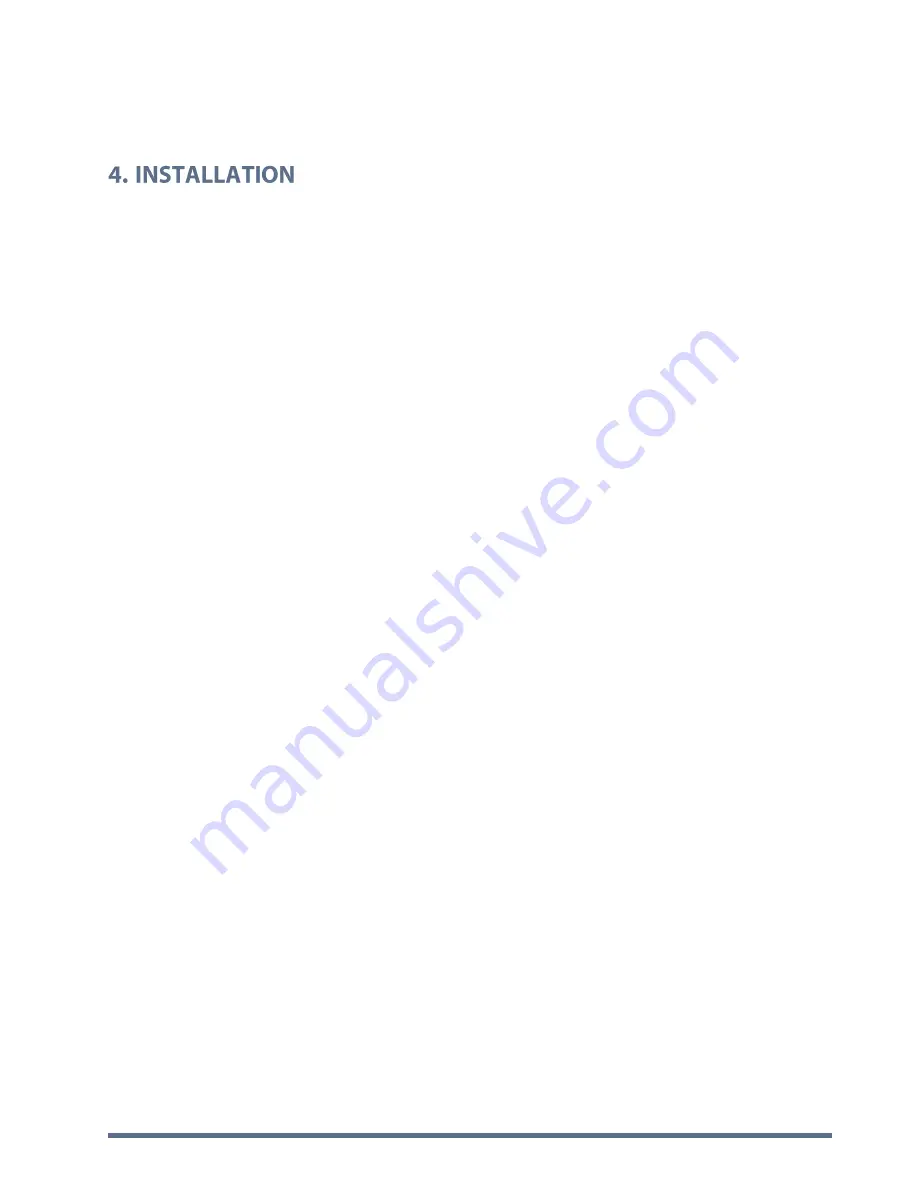
Doc. P/N 8.8128.00.3
Rev. 3 / July, 2020
PAGE / 9
1.
Place gaskets on top and bottom of assembly. Gaskets subject to relaxation or cold flow are not
recommended for use with the holder assembly. Spiral wound gasket are not suitable for sizes 1” (DN25).
Spiral wound gaskets may not be suitable for all flange ratings for sizes 2” (DN50) to 4” (DN100). Consult
factory.
2.
Carefully slide bursting disc assembly between companion flanges.
WARNING: For installations directly under a pressure relief valve that utilize a spool/spacer, ensure spool/spacer is
installed between the outlet of the holder and inlet of the pressure relief valve. SRLO, XLO and ATLAS-LO holder
sizes 12” and smaller are not suitable for direct-coupling to a pressure relief valve; they must utilize a high-profile
hold down, spool or a suitable spacer. Atlas holders 14” and larger require a spool piece if under a pressure relief
valve. Refer to Fike Technical Bulletin TB8105 for code requirements.
WARNING: Double check the orientation of the bursting disc. Verify flow arrows on the holder and disc tag are
pointed in the same direction as process flow.
3.
If necessary, clean threads on studs and nuts. Wire brushing is usually sufficient. Oil studs with a light oil
such as SAE grade 20. Do not use studs and nuts that show evidence of galling.
4.
Finger-tighten flange studs and nuts.
5.
Refer to Appendix A to obtain torque value. Locate nominal disc size and flange rating. This is the required
torque value.
6.
Using the crisscross pattern shown in Figure 8, apply torque in 4 steps of 25% increments. For larger
quantities of bolts than shown below, use a similar crisscross pattern. For example, if the torque required
from Table 1 is 100 ft-lb, the torque should be applied in 25 ft-lb increments. Apply 25 ft-lb to each nut,
then 50 ft-lb, then 75 ft-lb, etc. For larger quantities of bolts than shown below, use a similar crisscross
pattern.